Across the broad spectrum of manufacturing, few processes offer the efficiency, versatility and precision that thermoforming does. Its impact can be seen in nearly every aspect of modern life—medical food packaging electrical… But as an industry that is constantly looking to the future, thermoforming should not just produce more in the future, but produce smarter. This blog post takes an in-depth look at what’s next for thermoforming: looking at trends like sustainability issues, as well as the technological advancements and innovations that are reshaping this important technology.
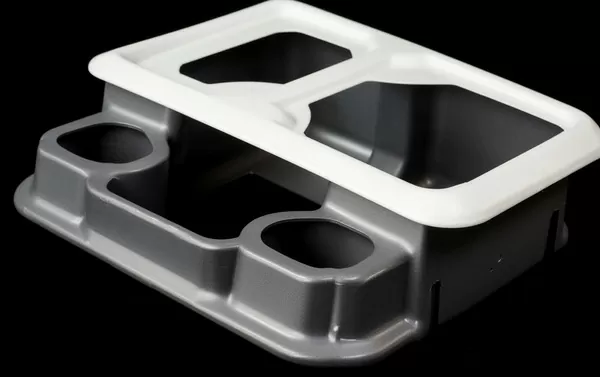
Thermoforming Process
Thermoforming, also known as vacuum forming or pressure forming, is a plastic manufacturing technology. The main principle is to heat a flat hard plastic sheet to soften it, then use vacuum to adsorb it to the surface of the mold, and then cool it into shape. It is widely used in plastic packaging. , lighting, advertising, decoration and other industries. There are several thermoforming methods used in actual production: differential pressure molding, cover molding, plunger-assisted molding, suction back molding, opposite mold molding, female mold and male mold thermoforming, thin gauge thermoforming, heavy gauge(thick gauge) vacuum forming and twin sheet forming.
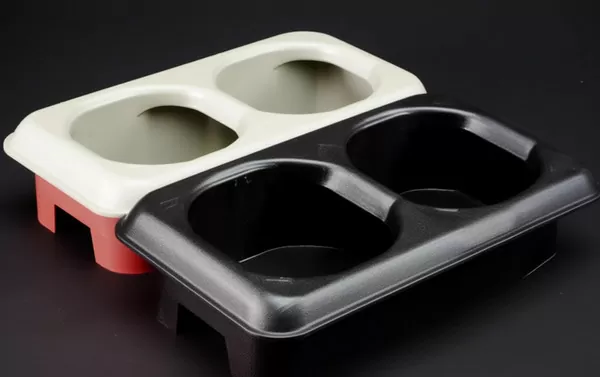
Importance of Thermoforming in Various Industries
Thermoforming plays a key role in various industries. It makes components by heating plastic sheets until they become pliable and then shaping them into their final shape. But thermoforming does much more than that: it helps generate ideas for new products and even changes entire markets. Here, we look at the applications of thermoforming in certain industries and the critical role it plays.
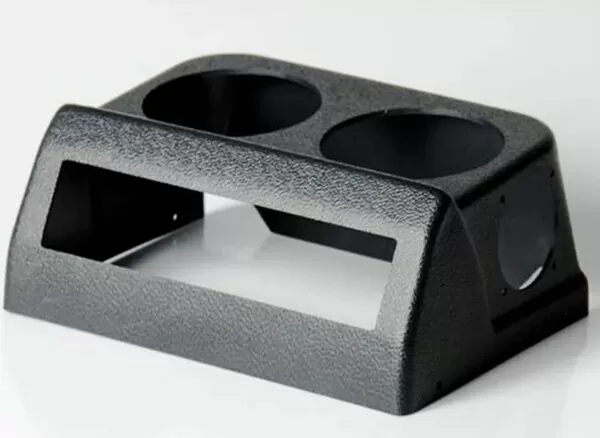
Medical Industry
Thermoforming plays a vital role in the medical field, enabling the creation of sterile, customized packaging solutions for medical devices and equipment. This packaging must meet strict regulatory requirements designed to ensure that the packaging or device remains free of contamination until final use. Thermoformed trays and blisters are widely used by healthcare professionals because they are strong, clear, and can tightly wrap odd-shaped items to provide an extra level of protection.
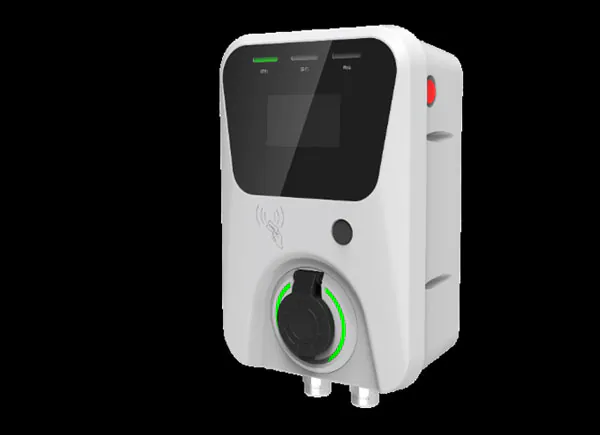
Automotive Industry
The automotive industry now relies heavily on thermoforming to manufacture a variety of parts for both the interior and exterior of vehicles. With this technology, items such as dashboards, door panels and even bumpers can be manufactured. Thermoforming offers an economical way to create lightweight parts that help improve overall fuel efficiency while lowering the carbon footprint of each vehicle. In addition to these benefits, customers are requesting more unique interiors and exteriors made from materials with a range of “aesthetic versatility”, meaning designers have the flexibility to be creative in how they look and work. Innovation.
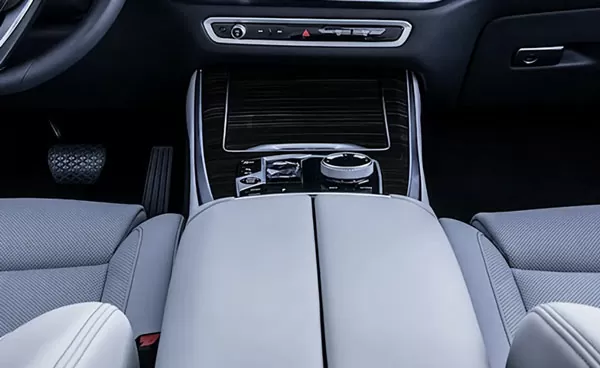
Food Packaging Industry
Thermoforming is crucial in the food packaging world because it allows the creation of transparent, durable items that not only effectively display food, but also protect it. Whether it’s a cup, tray, clamshell container or custom plastic packaging. When it comes to maintaining hygiene standards throughout the life cycle of a product, there is no better technology than thermoforming! Its inherent airtightness also supports the trend towards more secure, tamper-proof packaging, reflecting consumer demands for safety and quality.
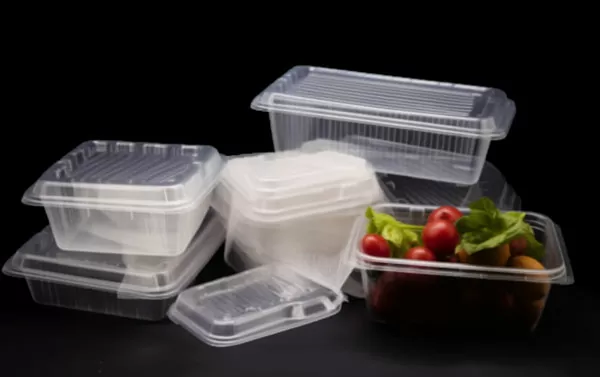
Aerospace and Defense
Thermoforming plastic manufacturing process is also used in the aerospace and defense sectors to produce lightweight, strong materials for structural and non-structural parts. This technology enables the creation of complex parts that can withstand harsh conditions, such as at high altitudes or high speeds. For example, thermoformed parts can be used in cabin interiors, seat components, and even potentially life-saving things like protective shields around radar units (radomes).
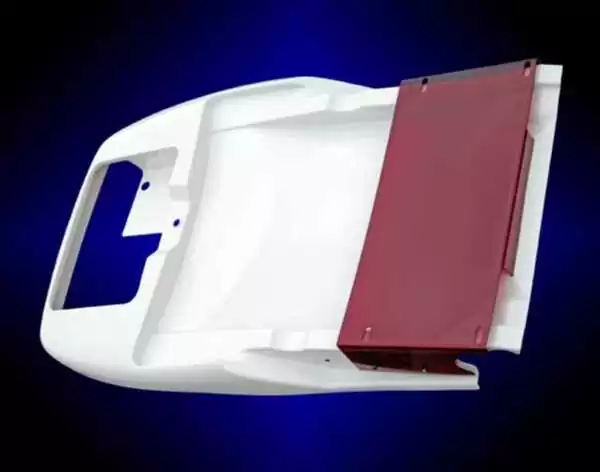
Retail and Display
Thermoforming is an extremely versatile process that has found a place in the retail and display world. It is used to create point-of-sale displays, signage and packaging that capture consumer attention. Not only are these products visually stimulating, but due to their durable yet lightweight nature, they are also great as marketing tools! Additionally, thermoformed plastics can be molded into complex shapes, which means you can see completely different or various styles of designs, creating unique and eye-catching displays that stand out in a competitive retail environment.
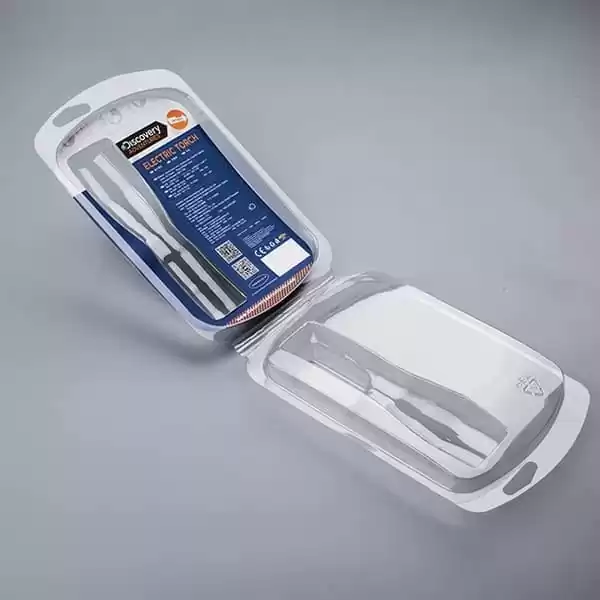
Environmental Considerations
The thermoforming process is developing rapidly, with sustainability playing an increasingly important role. To reduce their impact on the environment, many industries are now favoring recyclable resources and looking into bio-based plastics: the good news is that this is easily achieved with thermoforming. In addition, advances in this technology mean it is easier to recycle waste materials, thus helping to further reduce waste while supporting the wider industry to move towards a more environmentally friendly direction.
In comclusion, thermoforming has proven to be a valuable tool in various fields. Its ability to adapt designs and streamline manufacturing processes while reducing costs and increasing material usage efficiency makes it the preferred method for many products today. As the industry continues to innovate and drive more sustainable practices, thermoforming may remain at the forefront of manufacturing solutions that continue to adapt to the changing needs of businesses and consumers.
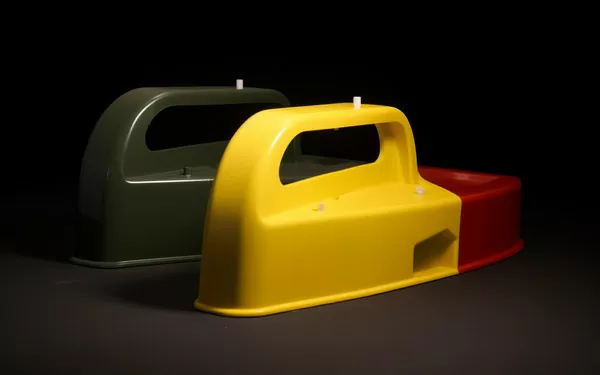
The Current State of Thermoforming
Before we delve into the future and advancements of thermoforming, it’s important to first understand the basics of thermoforming and its current uses. Thermoforming is the process of heating a plastic sheet to a pliable state, and then adsorbing the soft plastic material into a mold through vacuum adsorption to form a specific shape, and then trimming it to form the final product. Thermoforming is widely used in various fields such as packaging, automotive, medical and aerospace.
1. Thermoforming Today
The variety of products produced through thermoforming is incredible. Thermoformed parts surround us all: from the packaging we see on our daily purchases, to the interior panels and parts of luxury cars or aircraft. It’s also an increasingly advanced process; some production lines are now producing millions per year at an astonishing rate!
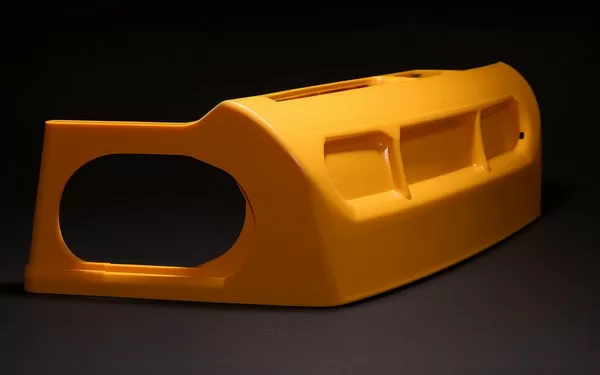
2. Competitive Edge
One of the key reasons why thermoforming is so popular is that it provides an inexpensive way to produce large items. The machines used in this type of manufacturing tend to be less expensive than those required for injection molding or other molding techniques. Although the overall cost of making some molds is still high, it will still be cheaper and faster to make than traditional methods. Thermoforming therefore appeals not only to companies who want to innovate cheaply by designing new products, but also to those who need a quick turnaround of orders: there is no other option that offers everything you need at an acceptable price!
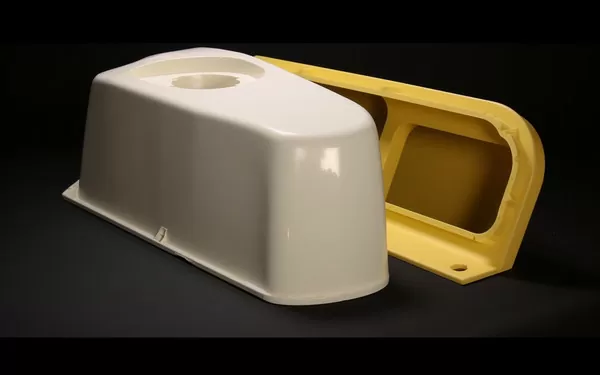
Emerging Trends in Thermoforming
1. Sustainability Initiatives and Eco-Friendly Materials
The pressure forming industry is not immune to global sustainability trends. Instead, companies in the industry are actively looking for greener alternatives to traditional plastics – materials that break down naturally over time or can be recycled and reprocessed repeatedly without causing pollution. Recently some manufacturers have also begun efforts to adopt more sustainable practices, such as installing solar panels so that their machines run solely on sunlight (thereby reducing dependence on fossil fuels), while also trying to create closed loops in which normal production processes Any waste produced is reprocessed into materials that can be used again.
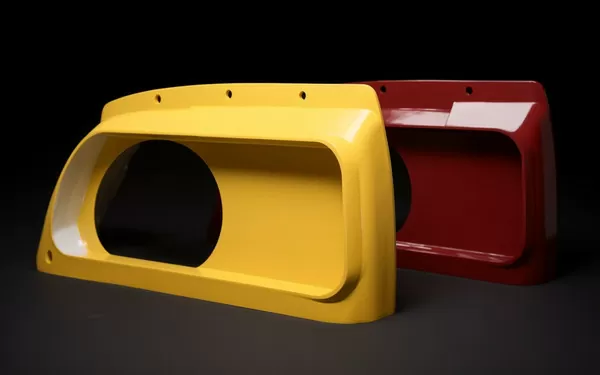
2. Automation and Artificial Intelligence in Thermoforming Processes
The current craze of the Fourth Industrial Revolution, also known as Industry 4.0, automation and artificial intelligence are more than just buzzwords. These technologies are changing manufacturing by introducing digital elements: this makes factories more efficient while also making them smarter! In the field of thermoforming, as robotics technology advances, robots can now handle parts with great care; another approach is to use algorithms that not only detect when a machine needs maintenance, but actually predict it before it becomes a problem.
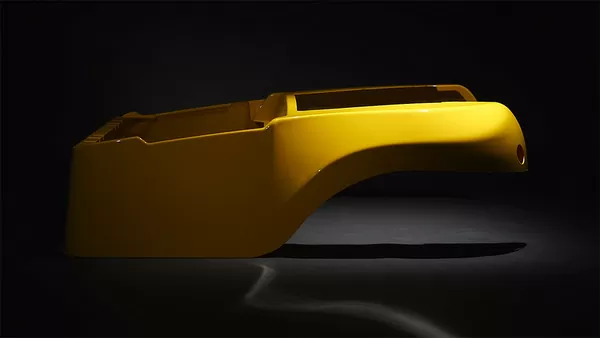
3. Customization and Rapid Prototyping Capabilities
Thermoforming is meeting the needs of today’s consumer by providing rapid prototyping services; this enables quick changes to be made during the design phase. Products can now be tailored specifically towards each person – something which has never before been possible in certain industries (which used to only produce things on an industrial scale). As a result, there are fresh opportunities available within some sectors: ones where individuality reigns supreme.
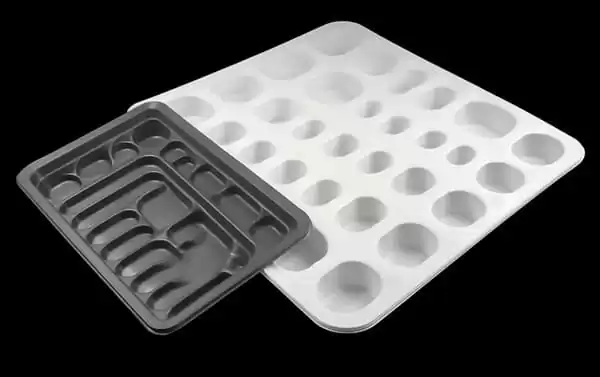
Innovations in Thermoforming Technology
In the future, thermoforming will definitely have superior processes and advantages than today. Here are some of the future breakthrough innovations that may one day become the standard for thermoforming plants everywhere.
1. Advanced Materials with Enhanced Properties for Thermoforming
In the future, thermoforming manufacturers may use materials that can change their color, texture or strength based on environmental cues or user commands. The development of self-healing plastics could similarly upend how we think about the longevity of everyday objects: Imagine fewer replacement parts for broken items and less overall demand for single-use items because the surrounding materials are stronger.
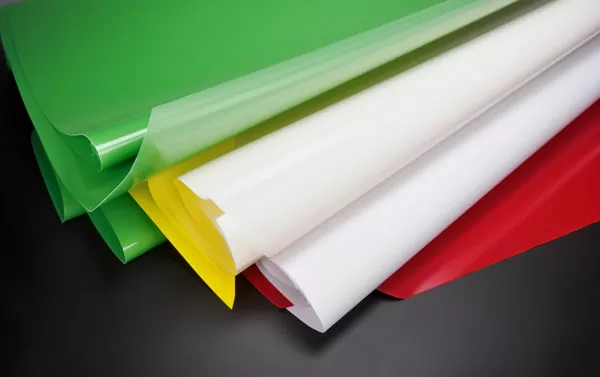
2. Integration of 3D Printing with Thermoforming
Combining 3D printing with thermoforming has the potential to revolutionize product customization. Combining 3D printing with thermoforming allows for smoother creation of prototypes and production of high-quality parts, resulting in shorter lead times and an overall smoother design process. The combination of these two technologies is likely to improve the end-user experience. Additionally, combining 3D printing with thermoforming may offer significant advantages in terms of cost and time for mold making.
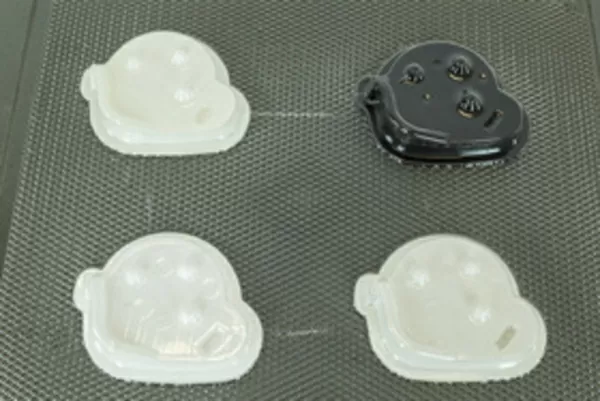
3. Predictive Analytics for Optimizing Thermoforming Operations
The future of thermoforming will be greatly influenced by predictive analytics. With the help of big data, manufacturers can predict the quality of parts, wear and tear on machines, and energy consumption patterns. These insights will revolutionize the industry: Companies will schedule maintenance procedures in advance to avoid complete outages; they will also be able to use electricity more efficiently – an approach that both saves money and benefits environmental stewardship.
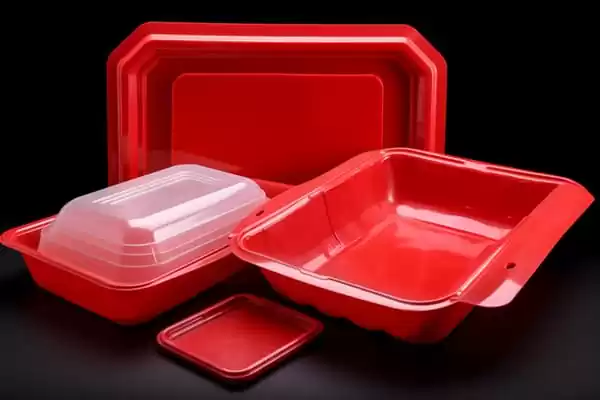
The Role of Automation and AI in Thermoforming
Automation and artificial intelligence are changing every aspect of thermoforming, including quality control, streamlined operations and overall process efficiency. Integration with these technologies also helps optimize how manufacturing operates!
1. How Automation is Changing the Thermoforming Landscape
As automation and artificial intelligence continue to reshape the world of work, there is an increasing need for people who can operate complex equipment or are skilled in using artificial intelligence systems to gather information – these developments are opening up new avenues for job development and original thinking in the thermoforming industry.
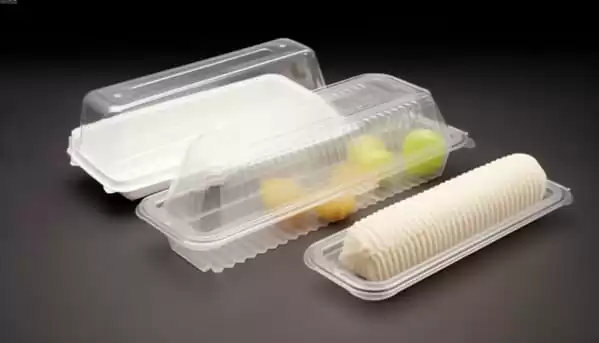
2. Enhanced Quality Control and Machine Uptime
Artificial intelligence (AI) is used to predict equipment failures, thereby reducing repair time and costs. Artificial intelligence also helps with quality control, as machine learning algorithms can identify defects in items moving along the production line; these products can then be separated and recycled or disposed of to reduce waste.
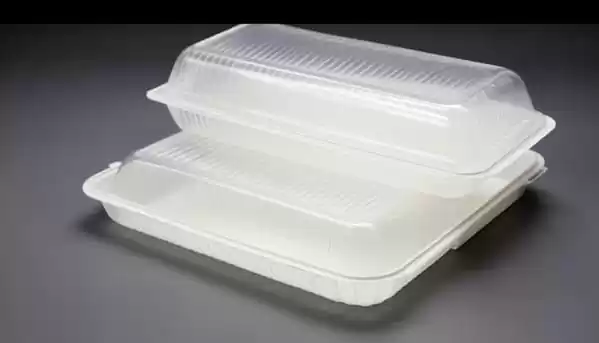
Future Market Trends and Demand
There is great optimism about the future of the thermoforming industry, which should see increased demand as consumer preferences for convenience, value and environmental friendliness continue to grow. However, global economic conditions as well as government environmental policies will also play an important role in shaping the future trajectory of thermoformed plastics market.
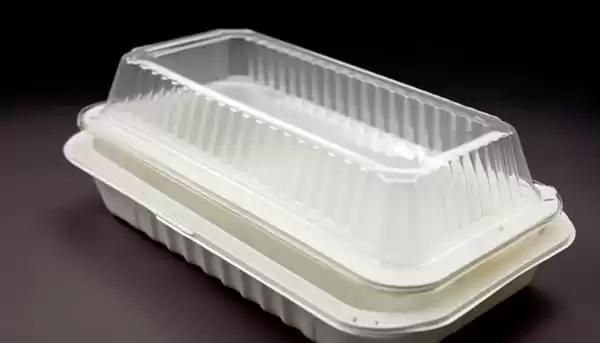
1. Predicted Growth Areas for Thermoforming Applications
The main plastics market drivers of thermoforming growth will be emerging markets and developing economies. Consumer spending in these areas is likely to increase, which will drive demand for many product types. Thermoformed packaging is expected to continue to gain popularity among food and beverage manufacturers, further expanding the market size. Healthcare companies will also increasing demand of these containers, with market growth for precision molded medical devices expanding.
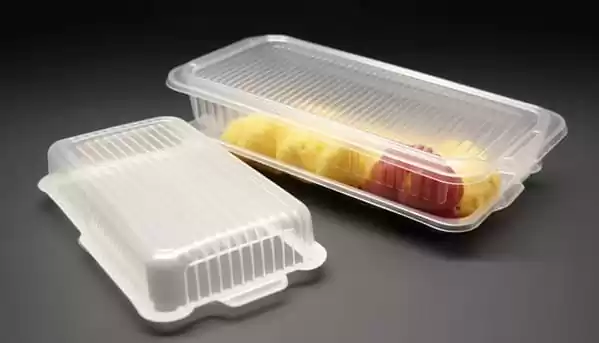
2. Consumer Demands Driving Innovation in Thermoforming
Today everyone expects products to be delivered faster, cheaper and more conveniently. The thermoforming process meets all requirements. As the demand for this technology continues to increase, so does the need to come up with new ideas to keep their products relevant in a rapidly changing market!
Challenges and Opportunities Ahead
The future of thermoforming looks bright, with many opportunities for expansion and new ideas. However, there are many obstacles ahead! If the industry hopes to reach its full potential in the coming years, there are a number of obstacles that need to be addressed.
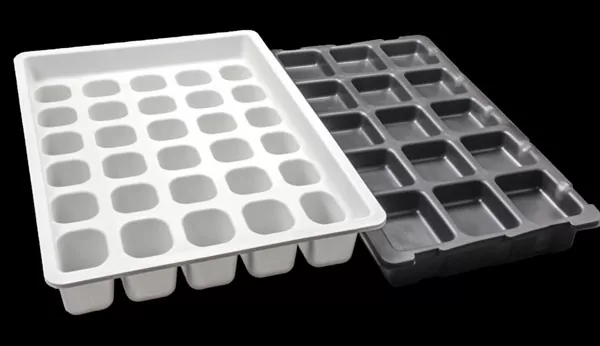
1. The Skills Gap in Thermoforming
The rate at which thermoforming technology is advancing requires the industry to have a more skilled workforce. Therefore, training and education programs must be specifically designed to provide future thermoforming workers with the skills they need to succeed in an ever-changing environment.
2. Encouraging Startups and Innovation
Entrepreneurship and innovation are key factors for any industry to thrive, including thermoforming. If we want to see progress in areas such as sustainability or technology, it’s vital that start-ups feel welcome in our industry!
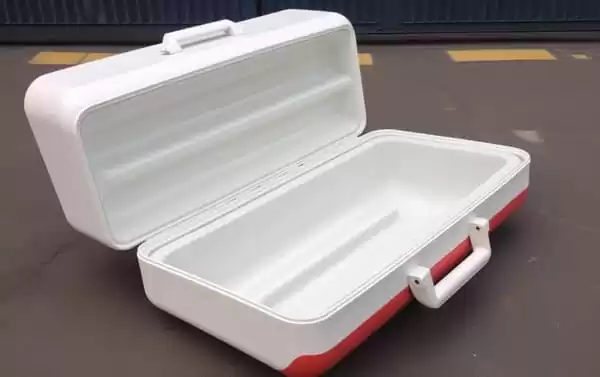
3. Finding the Balance
Innovation in thermoforming must strike a balance between adopting new technologies and materials, maintaining cost effectiveness, and upholding environmental responsibility. The future of thermoforming will be marked by manufacturers who can successfully manage this trinity, delivering value to consumers and sustainability to the planet.
Conclusion
Thermoforming industry leaders are already shaping the future of this manufacturing method. Keep up with trends, be receptive to new thinking, and be open to new concepts; thermoformers can be at the forefront of sustainable production technologies that both satisfy customers and are cost-effective. In conclusion, our investigation into the future of thermoforming shows that there is much more potential for the thermoforming process. Today, all walks of life are demanding sustainability and technology is advancing at a rapid pace; we believe thermoforming is about to enter an exciting period, with unprecedented levels of growth and some truly groundbreaking developments!