With the rapid development of modern electronic technology, fully automatic thermoforming machines have become a driving force for the development of mechanical processing and other industries. As a type of laminating machine series, fully automatic thermoforming machines are widely used in our lives.
The forming principle of the thermoforming machine is to fix the plate workpiece and the material film on the equipment platform, heat it with a chromium-nickel wire heating tube system to soften the material film, and then use the low pressure of the equipment to remove the air between the plate and the material film, so that The material film can be adsorbed and formed according to the contour of the workpiece. After cooling out of the warehouse, the worker directly cuts out the workpiece. Commonly used materials processed by thermoforming machines include PVC, PET, etc.
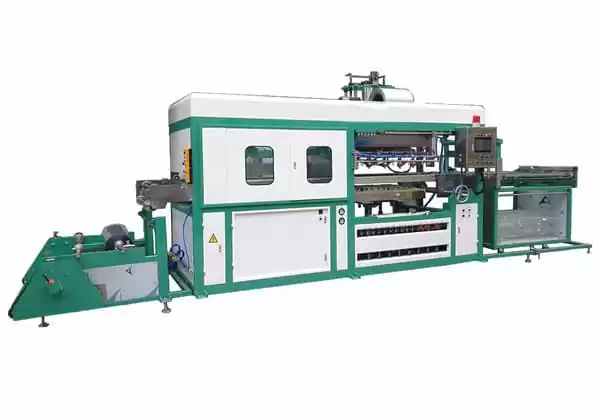
Vacuum Forming Machine
Thermoforming Machine Construction
Clamping Device
When the hot plastic sheet is formed, the sheet is held in place on a clamping device. Clamping devices that facilitate the fixation of sheets of various sizes are often used on general-purpose and composite thermoforming machines. Some have the entire molding machine equipped with a clamping frame.
Clamping devices can be divided into two categories: one is frame type and the other is split type. The frame-type clamping device consists of upper and lower frames. The sheet is sandwiched between two frames. When the frame is open, the lower frame generally remains fixed. The lower part of the upper frame of various types of single-station molding machines is directly fixed on the molding chamber. Manual and semi-automatic molding machines for loading parisons and removing finished products by hand, when the frame size is large, are equipped with safety operating devices within the frame opening range.
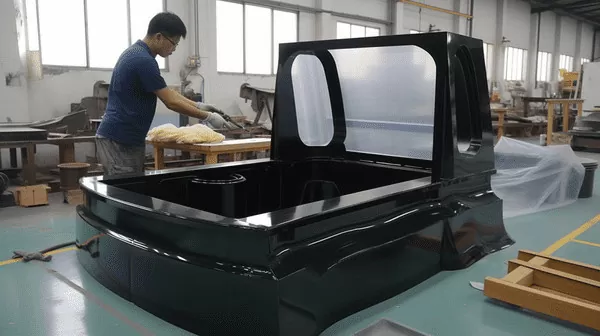
For parisons with large slippage during molding, the clamping force is required to be adjusted within a relatively wide range. To this end, two rubber-covered rollers are used to press each other with springs and are equipped with a pressure adjustment device. The clamping of the continuous pull tab forming machine is the joint action of the zippers on both sides and the front and rear gates.
It is best to use automatic control for the clamping device so that it can act quickly and help improve the quality and efficiency of the parts.
Heating System
One of the main processes in the vacuum molding process of thermoplastic sheets and films is sheet heating. The duration and quality of electric heating depend on the structure of the heater, the thermal inertia of temperature heat transfer behind the radiating surface, the distance between the sheet and the heat gun, the radiant energy absorption coefficient, the characteristics of the heating elements and the thermophysical properties of the material. Commonly used heaters include electric heaters, crystal radiators and infrared heaters.
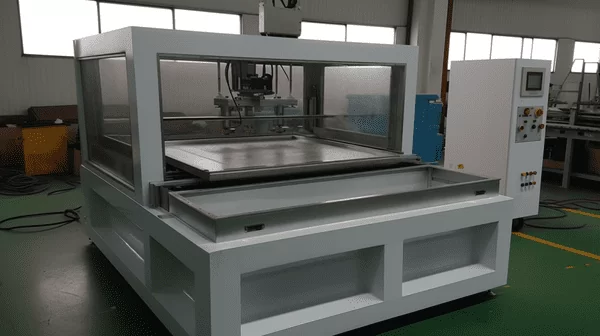
Vacuum System
The vacuum system consists of a vacuum pump, a gas tank, valves, pipelines, and a vacuum meter. In vacuum molding, a separate vacuum pump is often used. The vacuum degree of this pump should reach 0.07~0.09 Mpa (520mmHg) or above. The gas storage tank is generally a cylindrical box welded with thin steel plates, with an oval bottom. The capacity of the gas tank should be at least half greater than the capacity of the largest molding chamber. On the vacuum line, appropriate valves must be installed to control the narrow vacuum capacity.
The rotational power of the vacuum pump is determined by the size and molding speed of the molding equipment. Larger or faster molding speed equipment is often as large as 2-4KW. The size of the vacuum central system depends on the specific production and development requirements of the factory.
Air Compression System
The pneumatic system can be composed of the molding machine itself with a compressor, a gas storage tank, a workshop main pipeline set, valves, etc. The molding machine requires compressed air with a pressure of 0.4-0.5MPa, and piston air compressors are widely used in various vacuum molding machines. Large spiral air compressors can also be supplied from the whole factory.
In addition to being used in large quantities for molding, compressed air is also partially used for demoulding, external cooling of the initial product, and power to control the movements of the mold frame and running sheets.
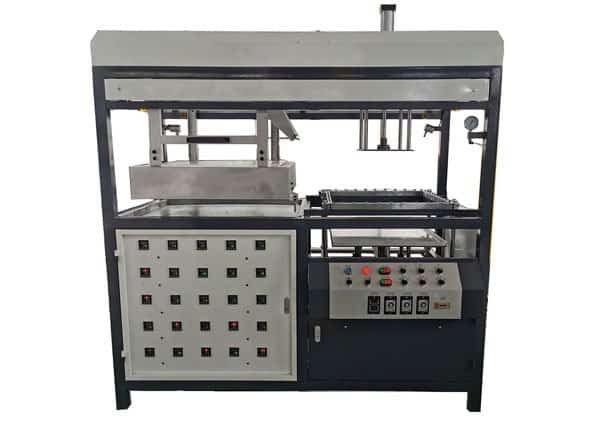
Cooling System
In order to improve production efficiency, vacuum molded products often need to be cooled before demoulding. Ideally, both the inner and outer surfaces of the part in contact with the mold are cooled, and it is best to use a mold with a built-in cooling coil.
For non-metal molds, such as wood, gypsum, fiberglass reinforced plastic, epoxy resin and other molds, since water cannot be cooled, air cooling can be used instead, and additional water mist can be added to cool the outer surface of the vacuum blister molding parts.
If natural cooling is used during production, annealed parts can be obtained, which is beneficial to improving the impact resistance of the parts. Although water cooling has high production efficiency, the internal stress of the parts is relatively large.
Demolding System
Demolding is to move the product out of the mold, usually whether it is a concave mold or a male mold. In most cases, the product is close to the mold due to cooling and shrinkage, so it is demolded through a vacuum suction hole or blowing in the opposite direction.
Especially for molds with small demoulding slopes or molds with concave molds, the demoulding mechanism is used to push or vibrate the mold at the same time. Sometimes a mold release agent is applied to the sheet and the mold or the surface of the mold is sprayed with Teflon.
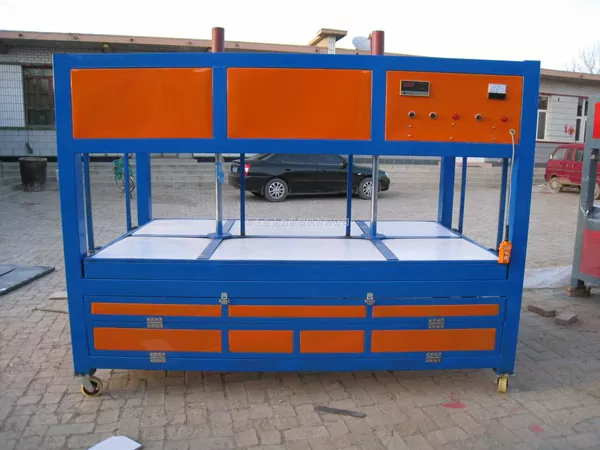
Control System
The control system generally includes the control of various parameters and actions of instruments, meters, pipes, and valves during vacuum blister molding, finishing, and other processes. Control methods include manual, electrical-mechanical automatic control, computer control, etc. The specific selection should be comprehensively considered based on the initial investment in labor costs, technical requirements, raw material costs, production and maintenance equipment costs and other factors.
Application of Vacuum Forming Machines
Plastic packaging industry (blister packaging, plastics, batteries, toys, gifts, hardware, home appliances, electronics, stationery, decoration).
Food packaging industry (fast food boxes, fruit trays, cookie boxes).
Pharmaceutical industry (pill packaging, tablet packaging).
Industrial cooling tower cooling water deflector, etc.
Manufacturing industries such as decorative three-dimensional relief patterns, plastic ceilings, wall panels, automotive materials, and sanitary equipment.
Suitable for producing sheets of various colors: polyethylene PS, polyvinyl chloride PVC, plexiglass, ABS, polymethyl methacrylate, flocking sheets, environmentally friendly sheets APET, PET, PP, etc., photodegradable materials, biodegradable Materials and other plastic products.
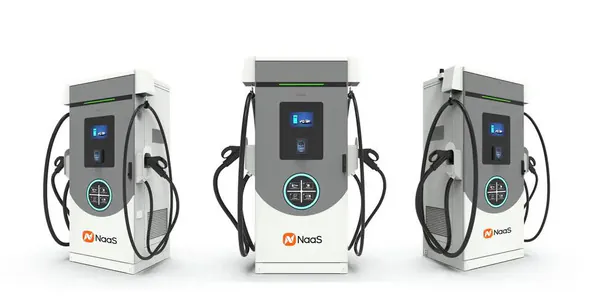
How to Maintain the Thermoforming Machine?
Thermoforming machine is a kind of machine equipment widely used in materials packaging, beverage bottle preparation and other industries. It is used to heat and soften plastics and shape them into finished products of a specified size and shape. In order to ensure the normal operation of the thermoforming machine and extend the service life of the machine, regular maintenance is very important.
Thermoforming process is also called vacuum forming process. It uses the host to heat and soften the raw materials, and then uses the vacuum pressure generated by the vacuum pump to absorb the air between the PVC, PET and other material films and plates, and adsorb them to the surface of various shapes of plates. After cooling, Get the desired shape.
The main structure of the fully automatic thermoforming machine consists of a material film frame, an automatic skin cutting knife, a pneumatic pressure frame, an automatic pneumatic lock for the frame, a workpiece platform, a heating and adsorption host, a joint venture vacuum pump, a high-definition multi-mode computer touch screen, a viewing window, It is composed of cooling function when the finished product leaves the warehouse, a chrome-nickel wire heating tube, and an aluminum row for auxiliary heating.
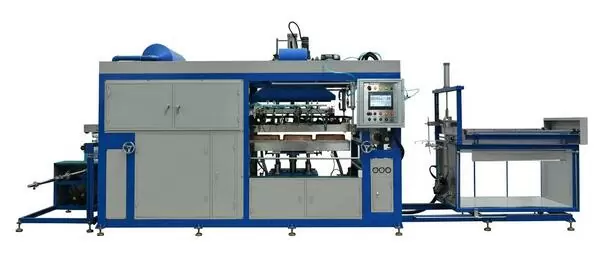
The pneumatic device is the main power source. The cutter pressure frame lock cooling system is a fully automatic control system composed of electric, reducer, time relay, and travel switch. It is a typical electromechanical integrated molding product, involving It has a wide range of functions and is very different from traditional machine tools in terms of fault diagnosis and maintenance.
Therefore, fully mastering the relevant technologies for fault diagnosis and maintenance of automatic thermoforming machines has attracted more and more attention from relevant units and employees. Fault diagnosis and maintenance of fully automatic thermoforming machines has become the key to correctly maintaining and personal protective equipment. One of the key factors. The following are the maintenance methods for thermoforming machines:
Machine Cleaning
After completing the work on the thermoforming machine, after shutting down, the surrounding debris and dirt in the machine should be removed to keep the surroundings and inside of the machine clean and tidy, so as not to affect the normal operation of the machine next time. Vacuum cleaners of machine is also crucial to achieve quality control in vacuum formed parts. During use, the parts of the thermoforming machine will shed some burrs, plastic and other residues. If these residues are not removed in time, the molding effect of the product will be affected. Therefore, various parts need to be cleaned regularly to interior and exterior parts.
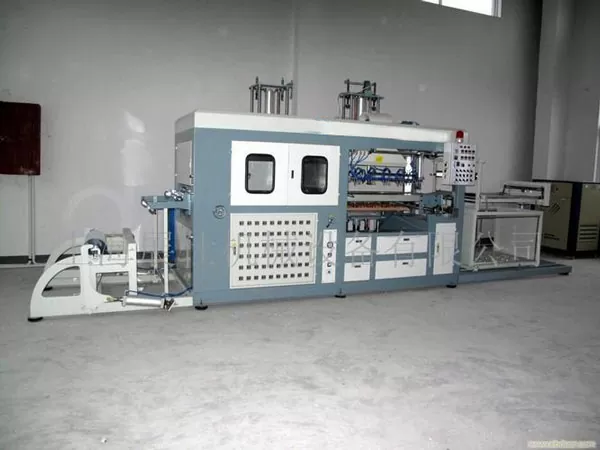
Apply Oil Regularly
Thermoforming machines are heavy-duty equipment that require frequent oiling to reduce wear on cables, brackets, and other components. Proper lubrication can effectively reduce worn or damaged parts, machine noise and extend the service life of the machine.
Each sliding guide column, bearing and sprocket must be kept in good lubrication condition and should be lubricated regularly.
Remove the workbench panel regularly, clean the dust on the bottom of the workbench and the vacuum filter, and allow the vacuum pipeline to pass.
Guide Strip
Because the plastic will flow onto the guide strip of the thermoforming machine after melting, so during the use of the thermoforming machine, the plastic residue on the guide strip of the thermoforming machine should be cleaned in time. If not cleaned, the residue will have an adverse effect on the use of the guide strips, and may even affect the molding of the product and deteriorate the quality of the finished product.
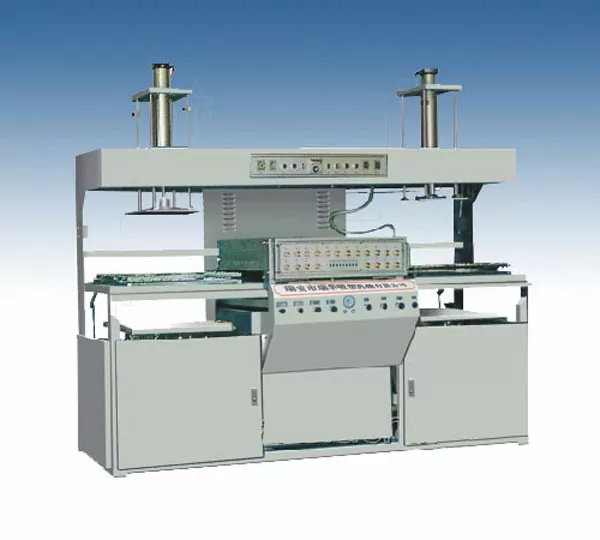
Inspection of Electrical Parts
The electrical system of a thermoforming machine is its core part and one of the most prone to problems. In order to avoid accidents, the electrical system needs to be checked regularly, including checking whether the wires are stuck in the machine, whether the cables, plugs, etc. are loose or damaged, etc. At the same time, ensure that the power terminals of the pressure forming machine are kept dry and clean to reduce the possibility of circuit burnout.
Cooling System Maintenance
Thermoforming machines generate a large amount of heat during operation, which must be dissipated through a cooling system. If the cooling system cannot work properly, it will seriously affect the working efficiency and life of the machine. During maintenance, it is necessary to check whether the fan of the thermoforming machine is operating normally and clean the radiator to prevent dust and other impurities from clogging it and causing poor heat dissipation.
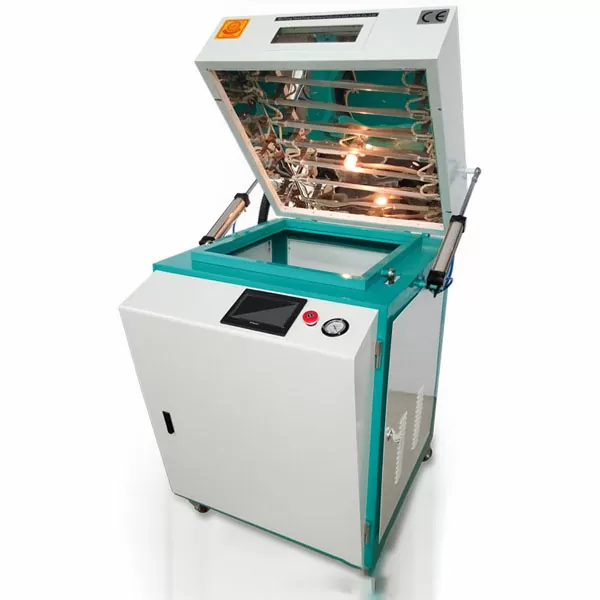
Vacuum Pump
Always observe the amount of oil in the oil mist device, and adjust the amount of oil in a timely manner. When the new machine is in operation, increase the amount (about 3 days for 1 bottle of oil. After one week of use, the amount can be reduced to ensure that each pneumatic component has sufficient lubrication. Automatic continuous vacuum thermoforming Characteristics of the machine. Keep the oil level in the vacuum pump appropriate. If the oil level is too high, the oil will overflow from the exhaust port. If the oil level is too low and the vacuum degree of the vacuum pump cannot meet the requirements, it will also cause damage to the vacuum pump.
Every working shift should first check the oil level of the vacuum pump (the oil should not be lower than the oil level line, and the vacuum pump oil should be replaced once a month.
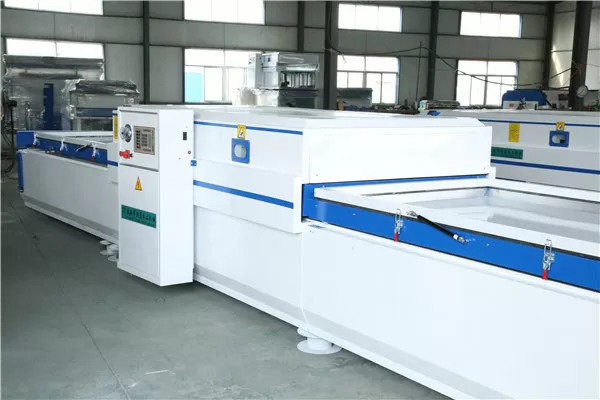
Precautions
1. The power must be cut off when reaching under the guide rail for operation, and there must be no accidental power on.
2. When the machine is using the secondary molding function, please do not put your hands into the molding area to touch the cooling product to prevent your hands from being crushed when the second molding comes down.
3. In the heating area, do not touch the heating device or baked goods with your hands. When shutting down, the heating furnace should be raised.
4. When the product length is less than 800mm, the upper gate and upper mold movements must be synchronized. When partially adjusting the machine, the upper gate should be opened first, and then the upper mold should be opened.
5. When debugging the machine locally, if you use a solenoid valve to energize the machine for debugging, you should pay attention to whether a power outage may cause damage.
6. When receiving pieces of material by hand and feeding them into the knife gate and adjusting the slicing position, the knife gate should be closed. Do not put your hands into the knife gate cabinet in the automatic state.
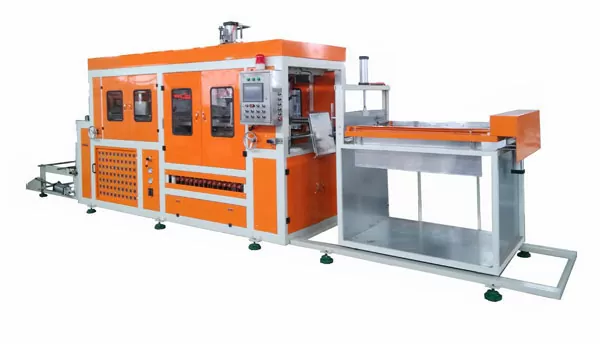
Others
The water filter in the gas line should be drained once every working shift, and the oil mist should be refueled frequently to ensure the normal use of the solenoid valve and vacuum cylinder.
Regularly drain the accumulated water in the air filter of the triple air source, add an appropriate amount of lubricating oil to the lubricator, and adjust the amount of oil mist to an appropriate amount.
Maintain correct temperature. The thermoformed film cannot be sucked in. First, the vacuum negative pressure does not meet the requirements. Second, the heating time is short or the heating temperature does not meet the requirements.
The thermoforming film rebounds, that is, the thermoforming film retracts after the workpiece is added to or removed from the workbench. This is caused by the short thermoforming time, incomplete solidification of the glue, or poor glue quality. The heating thermoforming time should be appropriately extended and the heating temperature should be increased. Or replace the glue with better quality.
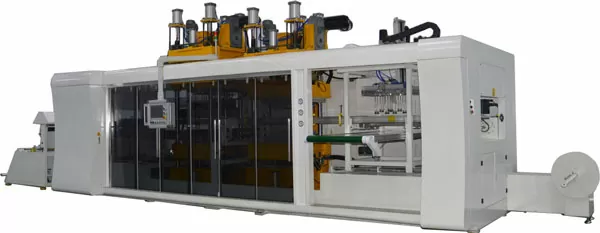
Conclusion
Overall, thermoforming machine maintenance relies on the experience, proper operation, skill level and expertise of the operator. As technology continues to develop, personnel should learn new machine operation theories in a timely manner and regularly invest in machine care and maintenance to ensure the durability of the machine.