Plastic molding processing is an engineering technology that involves various processes for transforming plastic into plastic products, such as injection molding, thermoforming, rotational molding, compression molding, extrusion, blow molding, etc.
Thermoforming is a crucial process in the plastic manufacturing industry. It uses heat and pressure to shape flat plastic sheets into different products. The mold is central to this operation – so important, in fact, that without it thermoforming wouldn’t work. One key element of the mold is how its cavities are laid out. This has a big effect on aspects such as the design, practicability and how easily items can be made later on down the line.
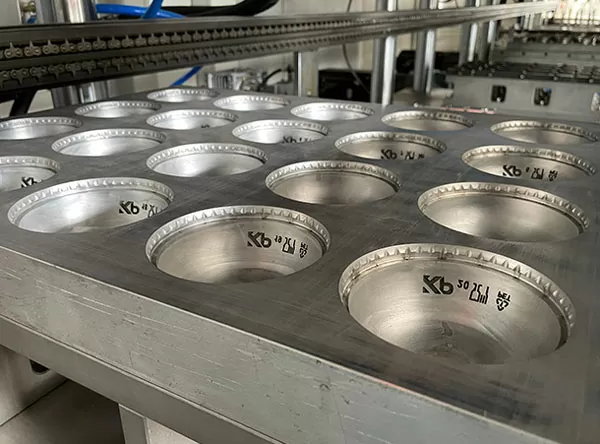
As a manufacturer, you want to make sure your thermoforming machine is efficient and precise – while also allowing for innovation. One way companies achieve this goal? Using different types of mold cavities. In this blog, we’ll examine what those are; how they work within the broader context of a thermoforming process, and how these intricacies play a pivotal role in modern production techniques. As a manufacturer, understanding these configurations will not only enhance your technical knowledge but also optimize your production capabilities for efficiency, precision, and innovation.
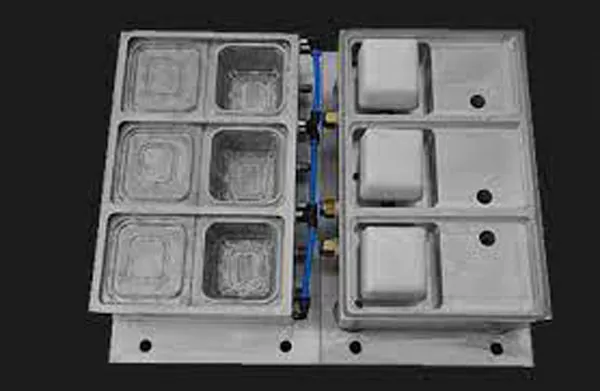
Thermoforming and Mold Cavities
Before we explore the different types of mold cavity designs, it is important to grasp how thermoforming works. Thermoforming is a method for manufacturing plastic products: it involves heating a sheet of thermoplastic material until it becomes malleable; you can then shape this sheet by placing it over a mold and applying pressure or vacuum. The heated sheet is then formed to a particular shape using a mold and is trimmed to create the final product.
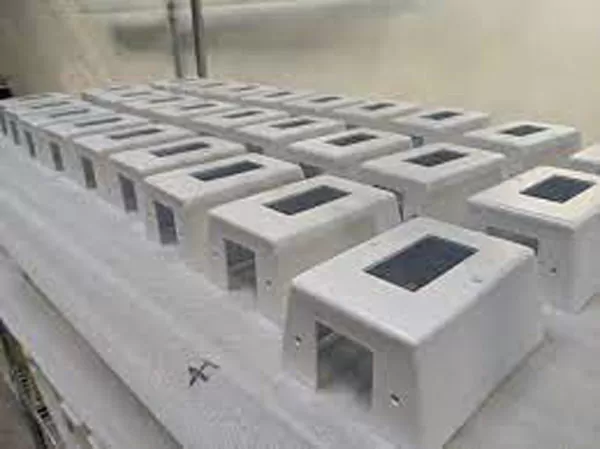
Thermoforming often involves a mold consisting of two parts connected by a hinge. This mold can be opened and closed around a sheet of plastic. Closing the mold forms an empty space, or cavity, inside. Once this has been done and the plastic sheet has been heated up, different types of thermoforming use either vacuum (suction), pressure, mechanical methods – or a combination – to make the required shape by applying force(s) and possibly also cooling (and other things) as necessary.
If you want to make the most of thermoforming machines’ modular design, focus on their mold cavities. These unpretentious parts do more than you’d think: They affect how your molded products turn out. Knowing about different cavity types will help you optimize thermoforming.
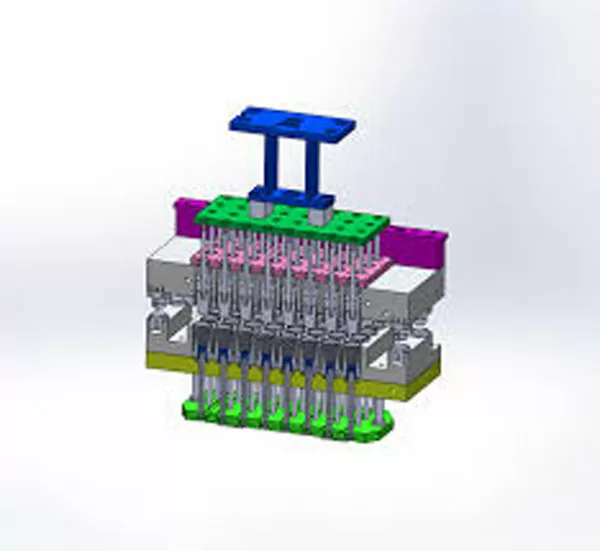
In the world of thermoforming, something magical takes place inside the mold cavity: The film gets heated up and is shaped into a three-dimensional object. And as technology marches forward, how that mold cavity is designed plays an ever-more-important role in the efficiency, accuracy and overall quality of the molded part.
You’ll find an in-depth exploration here on this blog about the various mold cavities for thermoforming machines – crucial when considering types of molds.
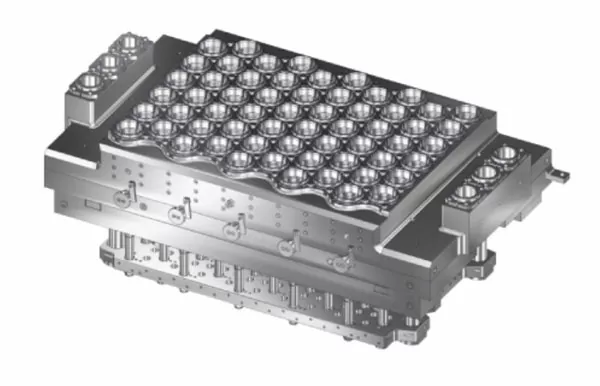
The Basics of Mold Cavities
Before we go any further into talking about the various kinds of mold cavities, let’s go over the basics again. Mold cavities are empty spaces or shapes inside a mold that dictate exactly what the product will look like. These cavities can be very specialized so as to make all sorts of things— everything from plain old consumer packaging to complicated car parts.
In most cases, the mold cavity is comprised of a female mold—used to shape the melted plastic—and a male mold, which aids in shaping it as well. Solid, plug-assisted, pressure-forming and matched metal are all different kinds of cavities one might use depending on their needs.
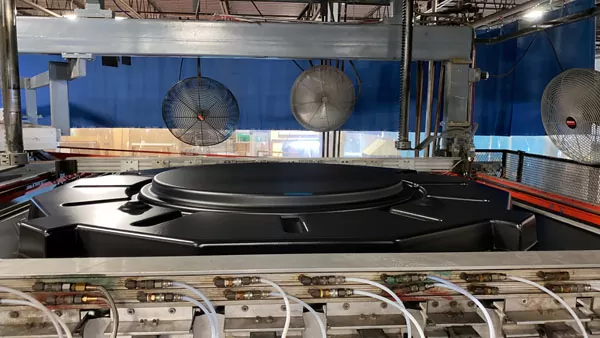
Types of Mold Cavities in Thermoforming
Mold cavities do more than shape material; they also affect a finished product’s detail, geometry and setup. Here are the types of mold cavities commonly found in thermoforming machines.
Single Cavity Mold
The single cavity mold is called so because it is the most basic type out there. Single cavity mold produces only one item each time it runs – which makes it great for making things in small or medium amounts, or very elaborate items. Single-cavity molds can be easier to design and maintain, as they are not as intricate as multi-cavity molds, and they can provide consistency for prototypes or low-demand products.
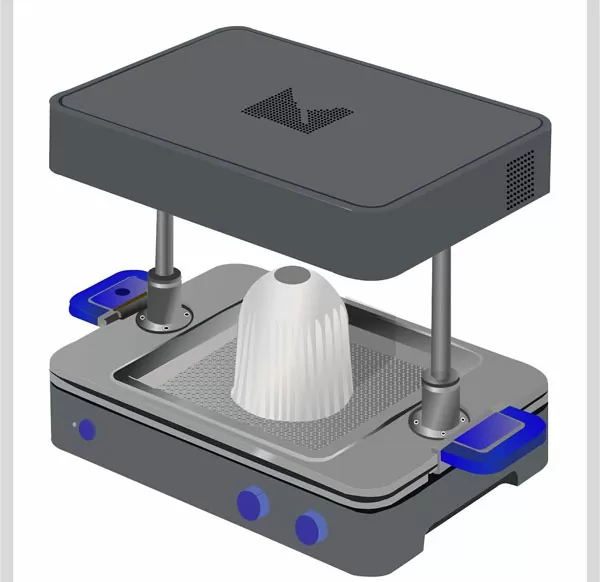
Advantages of a Single Cavity Mold
1. Easy to design and manufacture.
2. Provides high-quality and consistent products.
3. Suitable for intricate or large designs.
Disadvantages of a Single Cavity Mold
1. Inefficient for high-volume production.
2. Longer cycle times for a single product per cycle.
3. Higher production costs for large quantities.
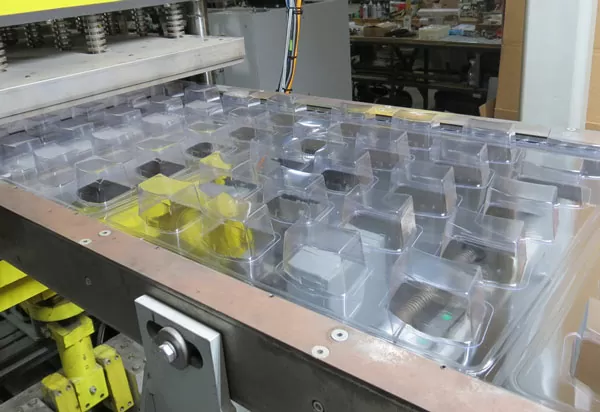
Multi Cavity Mold(Multiple Cavity Molds)
For high-volume production, go for the multi-cavity molds. Multiple cavities can make several parts at once – meaning you get more products per cycle and can charge less for each one. Good news for factories: it doesn’t cost much extra to use these molds because they don’t take any longer than regular ones.
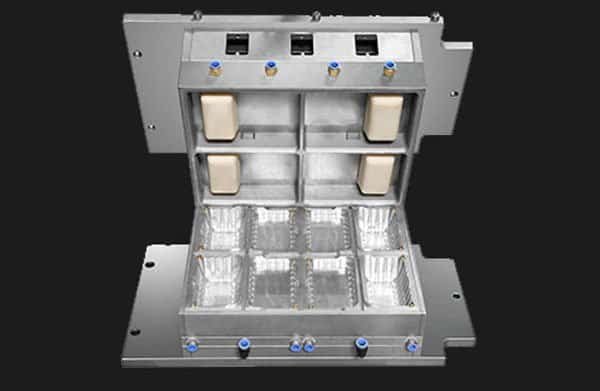
Advantages of a Multi Cavity Mold
1. High production output.
2. Reduced production costs per unit.
3. Efficient for smaller to medium-sized products.
Disadvantages of a Multi Cavity Mold
1. Complex design and manufacturing process.
2. Greater maintenance required due to the intricacy of the mold.
3. Each cavity must produce the same quality, requiring precise alignment and calibration.
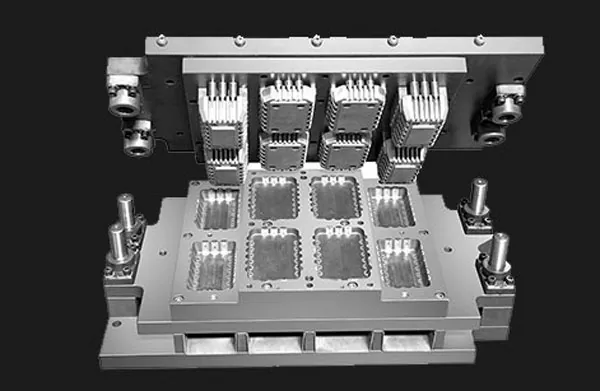
Family Mold
If you need to make two or more parts at once using thermoforming, consider a family mold. This kind of mold is great for products with lids and bases—or any primary part joined by one or more secondary elements. Think packaging, lots of types of containers and all sorts of plastic enclosures: many will have this type of layout.
Advantages of a Family Mold
1. Saves time by producing multiple parts in one cycle.
2. Ideal for linked or multi-element products.
3. Reduces energy consumption owing to fewer cycles needed.
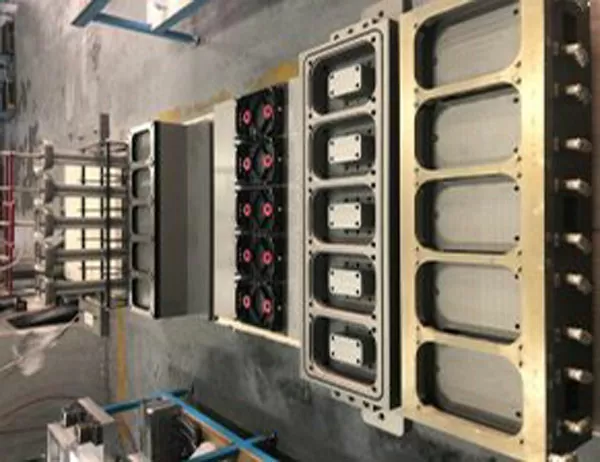
Disadvantages of a Family Mold
1. Complexity in design and setup.
2. Less efficient for high-volume production when compared to a multi-cavity mold.
3. Higher maintenance and calibration needs for accurate parting lines.
Stripper Plate Mold
When the parting of the mold would be difficult or damaging to the formed product, one uses a stripper plate mold setup. A plate or plate system pushes the formed part out of the mold after cooling, allowing for a more complex cavity design without the concern of damaging the part.
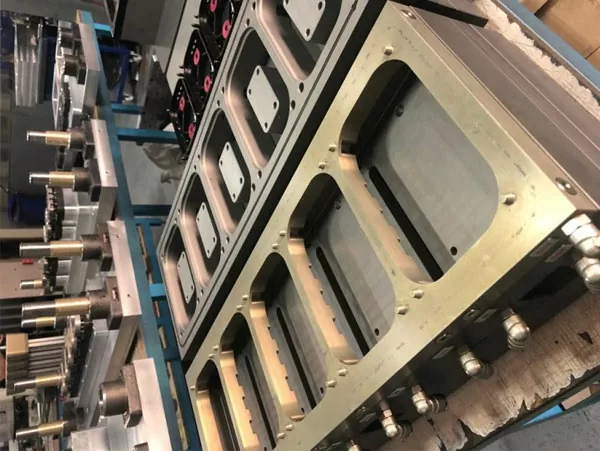
Advantages of a Stripper Plate Mold
1. Allows for complex part geometries.
2. Reduces post-processing activities by automatically stripping the part from the mold.
3. Protects part integrity by avoiding contact with mold surfaces.
Disadvantages of a Stripper Plate Mold
1. Adds a step to the thermoforming process, potentially increasing cycle time.
2. Adds complexity to the mold and tooling.
3. Requires additional maintenance due to moving parts.
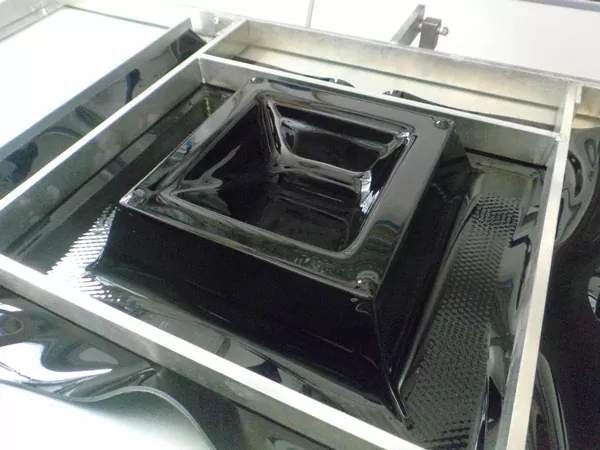
Stack Molds
Stack molds bring multi-cavity molding to the next level. In a standard thermoforming cycle, several sets of molds are stacked vertically by the machine. This enables the creation of intricate parts that would normally necessitate multiple steps within one cycle – thereby making the process even more efficient. Stack molds find use in areas such as healthcare, where part weight is important.
Collapsible-Core Molds
In industries such as consumer electronics and pharmaceuticals, it is common to find complex part shapes that include internal threads or undercuts. Collapsible-core molds make it possible to create these parts using a single mold cavity with no unscrewing needed. These molds have a core made up of sections which can be made to collapse inwards – this action allows the finished part to be taken out easily when the mold opens. If you use an collapsing core mold, you won’t need any additional side-actions (unscrewing or similar) to get parts with complex geometries out of the mold cavity!
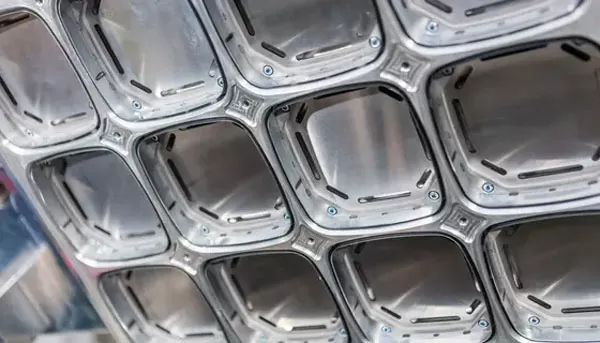
Shuttle Molds
Shuttle molds, also called rotary or indexing molds, employ a platen that rotates to transport molds into and out of the molding area. With this desige, the machine can have multiple molds in the processing area simultaneously – a boon for manufacturing intricate components or producing different parts at once. Containers and lids are among the many items made using this type of mold.
Multiple-Parting Surface Molds
The male and female molds in multi parting surface molds separate into multiple sections to free the part. This type of mold is good for parts with odd shapes that could get stuck or folded if you just pulled them out of a regular mold. Multiparting surface molds are difficult to design, tricky to operate exactly right, but necessary for some products that can’t be removed from a mold in any other way.
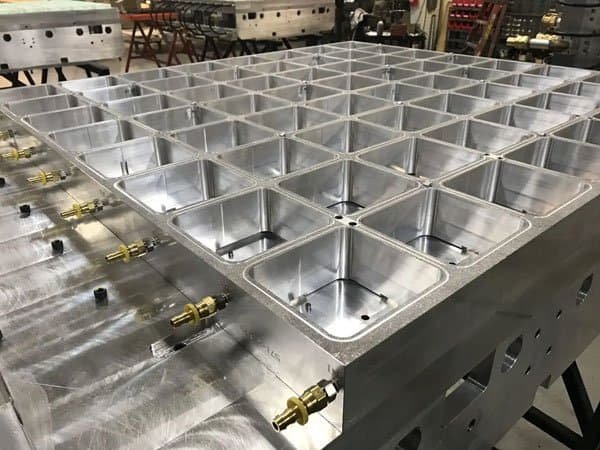
How to Choose?
Choosing the right mold for your thermoforming application is a critical decision that will impact not only your initial investment but also your long-term production capabilities and profitability. When determining the mold type that best suits your needs, consider the following factors:
1. Product size and complexity.
2. Desired production volume.
3. Material type and thickness.
4. Cycle time requirements.
5. Quality and finish standards.
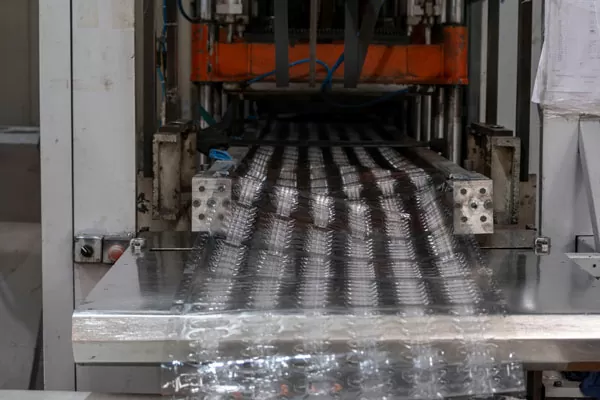
There are advantages and limitations to each type of mold cavity. For instance, a single-cavity mold might have shorter cycle times and be simpler to take care of, but a multi-cavity mold is designed for making lots of products at once – so each one costs less.
Part Complexity
Whether you need a single-cavity or multi-cavity mold, or one with special features like collapsible cores or stack molds, will depend largely on how intricate your part design is. Simpler parts usually don’t require any special considerations, but if you’re working with a complex geometry, you can choose collapsible cores or stack molds.
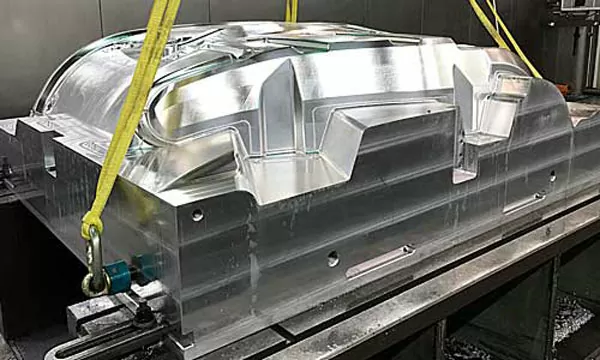
Material and Thickness
The thickness and material type being thermoformed determine the choice of mold cavity. If you’re working with heavy-gauge materials, stack molds might be best, while thin-gauge ones may call for collapsible-core molds’ greater complexity.
Volume and Turnaround Time
If you’re operating in a high-volume, time-sensitive environment, multi-cavity or stack molds are likely to be the best choices for rapid and efficient production.
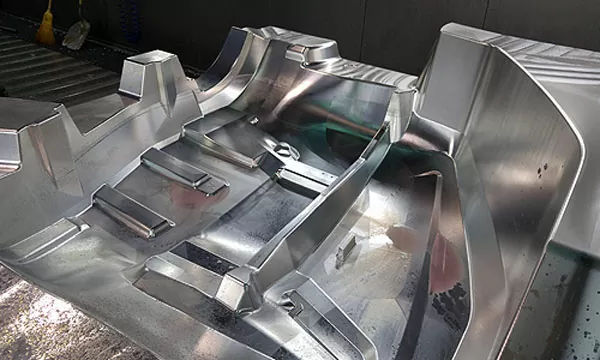
Budget and Tooling
There are different types of mold cavity, each with its own cost and tooling needs. Single and multi-cavity molds often work out cheaper overall; stack and collapsible-core molds are pricier because they’re trickier to make.
Innovations in Mold Cavity Technology
The thermoforming industry is no stranger to innovation, and mold cavity technology is no exception. Recent advancements have led to improvements in precision, material distribution, and cycle times, among other areas. Some of the latest developments include:
Manufacturers are constantly pushing the limits of thermoforming thanks to developments in material sheet, mold material, machining, and design technology. It’s now common to find things like overmolding, customized textures or complex details –– even when producing at high volumes.
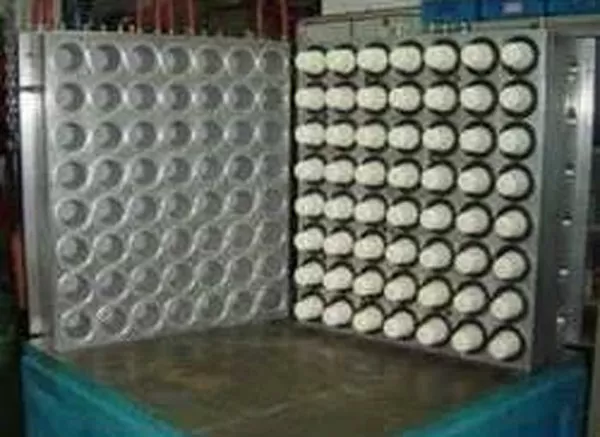
1. In-Mold Sensing and Feedback
Smart sensors in mold cavities enable instant checks on the quality of components as they are made, how well the material is being mixed and whether the molding process itself is working properly. This means any necessary tweaks can be made straight away – leading to better control overall.
2. Servo-Driven Systems
Servo-driven mold cavity systems provide superior control during formation, leading to improved part quality and less material wastage. Furthermore, they use energy more efficiently, meaning there can be power savings too.
Thanks to the introduction of servo-driven motion, real-time monitoring and 3D printing for rapid prototyping, thermoforming mold design have become increasingly exact, adaptable and efficient. This means it is now possible to create products with more imaginative and dynamic designs – all while using cost-effective production methods.
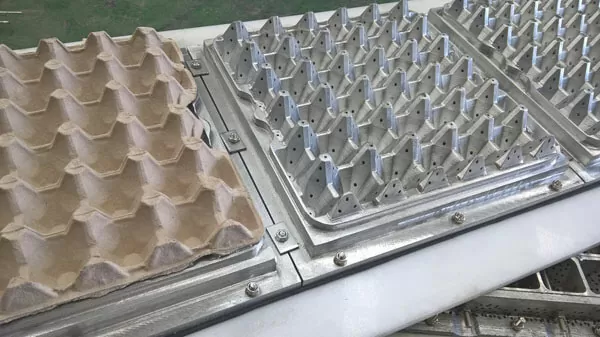
3. 3D-Printed Molds
By using a 3D printer to make molds, the process of creating prototypes is being completely changed – it’s become affordable to try out designs before investing in permanent equipment.
By staying informed about the latest advancements in mold cavity technology and incorporating these into your manufacturing processes, you can ensure that your thermoforming operation remains at the forefront of the industry, offering innovative solutions that meet the ever-changing demands of the market.
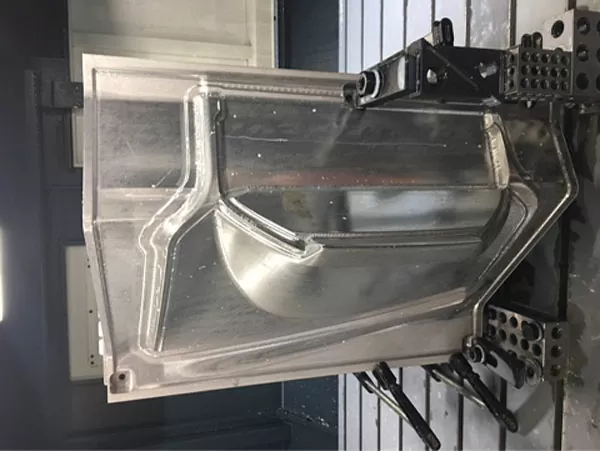
Conclusion
Plastic molding is a popular technology that encompasses various techniques like thermoforming, injection molding, and multi cavity injection molding. But within this broad field, it’s important to grasp how complex thermoforming and injection molding process can be. These processes involve things like runner system (which channel material into molds), thermoforming molds themselves and injection molds too. Equally crucial is understanding how to choose a right thermoforming machine or injection molding machine – plus choosing the right ones for your job; how you use them affects both productivity and output quality.
Understanding the various mold cavity options is essential for thermoforming success. These cavities do more than shape plastic—they also impact efficiency, volume output and part quality. By knowing your choices and picking smartly, you can make your thermoforming operation nimble, effective and even cutting-edge.
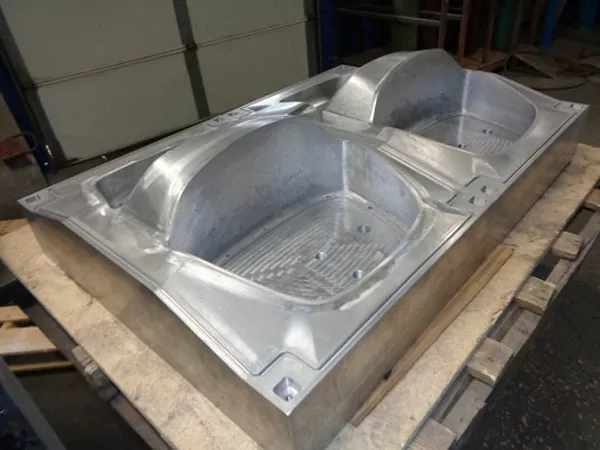
Manufacturers have lots of choices when it comes to making good parts inexpensively using thermoforming – all because of the mold cavity. They can pick from many types: single or multi-cavity molds, stack molds, collapsible-core molds and shuttle molds. By understanding these options plus parting-surface molds, as well as how each type differs from one another, companies can select wisely and get more out of their production process.
Whether you’re making prototypes, small batches of custom parts or large quantities for a mass market – then the choice of mould cavity is key. With good thought about what you need for production and by making the most of up-to-date mould design technology, you can make sure that whatever you produce is high quality and offers customers value for money.
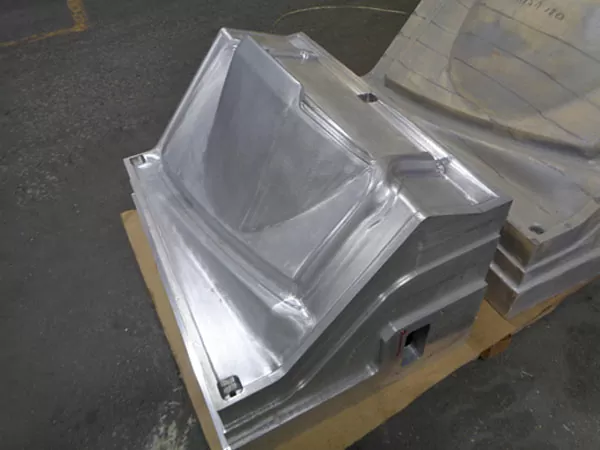
As technology progresses, so too does the potential for creative mold cavity design. Bear these thoughts in mind as you delve into thermoforming – and don’t be afraid to seek advice from seasoned pros: They can help make sure your choice of mold cavity matches both your manufacturing objectives and what your products require. The correct cavity can take your thermoforming endeavors up a gear, enabling you to produce goods with increased efficiency and style.