If you work in manufacturing, you probably know about thermoforming. This is a popular method where a plastic sheet is heated until it’s soft enough to shape by pressing it against a mould. The type of mould you use will affect how good your thermoforming is – as well as its cost and efficiency. So what kinds of moulds are there for thermoforming? And how do they affect what you can make? In this detailed guide we’ll cover everything from the basics up – including different types of moulds available; why some might be better than others depending on what sort (or volume) production run you have coming up; plus lots more besides!
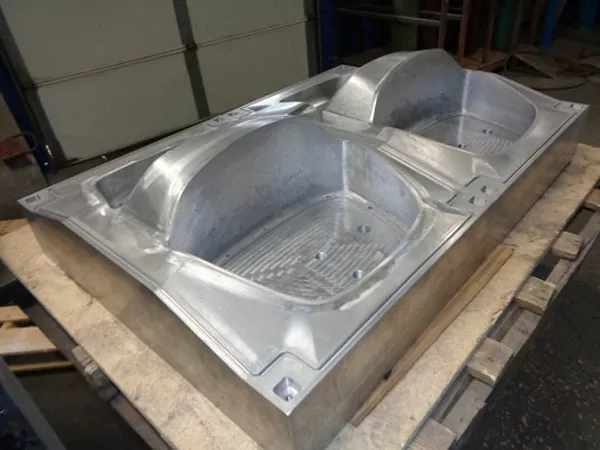
Thermoforming is a very useful, multi-purpose technique for making things. It involves taking heated plastic sheet and using it to create a solid object with desired shape – something that can be seen and felt in three dimensions. To do this requires special tools called molds: without them, the process wouldn’t work. But different jobs need different sorts of molds if they are to succeed; indeed, the kind chosen can often determine whether or not thermoforming will be successful overall. In this blog we shall look at several kinds of these molds – examining their individual characteristics as well as what each type tends to be used for plus any advantages it may have over others available. Whether you’re a seasoned industry professional or just getting started, this detailed breakdown will arm you with the knowledge you need to make informed decisions about mold selection for your vacuum forming projects.
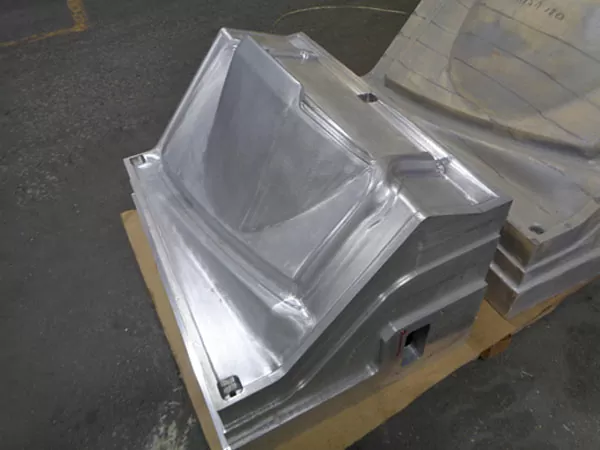
Thermoforming Molds
Prior to delving into the various forms of thermoforming molds available, it is essential to grasp the fundamental principles behind thermoforming itself. Essentially, this process involves heating a plastic sheet until it becomes malleable enough for shaping purposes – at which point an implement known as a “thermoforming mold” comes into play. Depending on exactly what needs they are designed to meet, such molds can assume many different forms.
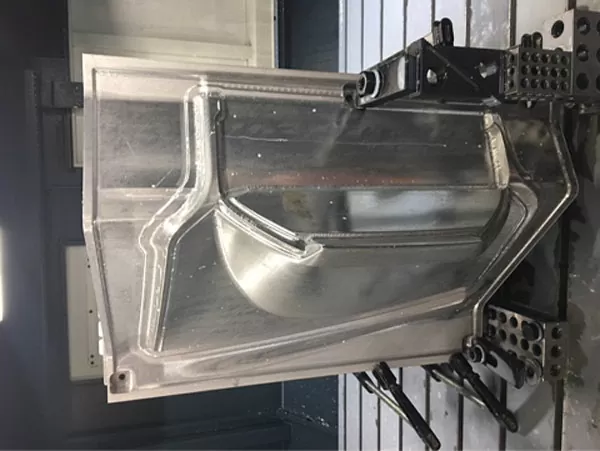
Why Thermoforming Molds Are Important
Thermoforming molds play a crucial role in thermoforming as they determine how intricate and accurate the end result will be. Molds also affect production speed, material efficiency, and overall output quality – meaning the success or failure of a thermoforming job often depends on the type of mold used.
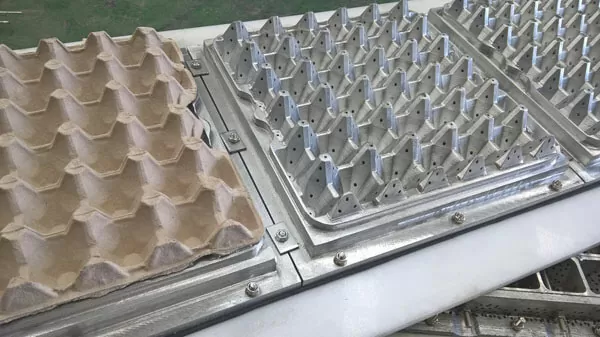
Types of Thermoforming Molds
Thermoforming molds can be categorized based on their complexity, construction, and use case. Here are the common types you’re likely to encounter in thermoforming facilities.
Male and Female Molds
Male and female molds are the basic pressure forming molds. They are employed in simple thermoforming process where either pressure or vacuum draws plastic over a mold.
Male Mold: Shapes the outside of the plastic part.
Female Mold: Shapes the inside of the plastic part by pushing the plastic into a void or cavity.
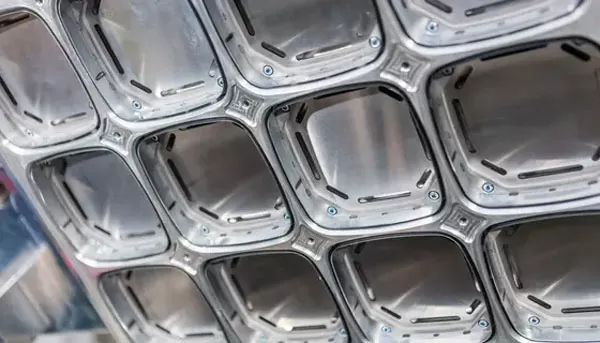
Composite Molds
Composite molds combine different materials to take advantage of their individual strengths. One example is a wooden frame mold with an outer layer made from steel or aluminum. Such molds are affordable ways to handle jobs that do not require extremely high levels accuracy.
Wood Aluminum: A relatively low-cost option for molding with moderate durability and precision.
Steel Aluminum: Offers higher precision and extended longevity due to aluminum’s robustness.

Cast Molds
Cast molds are created when molten metal is poured into a sand mold cavity (or one made from another disposable material). The mold hardens, gets cleaned up, and is then ready for use. People might pick this technique if they’re working with big stuff like car parts which don’t sell as often.
Sand Cast Molds: Cost-effective for one-off or very limited runs.
Plaster Mold Casting: Suitable for intricate molds and provides a smooth finish.
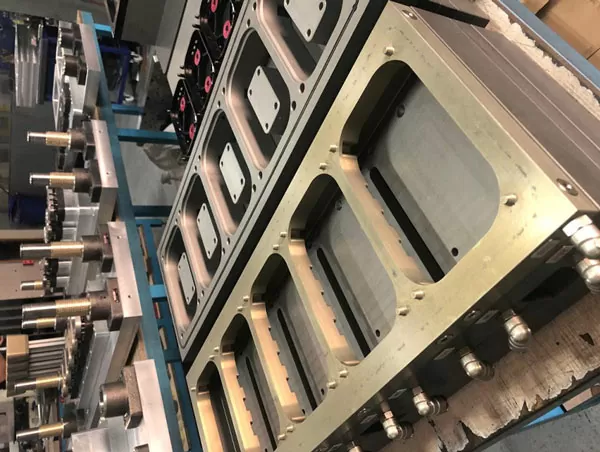
Machined Molds
Machined molds are the result of subtractive manufacturing techniques such as CNC machining. These molds provide a high level of precision and are used for creating parts with exacting tolerances.
CNC Aluminum Molds: Commonly used for low to mid-range production volumes with tight tolerances.
CNC Steel Molds: Reserved for the highest production volumes and superior tolerance requirements.
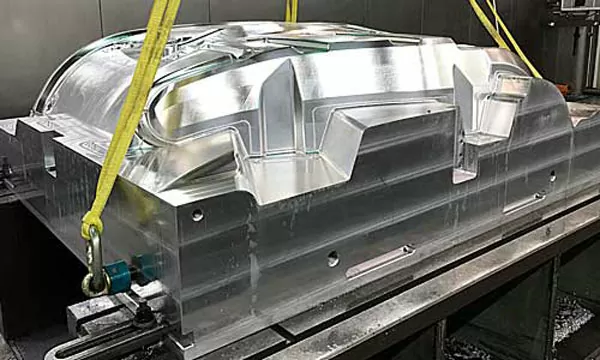
Pressure-Forming Molds
Positive air pressure and vacuum are both used in pressure forming, which enables the production of highly intricate components. The molds employed for this type of molding can be quite advanced and one-of-a-kind.
Plug Assist Molds: Plug assist molds fall under the umbrella of pressure forming; however, they feature an extra component (often powered by either air or mechanical means) that assists in shaping intricate geometries.
Twin sheet molds: Meanwhile also part of pressure forming processes, form hollow items such as enclosures and containers – but do so using two plastic sheets at once while applying force.
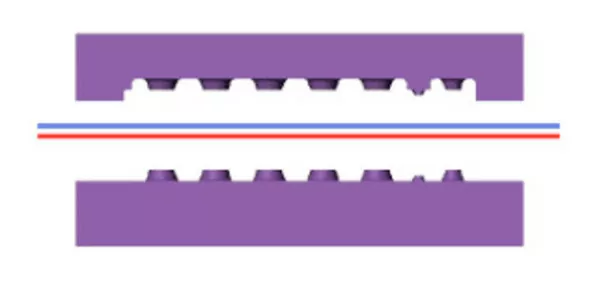
Matched Metal Mold
Metal-to-metal seals, or matched metal dies, are tools used in high-pressure industrial processes. These tools ensure that components are pressed together with great accuracy: this reduces flash, and helps to maintain tight tolerances throughout operations.
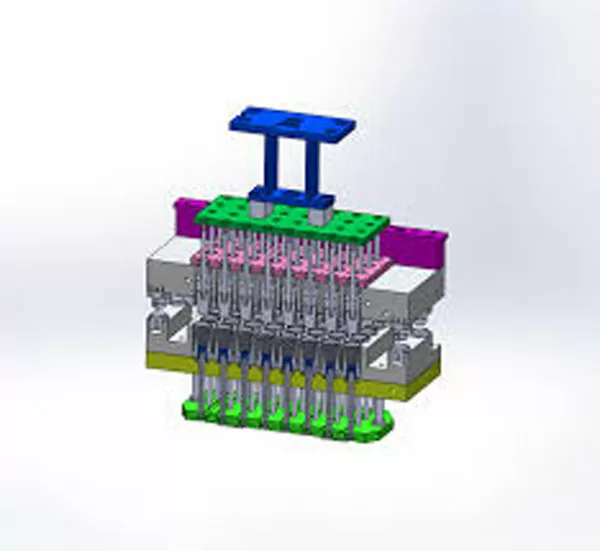
Tilt Molds
It is important to select the right kind of mold for your project in order to achieve optimum results. If you have a product that needs vertical curves or lines, or if it must have an even distribution thickness all over – then tilting molds are perfect!
These types of molds move while they shape things; so when everything’s said and done there won’t be any lumps anywhere on its surface.
Choosing the Right Mold for Your Thermoforming Application
The choice of mold depends on several factors, such as the complexity of the object, the volume of production expected, lead times,vacuum forming machine type, mold surface temperature, heavy or thin gauge thermoforming and the material used. Here’s how you can select a suitable mold for your project:
Part Complexity: For simple objects, basic molds are sufficient and cost-effective. However, if you’re making something more intricate, then you’ll need an advanced mold.
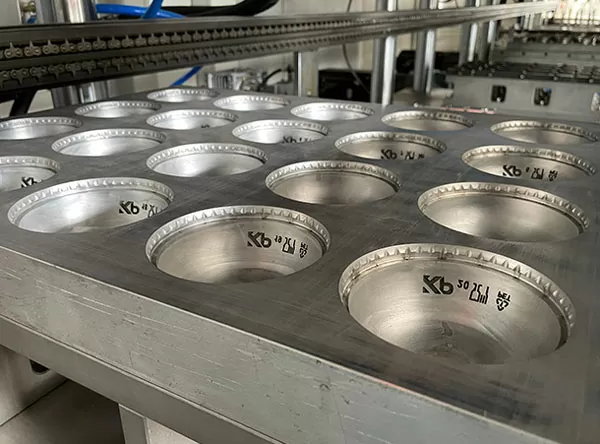
Material Selection: Different plastics flow differently when they’re heated – this means different types of molds will be needed to make sure each piece is high quality.
Production Volume: High-volume projects may warrant the investment in higher-quality, more durable molds.
Lead Times: Sometimes speed is important, machined molds take less time to make than casts ones so if there is a tight deadline on your project knowing this information ahead might help!
Tolerances: When determining which molds to use, take into account how precise your parts need to be. If they must have very tight tolerances, then CNC-machined or steel molds might be the best choice.
Surface Finish: If achieving a certain kind of surface finish is important – for example if these items will be on display and need to look flawless – then consider either pressure forming them using CNC-machined molds again here too.
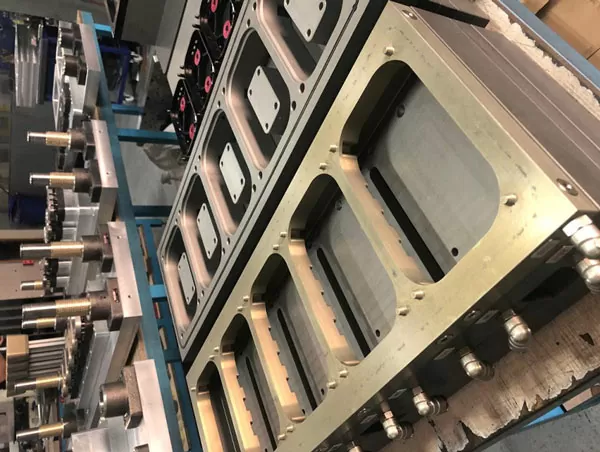
Budget Constraints: Your available budget will play a significant role in mold selection. While high-quality molds can lead to better part quality, they come with higher initial costs.
Real-World Applications of Thermoforming Molds
Now, let’s take a look at how these mold types are actually used. Here are some real-world examples of parts made with different kinds of thermoforming molds:
Transportation Industry: Seats, bus parts and panels for airplane interiors frequently require composite or pressure-forming molds.
Packaging Industry: In packaging, it all depends on what you want the finished package to look like – for example blister packs need precision-machined vacuum forming and pressure forming molds if they’re going fit snugly around each item inside them!
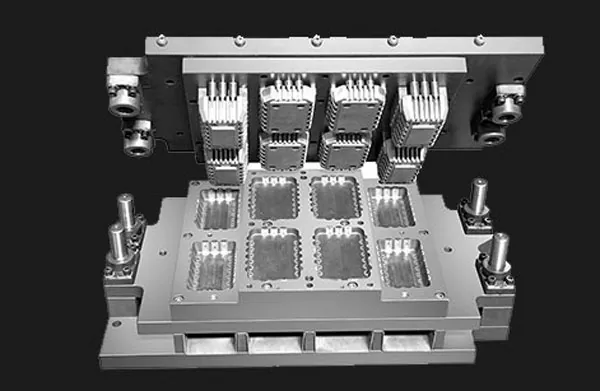
Consumer Goods: Molds come in many shapes sizes complexity levels when manufacturing things like point-of-sale displays cosmetic containers; designers often have specific needs beyond just function too such as wanting their product stand out visually which may mean using more intricate tools at times.
Advantages and Disadvantages of Thermoforming Mold Types
Each mold type comes with its own set of pros and cons that can influence your decision-making process. Here’s a brief rundown:
Male and Female Molds: Simple and cost-effective but limited in complexity.
Composite Molds: Versatile and less expensive than fully machined molds, but have compromises in precision.
Cast Molds: Ideal for low-volume needs but can lack the precision of machined or tooled molds.
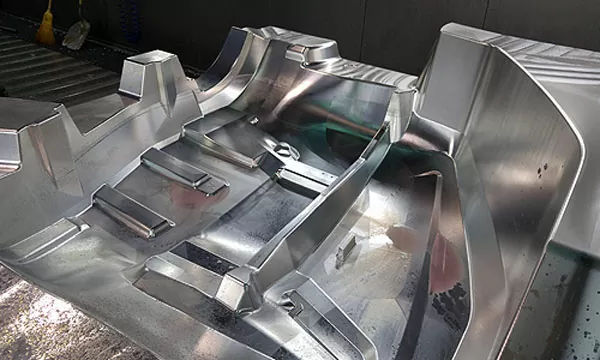
Machined Molds: Offer high precision and durability but can be more costly and time-consuming to produce.
Pressure Forming Molds: High detail resolution and a wider range of materials but can be more expensive than other molds.
Matched Metal Molds: Best for exacting precision and high volumes, but the initial investment can be substantial.
Tilt Molds: Provide intricate part formation for specific applications but can be complex to set up and operate.
Conclusion
In addition to injection molding, thermoforming molds also deserve more praise for their contributions to the manufacturing industry. They play a crucial part in determining the final shape of everyday items that we rely on without thinking too much about it. If you take the time to learn about thermoforming molds – how many kinds there are and what each type does best – you could improve your company’s manufacturing process significantly. To do this, weigh up factors like how many parts you plan on making; how complicated they’ll be to create exactly right (or whether any other method exists which could produce them better); also consider what materials will work perfectly for these purposes before choosing one kind over another.
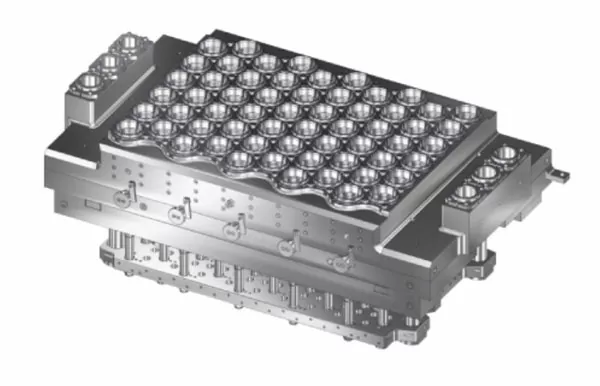
If you want your thermoforming project to succeed – whether it’s a one-off prototype or a full production run – then don’t underestimate the importance of selecting the right mold. The choice you make will affect not only efficiency and costs but also overall quality. So take advice from experts in molds, consider all possibilities carefully before committing yourself financially: because making an informed choice at this stage could save both time and money later on!
When it comes to choosing a vacuum forming molds, there is a lot riding on the decision. It’s not just about knowing your stuff technically, or understanding what you need for this specific project – although both those things are important too! You also have to think long term: where do these pieces fit into future projects as well? By looking at different types of molds available (each with its own pros and cons) plus thinking carefully through how they’ll play out given what’s required–you can make sure everything produced via thermoforming will be top notch quality wise while still being efficient/cost effective. Remember though- don’t think about these molds merely tools; consider them gateways leading towards success/innovation within plastics manufacturing overall.
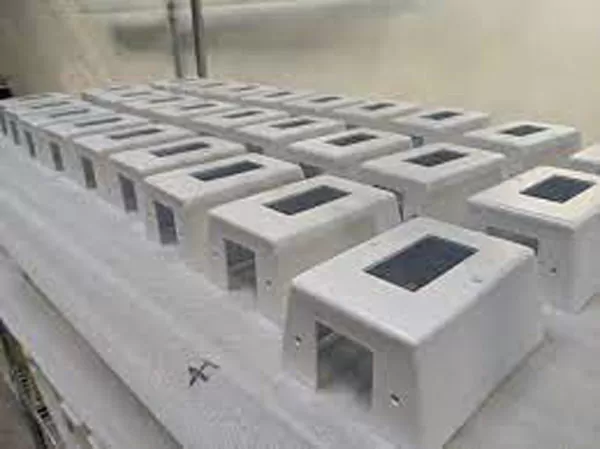
With this in-depth look at thermoforming molds, you will have the knowledge necessary to make careful choices that push your projects further. It doesn’t matter if you are new to vacuum forming process or very experienced; picking the right mold is extremely important. By selecting a mold with an appropriate shape, you can increase both how efficiently things are made and how many new ideas can be tried out – so think hard before deciding because there’s a lot riding on it!