Thermoforming involves heating, vacuum forming, cooling and other processes of PVC, PS, PET and other resin sheets in a thermoforming machine to shape them according to the shape of the mold, and then punch them into a single product using a die on a punch machine, and finally packaging products made through folding, punching and other processes.
This kind of packaging product has the characteristics of cheap materials, simple technology, low investment and considerable profits. It is suitable for packaging small daily necessities, small electrical appliances, toys and other commodities. It is not suitable for packaging products with high cushioning requirements and heavy products.
Compared with traditional cold forming processing technology, hot forming process is characterized by a constantly changing temperature field on the processed sheet. Under the action of the temperature field, the basic structure and mechanical properties inside the sheet change, resulting in changes in the stress field of the sheet. At the same time, the stress field of the material reacts on the temperature field. Therefore, the vacuum forming plastic manufacturing process means that the internal temperature field and stress field of the sheet coexist and Mutually coupled change processes.
There are several thermoforming methods used in actual production, and the most basic ones are six: differential pressure forming, overmolding, plunger-assisted molding, suction molding, countermolding, and twin sheet forming.
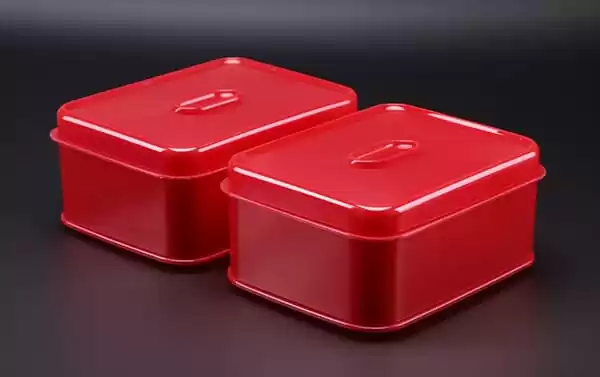
Ⅰ. Thermoforming Production Process
The main production processes of thermoformed products include mold removal, pull tabs, punching, folding, punching, packaging, etc.
Mould or Drawing
A thermoforming project starts with design, which requires a model or drawing of the product, or a sample provided by the customer.
Mold Design & Making
After the customer confirms the sample, the plaster mold used for proofing is used as the master mold. After electroplating copper, the production mold is made according to a certain quantity and position. There are three types of conventional molds: plaster mold, copper mold, and aluminum mold. The plaster molds are mainly used for proofing and generally cannot be used for mass production. The production time is generally 24 hours.
The copper mold is a plaster mold electroplated with a layer of copper, which has enhanced strength and wear resistance and is not high in cost. It is the most commonly used mold in production. The general production cycle is 100 hours, at least 3 days, and the service life is about 100,000 pieces. When the quantity reaches more than 1 million, aluminum molds can be made.
The aluminum molds are made of pure aluminum, which is costly and requires machine processing. The general mold making time is 3 days. Aluminum molds have good production quality, fast heat dissipation, high product precision, and long service life. If the customer requires precise products and the copper mold cannot meet the accuracy requirements, aluminum molds must be made even if the quantity is small.
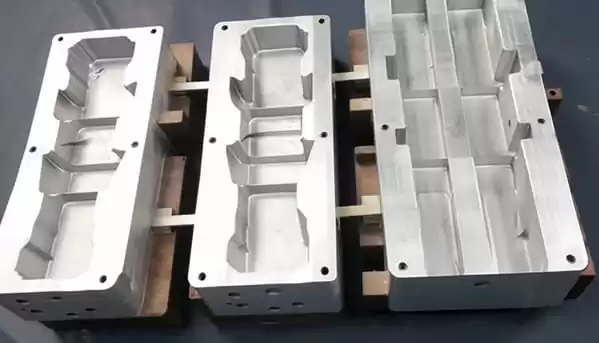
Install the Mold
Based on product and material information, the mold’s cavity count and expected cycle time can be estimated. With this data, the moldmaker has all the details to build the tooling accordingly. The mold consists of two mold halves, each mounted on a removable platen of a vertical toggle press.
Heating & Forming
The thermoforming machine heats the raw material coils or plastic sheets through the vacuum forming machine, vacuum thermoforms them, and cools them, and then automatically cuts them into predetermined sizes. This process is the most important process of pressure forming.
The length of the sheet is between 600 and 1170mm according to actual needs. Different materials, different thicknesses, and different temperature adjustment requirements require considerable experience from the startup personnel. The adjustment test usually takes 3 pictures.
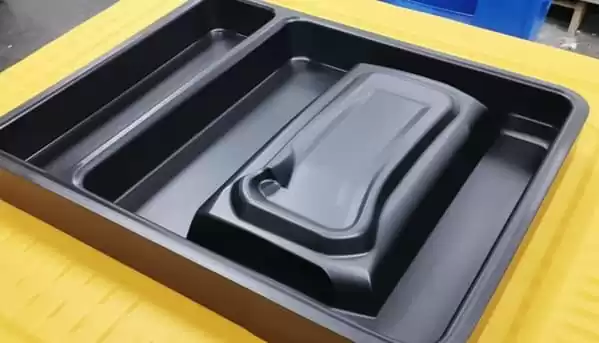
Punching
After heated plastic sheet and forming, there are usually multiple products (according to the number of mold rows), which need to be punched into a single product on a punch. This process is called punching.
If the customer has special requirements, this process should be added when perforating the thermoformed part.
Folding
For some products that need to fold over two or more corners of the thermoformed product to insert paper cards, this process is required. This process is completed by a folding machine.
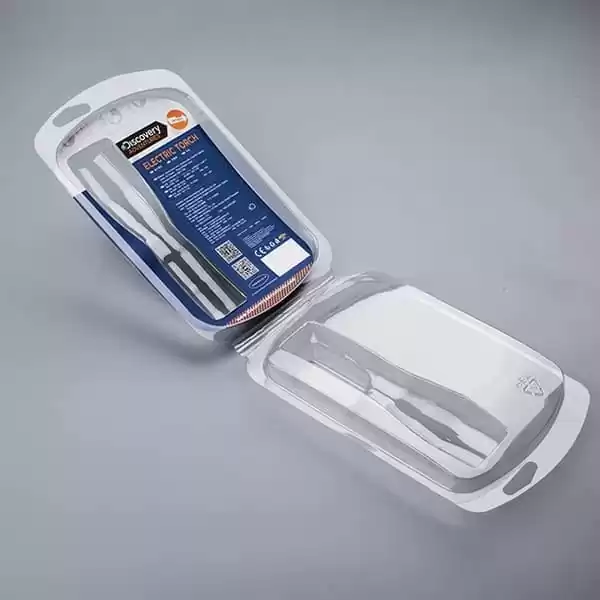
Package
Must pay attention to the packaging of thermoformed products, and determine the appropriate packaging method according to the strictness of customer requirements, product materials, shapes, etc.
If the customer has no special requirements, packing and plastic bags can be used. For products that are white or brightly colored, easily scratched by friction, or cannot attract dust or fingerprints, gloves are often worn during production.
Ⅱ. Thermoforming Materials
Commonly used vacuum forming materials include PVC (accounting for approximately 50%, density is 1.36g/cm³), PS (accounting for approximately 30%, density is 1.06g/cm³), PET (accounting for approximately 10%, density is 1.39g/cm³) , PP (about 10%, density is 0.92g/cm³).
Among them, the maximum thickness of PVC is generally 0.8mm, and that of PS is generally up to 1.2mm. Films exceeding this thickness are difficult to pull and may easily cause damage to the equipment.
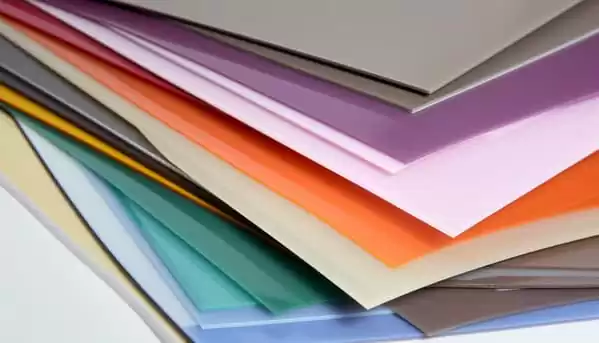
The color of the material is generally determined according to the customer’s requirements. Generally, PANTON color standards, color drafts, color separation standards, etc. need to be provided. The customer can also specify the approximate color and provide the customer with the color based on the product inventory. If there is no requirement from the customer, generally colorless and transparent materials that are easiest to produce can be used.
If you order colored sheets, they generally need to be more than 2 tons before they can be customized. Colored materials are denser than transparent materials. Flocking materials generally use PS materials with smaller density. If the density is high, it is easy to produce lint-free parts of the surface after stretching.
Generally, materials with brighter colors are easier to produce and do not have high requirements for packaging. Scratches on light-colored materials are easy to see, so packaging requirements are strict. Generally, flocking materials need to be protected from scratches and indentations.
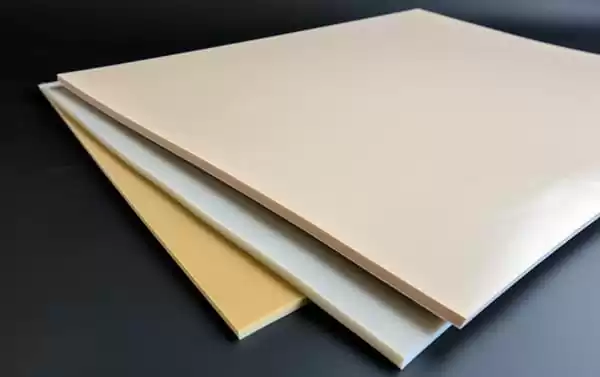
When the products are put together, friction will easily occur in the tight contact areas and cause them to turn white. In places like this, special attention must be paid when packaging. If the requirements are strict, consider using plastic bags, copy paper and other methods for protection. Flocking materials are generally ordered according to length (meters).
Material properties generally include anti-static properties. Anti-static materials are produced by soaking or adding anti-static ingredients. The latter method has long-lasting anti-static properties. The static value of anti-static materials can generally reach 106~1012Ω.
In addition, there is environmental protection, among which APET is the most environmentally friendly and PVC is recyclable. Generally speaking, the thicker the material, the longer it takes to heat and the slower the production speed. The thinner the material, the faster it can be produced, but the longer the roll will be.

Ⅲ. Thermoforming Mold
Lower Mold
The lower mold is an essential mold in thermoforming production. According to different production processes and materials, they can be divided into plaster molds, copper molds, and aluminum molds. When customers provide samples, drawings or physical objects, plaster molds for adding samples need to be made.
The gypsum mold is made of gypsum powder and water is added to it to set it into a certain shape. It hardens after dehydration to form a mold. Materials and tools such as gypsum powder, drill bits, emery cloth, and wooden boards are required. Because it is handmade, there will be a deviation of about 2mm from the drawing. Plaster molds can be prototyped directly after being made and are not suitable for mass production.
The plaster mold can be modified after it is formed, and it is generally easier to make it smaller than to make it bigger. After the customer confirms the sample, the proofed plaster mold can be used as the seed mold (master mold), and multiple sub-molds can be produced according to production needs. The size of the sub-mold will not deviate greatly from the seed mold, generally around 0.5mm.
After the lower mold is made, it needs to be fixed on a plywood about 8mm thick, and then it can be mounted on the mold basin during production. When the heated sheet passes through the mold, it is sucked by the vacuum pump and attached to the lower mold to make a product with the same shape as the lower mold.
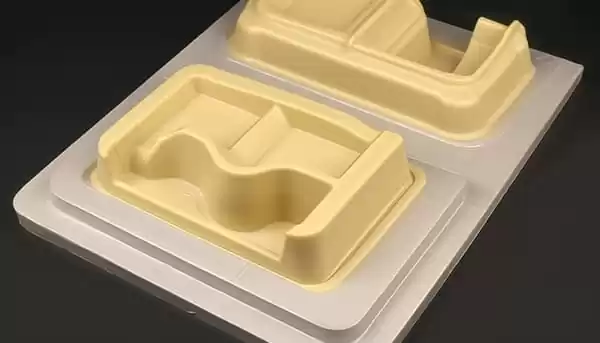
Upper Mold
Sometimes vacuum suction alone is not enough to shape the product, and a certain external force needs to be applied to make the upper mold. The upper mold is not required for all products, but depends on the needs of production.
When testing the machine, if the thermoforming is not good and a upper mold is needed, the operator will make the upper mold according to the shape. The material of the upper mold is generally iron or wood, and the surface in contact with the product needs to be wrapped with soft sponge or flannel.
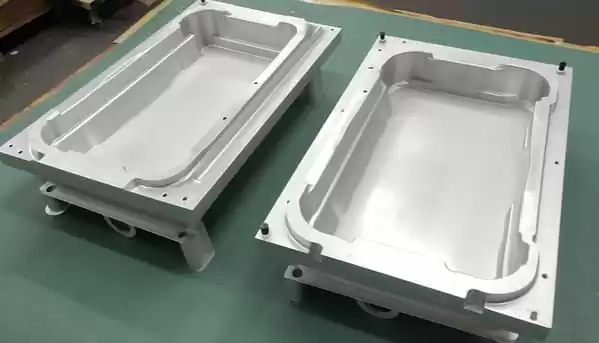
Cutting Die
Generally, multiple vacuum forming molds are used to open multiple molds. After forming, they need to be cut into finished products according to the size and shape of the product. The process of cutting into finished products is the punch press, and the mold used is the cutting die.
Cutting die can be divided into three types according to different materials and production processes: iron dies, wood die, and laser cutting die. Among them, iron die are thicker and can generally be made into cutting dies with more regular shapes, such as rectangles, ovals, etc., and are not suitable for shapes that are too curved.
The blade used in the wooden die is the beer machine cutting die used for color boxes. It needs to be stacked with a certain number of layers according to the height of the product, and sometimes a cushion is required. For cutting dies that require higher precision, laser die can be made, similar to wood sample knives.
After the die is made, the product that needs to be positioned generally needs to be fixed with a finished product in the die to facilitate positioning when punching the product. For products that do not require positioning, such as edgeless thermoformed products, iron knives are generally used as molds.
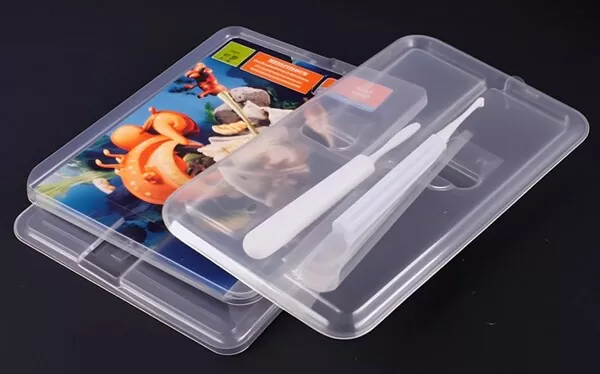
Ⅳ. Dimensions and Tolerances
Thermoforming dimensions can be obtained in three ways: copying according to customer samples, making molds based on drawings, and designing by yourself based on the actual object. Because the shape of pressure forming is generally customized based on the actual object, the shape is often irregular. Many dimensions are inaccurate or cannot be marked when the drawings are made, so there is a large deviation when making according to the drawings. For the sake of accuracy, it must be accompanied by a physical trial installation. The size deviation of products made based on sample replicas is not large.
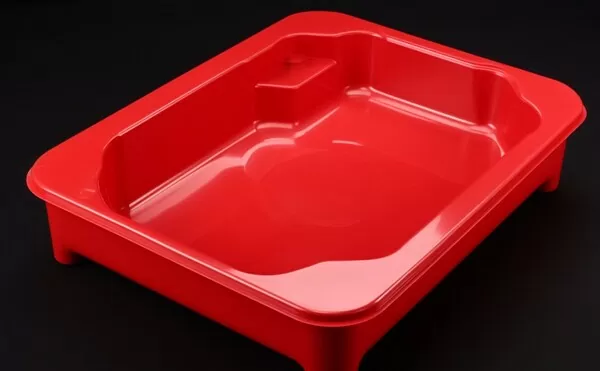
The general thickness tolerance is 0.1mm, and the product deviation is ±2mm. The main reasons for tolerance are:
1. Deviation caused by manual mold removal. This deviation is generally less than 2mm.
2. Deviation caused when the seed mold copies the sub-mold. This deviation is small, generally less than 0.5mm.
3. Thickness deviations in the same mold caused by different materials and thermoforming temperatures. This deviation is small, generally less than 0.1mm.
4. The thickness tolerance depends on the specific situation. The larger the same area is stretched, the thinner the thickness of the piece becomes. Different operators and different forming temperature will also make the thickness of the same part different.
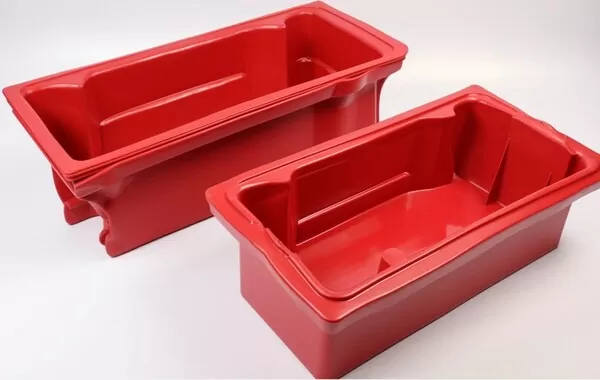
Among the above reasons, the first one is the main reason for dimensional tolerance, but because the mold can be modified and corrected, the deviation of thermoforming process can generally be controlled within 2mm.
It should be noted that the material thickness is two sizes (0.05mm) smaller than the finished product thickness. Although there are phenomena such as when the surface area of the finished product is much larger than the surface area of the material, the thickness of the finished product will be much smaller than the thickness of the material, the surface area of the finished product is much larger than the surface area of the material, and the thickness of the finished product will be much smaller than the thickness of the material, but overall Generally speaking, the general difference is 0.05mm.
Vacuum forming is a very definite product. If you want the size to be right, you must take the actual product and try it out.
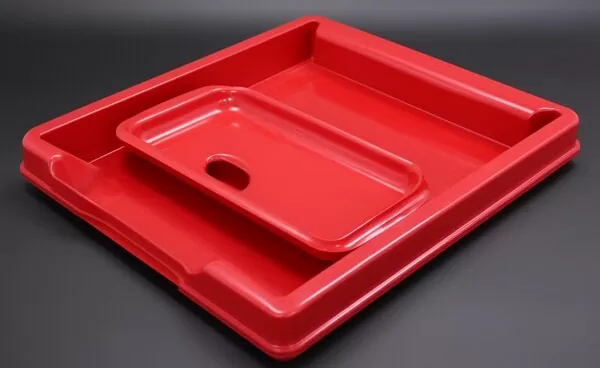
Ⅴ. Draft Angle
All products stamped with molds need to set the draft angle during design, and the same is true for thermoforming. The general draft angle for thermoforming is 3°. The draft angle will cause the size of the upper surface to be smaller than the size of the lower surface. If the thermoforming is placed in a box, there will be a gap between the upper surface and the box wall. When the draft angle is the same, the size of the gap is related to the height.
Calculation Formula
The calculation formula is: d=h×tgθ
d——Size of the gap on each side.
h——Height of thermoforming.
θ——Draft angle, usually 3°.
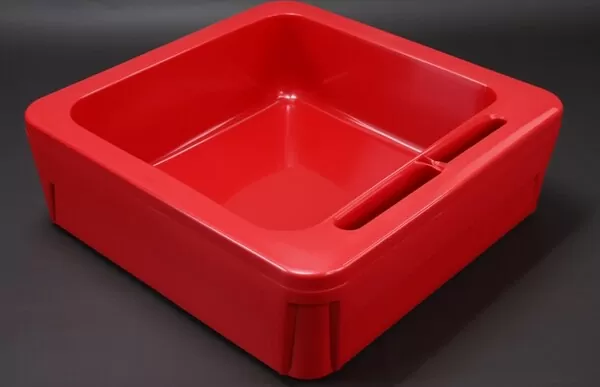
Ⅵ. Mold Layout and Material Setting
Mold arrangement refers to arranging the molds on the mold plate and fixing them. The distance between the molds depends on the height of the product. The general rule is that the distance between the molds is equal to the height of the mold, and the distance between the mold and the four sides of the mold plate is equal to the height of the mold divided by 2. The high point of the mold refers to the highest point of the mold.
The height of the product refers to the highest dimension of the product. See Figure 2-1. Neither h1 nor h2 is the height of the product. The largest h is the height of the product.
When arranging the mold, the width must be arranged to the edge. The length can be more or less, but no more than 1120mm at most and no less than 600mm at least. Between 600 and 1120mm, the longer the better. The number of molds for APET materials cannot be too many, between 600 and 800.
The mold plate width plus 50mm equals the material width, and the mold row length plus 50mm equals the sheet length.
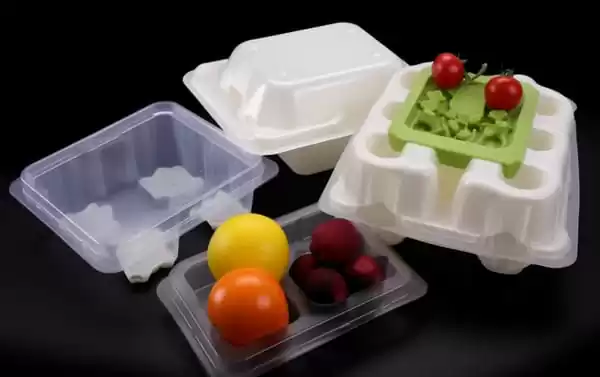
Conclusion
Thermoforming is a process that uses high temperature and high forming pressure to form raw materials into products of the desired shape and structure through steps such as heating, air pressure regulation, and cooling. This process can be used for processing materials such as plastics, metals and ceramics. By controlling parameters, products with different properties, shapes and sizes can be manufactured. The hot press molding process is widely used in automobiles, electronics, aerospace and other fields, providing high-quality products to all walks of life.
Thermoforming is different from injection molding, blow molding, rotational molding and other forms of processing plastics. Thin gauge thermoforming is used primarily to create disposable cups, containers, lids, trays, blisters, clamshells and other products for the food, medical and general retail industries. Thick-gauge vacuum forming includes parts as diverse as car doors and dashboards, refrigerator liners, utility vehicle floors and plastic pallets.