Sheet Bubbling
1. Heating too fast. The following methods can be used to exclude:
- Reduce the heater temperature appropriately.
- Slow down the heating speed appropriately.
- Increase the distance between the sheet and the heater appropriately to make the heater farther away from the sheet.
2. Uneven heating. The following methods can be used to exclude:
- Use baffles, air distribution hoods or screens to adjust the distribution of hot air so that all parts of the sheet are heated evenly.
- Check whether the heater and shielding net are damaged, and repair the damaged parts.
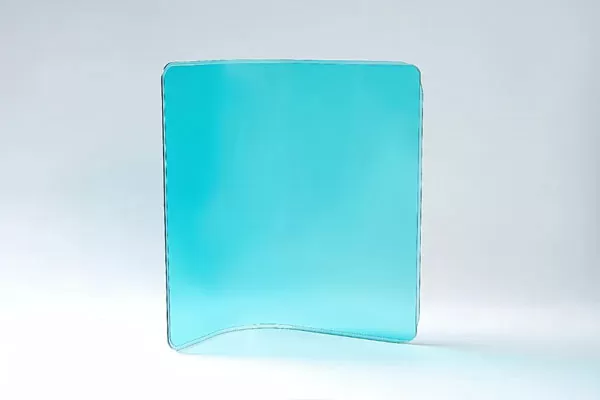
3. The sheet is damp. The following methods can be used to exclude:
- Carry out pre-drying treatment. For example, polycarbonate sheets with a thickness of 0.5mm should be dried at 125-130°C for 1-2 hours, and sheets with a thickness of 3mm should be dried for 6-7 hours. ARS sheets with a thickness of 3mm should be dried at 80-90°C for 1-2h and should be thermoformed immediately after drying.
- Carry out preheating treatment.
- Change the heating method to double-sided heating. Especially when the thickness of the sheet is more than 2mm, heating on both sides must be adopted.
- Do not open the moisture-proof packaging of the sheet prematurely. Should be unpacked and formed immediately before thermoforming.
4. There are bubbles in the sheet. The production process conditions of the sheet should be adjusted to eliminate bubbles.
5. Inappropriate sheet type or formula. Appropriate sheet materials should be selected and the formula should be adjusted reasonably.
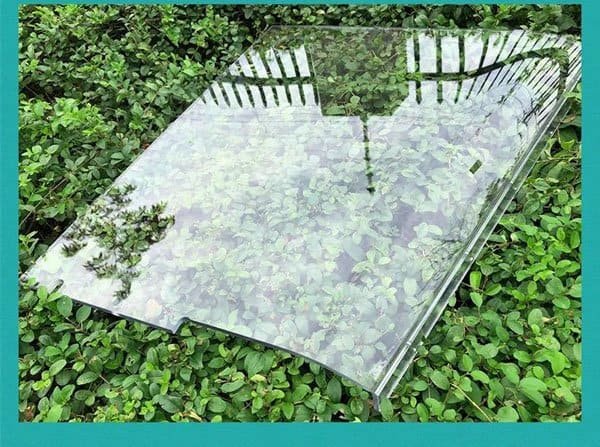
Sheet Tear
1. The mold design is poor and the arc radius at the corner is too small. The radius of the transition arc should be increased.
2. The heating temperature of the sheet is too high or too low. When the temperature is too high, the heating time should be appropriately reduced, the heating temperature should be lowered, the heating should be even and slow, and compressed air should be used to slightly cool the sheet; when the temperature is too low, the heating time should be appropriately extended, the heating temperature should be increased, and the heating should be evenly heated.
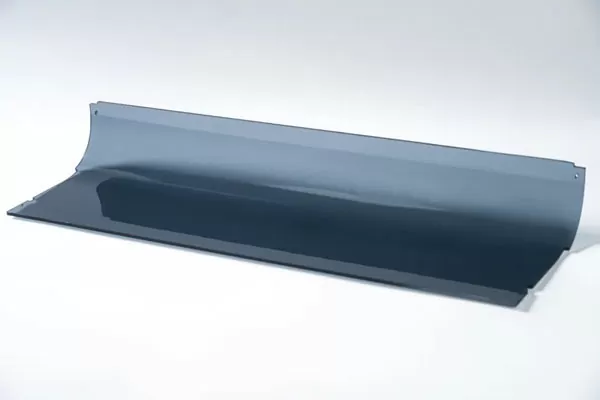
Sheet is Burnt
1. The heating temperature is too high. The heating time should be appropriately shortened, the temperature of the heater should be lowered, the distance between the heater and the sheet should be increased, or a shield should be used to isolate the sheet so that the sheet is heated slowly.
2. Improper heating method. When forming thicker sheets, if single-sided heating is used, the temperature difference between the two sides will be large. When the back side reaches the molding temperature, the front side will be overheated and burned. Therefore, for sheets with a thickness greater than 2mm, heating on both sides must be adopted.
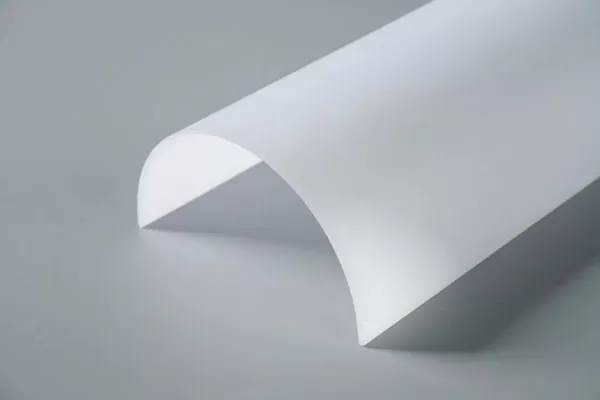
Sheet Collapse
1. The sheet is too hot. The following methods can be used to exclude:
- Appropriately shorten the heating time
- Lower the heating temperature appropriately
2. The melt flow rate of the raw material is too high. When making films, raw materials with lower melt flow rates should be used as much as possible or the drawing ratio of the sheet should be appropriately increased. The thermoforming area is too large. Screens and other shields should be used to ensure uniform heating, and the sheet can also be heated differently to prevent overheating and collapse in the middle area.
3. Uneven heating or inconsistent raw materials used lead to different collapse of each sheet. The following methods can be used to exclude:
- Install air distribution boards at various parts of the heater to distribute hot air evenly.
- The amount and quality of recycled materials in sheets should be controlled.
- Mixing of different raw materials should be avoided.
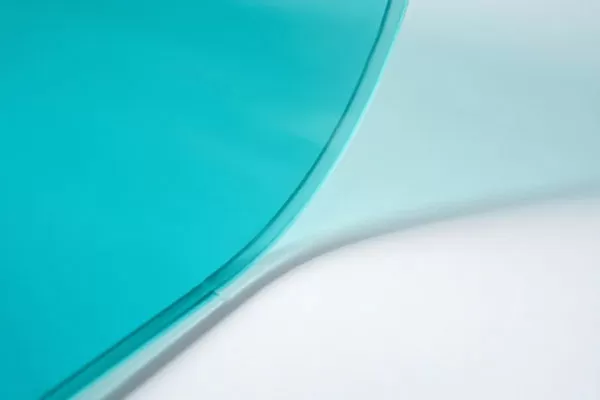
Bright Stripes on Surface
The heating temperature of the sheet is too high. The heating temperature should be appropriately lowered and the heating time should be shortened. You can also move the heater away from the sheet and heat slowly. If the sheet is partially overheated, a shielding net can be used to cover the overheated area.
There are Cold Material Marks and Streaks on the Surface
1. The temperature of the pressure-assist plunger is too low. should be increased appropriately. You can also use a wooden pressure-assisted plunger or wrap the plunger with cotton velvet cloth and blankets for heat preservation. The mold temperature is too low. It should be increased appropriately, but should not exceed the curing temperature of the sheet.
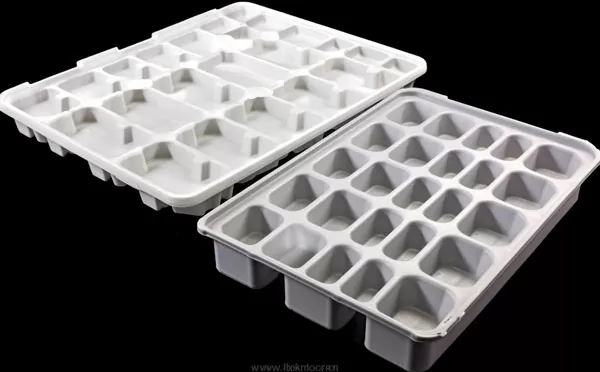
2. Mold cooling is uneven. Cooling water pipes or sinks should be added and the water pipes should be checked for blockage. The heating temperature of the sheet is too high. It should be appropriately lowered, and air can be used to blow the surface of the sheet slightly cooler before forming. Improper selection of forming process. Other forming processes should be used instead.
There are Marks and Stains on the Surface
1. The surface finish of the mold cavity is too high, and air is trapped on the smooth mold surface, causing acne spots on the surface of the product. The cavity surface should be sandblasted and additional vacuum holes can be added.
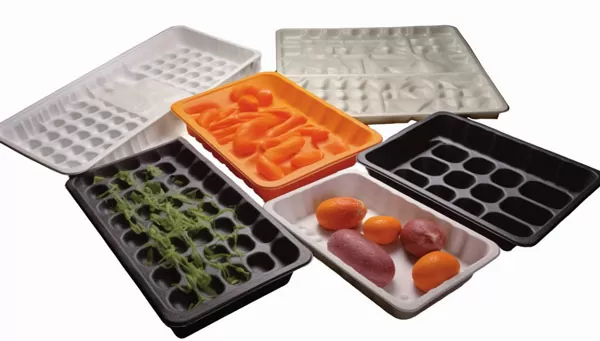
2. Poor evacuation. Exhaust holes should be added. If acne spots only occur in a certain area, you should check whether the air extraction hole there is blocked or add an air extraction hole in that area. When using sheets containing plasticizers, the plasticizers accumulate on the mold surface to form spots. You can use the following methods to exclude:
- Use a temperature-controllable mold and adjust the mold temperature appropriately.
- When heating the sheet, keep the mold as far away from the sheet as possible.
- Appropriately shorten the heating time.
- Clean the mold promptly.
3. The mold temperature is too high or too low. should be adjusted appropriately. If the mold temperature is too high, cooling should be strengthened and the mold temperature should be lowered; if the mold temperature is too low, the mold temperature should be increased and the mold should be insulated.
4. Improper selection of mold material. When processing transparent sheets, do not use phenolic resin to make molds. Aluminum molds should be used. The mold surface is too rough. The cavity surface should be polished to improve surface finish. If the surface of the sheet or mold cavity is not clean, the dirt on the surface of the sheet or mold cavity should be completely removed.
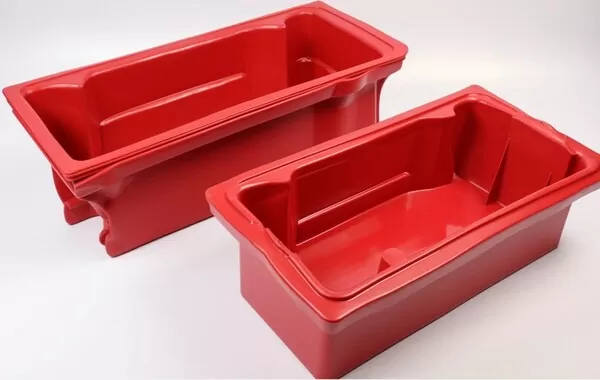
5. There are scratch marks on the surface of the sheet. The surface of the sheet should be polished and the sheet should be stored with paper. The dust content of the air in the production environment is too high. The production environment should be purified. The draft of the mold is too small. should be appropriately increased
Surface Yellowing or Discoloration
1. The heating temperature of the sheet is too low. The heating time should be appropriately extended and the heating temperature should be increased. The heating temperature of the sheet is too high. The heating time should be appropriately shortened and the heating temperature should be lowered. If the sheet is locally overheated, check whether the relevant heater is out of control.
2. The mold temperature is too low. Preheating and insulation should be carried out and the mold temperature should be appropriately increased. The temperature of the pressure-assist plunger is too low. It should be heated appropriately. The sheet is overstretched. Thicker sheets should be used or sheets with better ductility and higher tensile strength should be used. This failure can also be overcome by modifying the mold.
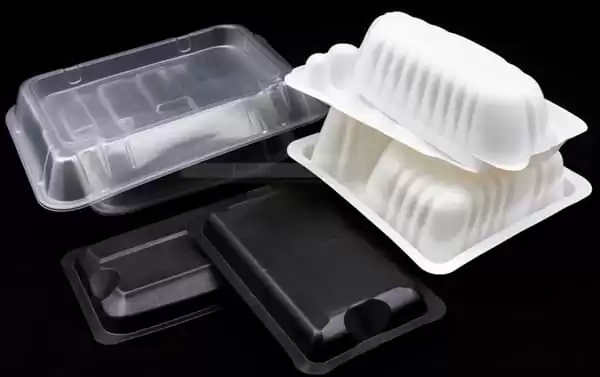
3. The sheet cools prematurely before it is fully formed. The molding speed and evacuation speed of the sheet should be appropriately increased, the mold should be properly insulated, and the plunger should be properly heated. Improper mold structure design. You can use the following methods to exclude:
- Reasonably design the draft angle. Generally, when forming a female mold, it is not necessary to design a draft slope, but designing some slope is beneficial to the uniform wall thickness of the product. When forming the positive mold, for styrene and rigid polyvinyl chloride sheets, the draft angle is preferably about 1:20. For polyacrylate and polyolefin sheets, the draft angle is preferably greater than 1 :20.
- Increase the fillet radius appropriately. When the edges and corners of the product need to be rigid, the arcs can be replaced by bevels, and then the bevels can be connected with small arcs.
- Appropriately reduce the stretching depth. Generally, the drawing depth of the product should be considered in conjunction with its width. When vacuum molding is used directly, the drawing depth is preferably less than or equal to half of the width. When deep drawing is required, a pressure-assisted plunger or air pressure forming method should be used. Even with these forming station, the draw depth should still be limited to less than or equal to the width.
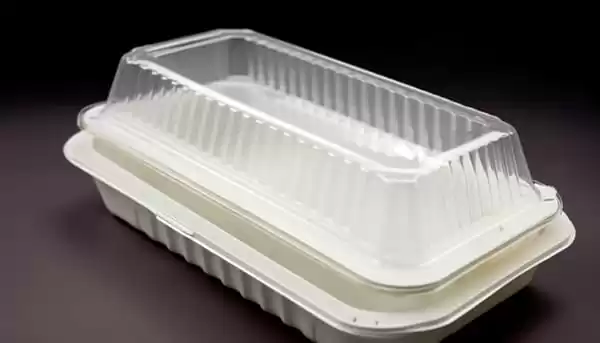
4. Too much recycled material is used. Its dosage and quality should be controlled. The raw material formula does not meet the requirements of thermoforming process. The formula design should be appropriately adjusted when making sheets
Sheet Arching and Wrinkles
1. The sheet is too hot. The heating time should be appropriately shortened and the heating temperature should be lowered. The melt strength of the sheet is too low. Resins with lower melt flow rates should be used as much as possible; the draw ratio of the sheet should be appropriately increased during filmmaking; and when thermoforming, a lower molding temperature should be used as much as possible.
2. Improper control of the stretch ratio during production. should be adjusted appropriately. The extrusion direction of the sheet is parallel to the die spacing. The sheet should be turned 90 degrees. Otherwise, when the sheet is stretched along the extrusion direction, it will cause molecular orientation, which cannot be completely removed even by molding and heating, resulting in wrinkles and deformation of the sheet.
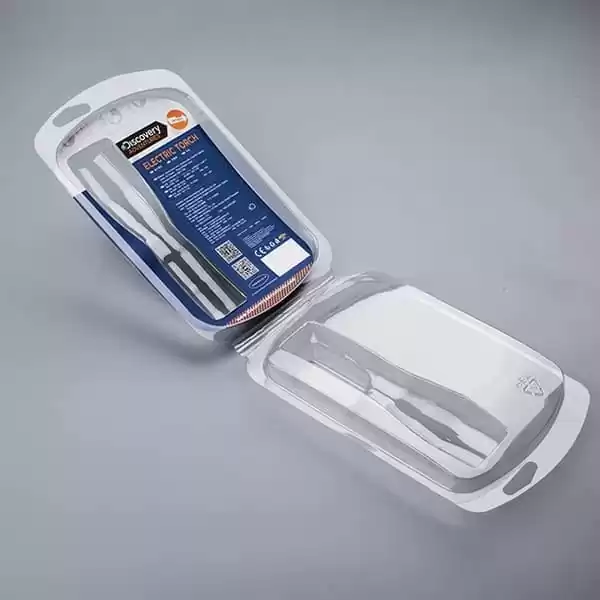
3. The part of the piece of material that the plunger hits first is overextended or the mold design is improper. You can use the following methods to exclude:
- Formed using female mold.
- Add a pressure-assisting device such as a plunger to flatten the wrinkles.
- Increase the demoulding taper and fillet radius of the product as much as possible.
- Appropriately speed up the movement speed of the pressure-assisted plunger or mold.
- Reasonable design of frame and pressure-assisted plunger.
Warpage
1. Uneven cooling. The cooling water pipe of the mold should be added and checked to see if the cooling water pipe is blocked. The wall thickness is unevenly distributed. The pre-stretching and pressure-assisting device should be improved and a pressure-assisted plunger should be used. The sheets used for molding should be of consistent thickness and evenly heated. Where possible, the structural design of the product should be appropriately modified, and reinforcements should be provided on large planes.
2. The mold temperature is too low. The mold temperature should be appropriately raised to slightly lower than the curing temperature of the sheet, but the mold temperature should not be too high, otherwise the shrinkage rate will be too high. Demold too early. The cooling time should be appropriately increased, and air cooling can be used to speed up the cooling of the product. The product must be cooled below the solidification temperature of the sheet before it can be demoulded.
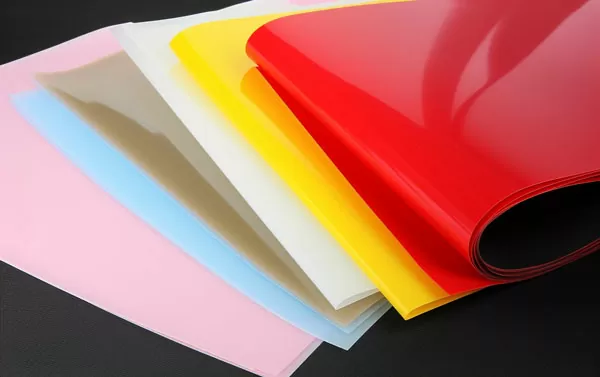
3. The sheet temperature is too low. The heating time should be appropriately extended, the heating temperature should be increased, and the evacuation speed should be accelerated. Poor mold design. The design should be modified. For example, when vacuum forming, the number of vacuum holes should be appropriately increased, and the grooves of the mold on the trimming line should be increased appropriately.
The Sheet is Pre-Stretched Unevenly
The thickness of the sheet is uneven. The production process conditions should be adjusted to control the thickness uniformity of the sheet. When thermoforming, heat should be slow. The sheet is heated unevenly. The heater and shielding screen should be inspected for damage. The production site has large airflow. The operating area should be shielded. Compressed air is unevenly distributed. An air distributor should be installed at the air inlet of the pre-stretch box to ensure even air blowing.
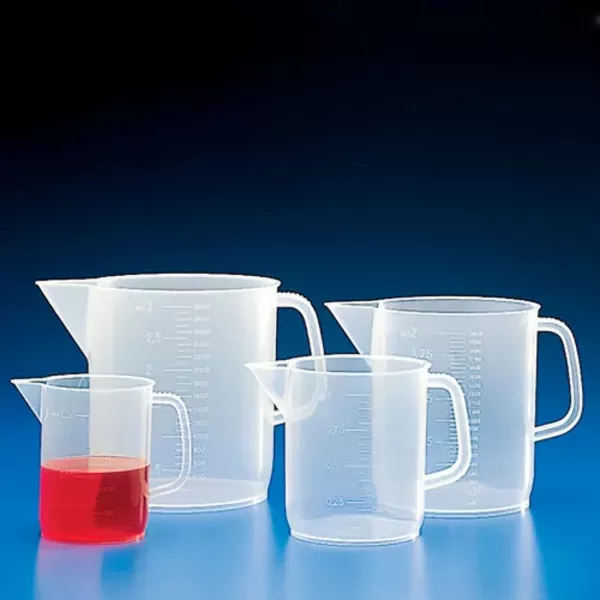
Poor Wall Distribution
Improper selection of forming process. The pressure-assisted technology of the air expansion plug can be used instead. The sheet is too thin. Thicker sheets should be used instead. The sheet is heated unevenly. The heating system should be checked and the temperature should be lower for the parts where the corners of the product will be formed. Before pressing, you can draw some cross lines on the sheet to observe the material flow during forming and adjust the heating temperature. The mold temperature is uneven. It should be adjusted appropriately to be even. Improper selection of film raw materials. Raw materials should be replaced.
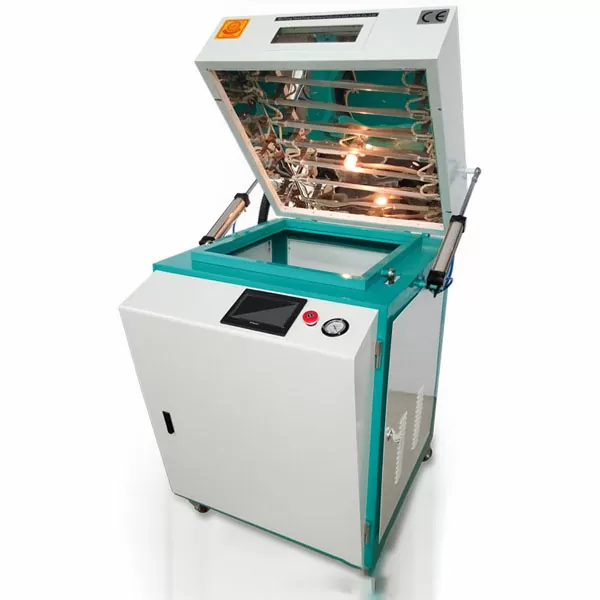
Conclusion
In the thermoforming process of plastic sheets, various factors contribute to common failures that affect the overall efficiency and quality of the production. One crucial element is the roll stand, which plays a pivotal role in the material feeding mechanism. The efficiency of the entire system is further influenced by the clamp rail heaters, ensuring proper heating and forming of the plastic sheets. However, challenges such as vacuum leaks can compromise the integrity of the forming process, leading to poor part detail. In line thermoforming, characterized by its continuous production, requires meticulous attention to details, especially in addressing issues related to ring assist and the trim station. The roll-fed mechanism, a widely used method, can encounter challenges on the mold side, impacting the overall output. To mitigate these common failures, manufacturers need to implement effective countermeasures that address each stage of the thermoforming process, ensuring a seamless and reliable production workflow.