Introduction:
In the domain of polymer fabrication, vacuum forming emerges as a pivotal modality, involving the process where a thermoplastic sheet, upon reaching a malleable state through thermal application, is subsequently contoured over a delineated mold. This technique is lauded for its adaptability, efficacy, and its proficiency in generating an expansive spectrum of artifacts, ranging from encasement materials to vehicular components. Yet, in any fabrication process, the primacy of superior-quality outcomes cannot be overstated, and within the vacuum forming problems, a predominant challenge encountered is the emergence of vesicles within the culminating product.
The manifestation of these vesicles transcends mere superficial imperfections; it profoundly undermines the structural soundness and functional efficacy of the molded plastic. These air pockets, frequently ensnared within the plastic stratums or at the juncture vacuum voids with the mold, engender vulnerabilities in the substrate, potentially precipitating product malfunctions or diminution in longevity. For sectors dependent on the resilience and dependability of vacuum-molded elements, such as the automotive, aeronautical, and consumer merchandise industries, obviating bubble formation holds paramount significance.
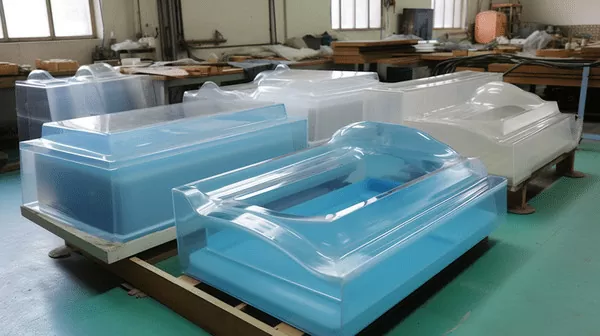
Confronting the quandary of vesicles in vacuum-molded items is thus not solely a quest for aesthetic enhancement but a vital endeavor to uphold the benchmarks of robustness, endurance, and comprehensive quality that patrons anticipate. This discourse ventures into the multifaceted aspects of vesicle genesis in vacuum forming – scrutinizing its origins, the repercussions on product caliber, and the avant-garde stratagems to circumvent this prevalent impediment in polymer fabrication.
The Science Behind Bubble Formation
Causes of Bubbles in Vacuum Forming
In the domain of vacuum forming, the emergence of vesicles detrimentally impacts the integrity of the end product. A profound comprehension of the genesis of these vesicles is imperative in formulating efficacious rectifications. Enumerated hereunder are the predominant elements contributing to vesicle genesis:
Disparity in Thermal Conditions of Melt and Mould
Thermal Incongruities: The vacuum forming procedure necessitates a meticulous equilibrium between the heat of the molten polymer (melt heat) and that of the mould. Excessive heat in the polymer or insufficient heat in the mould can precipitate uneven congealing, engendering vesicle emergence. Conversely, an overheated mould can provoke heat gun the polymer to exceed its thermal threshold, fostering vesicle formation.
Equitable Heat Allocation: It is paramount to ensure a uniform thermal distribution throughout the polymer sheet. Disproportionate heating can render certain zones more prone to vesicle development, owing to variances in material flux and cooling velocities.
Inefficacies in Vacuum Pump and Atmospheric Pressure Dynamics
Vacuum Pump Efficacy: The performance of the vacuum pump is pivotal. A suboptimal pump may fail to evacuate all the air trapped between the mould and the polymer sheet, leading to the entrapment of air that forms vesicles.
Atmospheric Pressure Variabilities: Atmospheric pressure exerts an influence on vesicle formation. Fluctuations in atmospheric pressure pushing through during the forming process can induce irregular adhesion of the polymer to the mould, potentially resulting in air pockets and vesicles.
Complications Arising from Entrapped Air and Aqueous Vapor
Air Entrapment: During the moulding sequence, may be trapped air, trapped gas particularly if the mould design lacks adequate avenues for vacuum void expulsion. This scenario is commonplace in complex moulds with elaborate details or undercuts.
Aqueous Vapor: Humidity within the polymer material can transmute into aqueous vapor upon heating, generating pressure that culminates in vesicle formation within the polymer. It is crucial to store polymer sheets in arid conditions and pre-dry them when cooling time necessary to avert this predicament.
In summation, discerning these critical factors – thermal equilibrium, vacuum efficacy, and the control of entrapped air and moisture – is fundamental in addressing the vesicle quandary in vacuum-formed merchandise. Proactive engagement with these challenges can enhance the caliber and resilience of the resultant products.
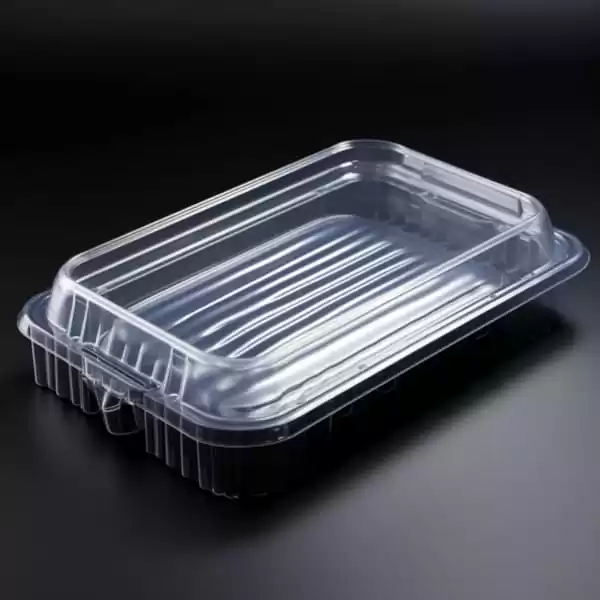
Material and Process Factors
Influence of Plastic’s Movement and Injection Rapidity
Regulation of Plastic’s Trajectory:
The trajectory of the molten plastic across the mold is of utmost importance in vacuum forming. The manner in which the plastic disseminates, occupies the mold’s recesses, and crystallizes greatly influences bubble incidence. Disproportionate distribution can result in uneven thickness, fostering areas susceptible to bubble emergence.
Velocity of Injection:
In methodologies merging vacuum forming with injection molding, the pace at which plastic is propelled into the mold is crucial. Excessive velocity can entrap air, culminating in bubble formation eliminating voids. Conversely, a sluggish injection might not suffice in completely filling the mold, leading to voids and flaws.
Significance of Cycle Duration and Injection Force
Cycle Time Deliberations:
The cycle duration, encompassing plastic and cycle time during the heating, shaping, and cooling stages, necessitates fine-tuning. It is vital that the plastic is afforded ample time to adapt to the mold’s contours without developing internal stress points or irregularities that could instigate bubble generation.
Pressure of Injection:
Analogous to injection speed, the force exerted during injection requires meticulous adjustment. Excessive force on insufficient plastic may cause the plastic to compress against entrapped air, creating bubbles. On the other hand, inadequate pressure might not permit thicker plastic to complete mold occupancy, resulting in imperfect formation and potential bubble dilemmas.
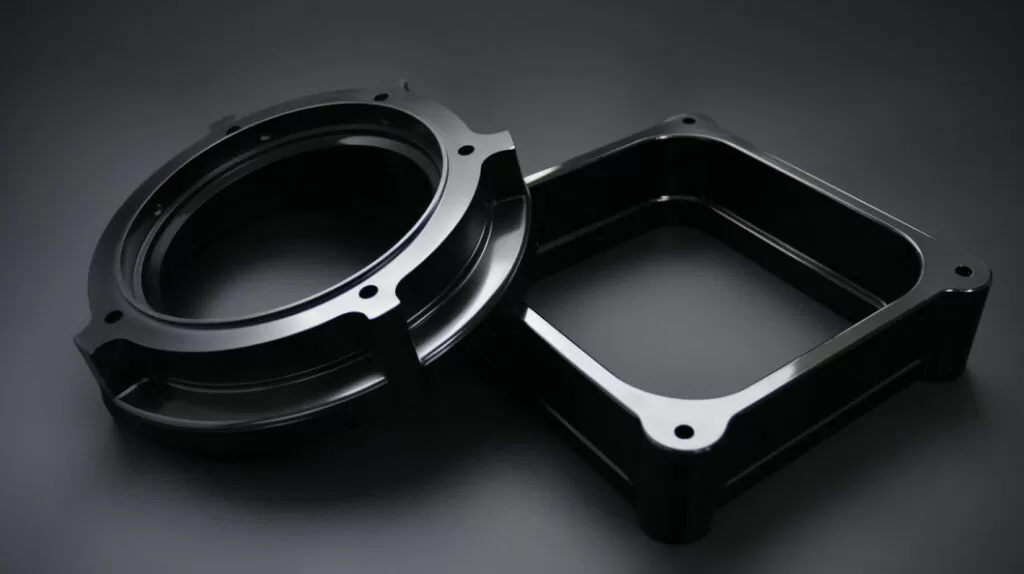
In conclusion, an intricate comprehension of material properties, such as the plastic’s flow and solidification behaviors, combined with precise manipulation of process parameters like injection velocity mold temperature and pressure, is pivotal in circumventing bubble emergence in vacuum-formed items. These aspects, when judiciously controlled, are instrumental in realizing a superior, bubble-free surface in the final merchandise.
Mitigating Tactics for Ensuring Pristine Vacuum-Formed Commodities
To ascertain the fabrication of superior vacuum-molded commodities devoid of any bubble anomalies, a repertoire of mitigating tactics is advisable. These tactics encompass judicious raw material choice, meticulous calibration of machinery, and refinement of the fabrication methodology.
1 Judicious Material Choice and Machinery Calibration
Opting for Substrates with Enhanced Nominal Thickness: The judicious selection of substrates is quintessential in the abatement of bubble incidences. Substrates boasting an enhanced thickness inherently exhibit a heightened resistance to bubble emergence. They facilitate a homogenous dissemination of thermal energy and subsequent cooling, pivotal in precluding bubble emergence.
Precision in Heating Apparatus and Machinery for Uniform Thermal Distribution: The precision calibration of thermal apparatus, such as heat emitters, is paramount. The uniform thermal exposure of the plastic substrate is essential to circumvent thermal anomalies or disparate temperature distributions, culminating in bubble genesis. Periodic upkeep and precise calibration of apparatus ensure unwavering performance and consistency in output quality.
2 Refinement of Fabrication Methodology
Optimization of Material Transit Path and Densification in Robust Sections:
Refining the transit and flow path of the plastic substrate during the molding process is of paramount importance. A balanced and uniform transit of plastic flow front the material, especially in denser sections, is instrumental in averting the emergence of fragile zones prone to bubble formation. Moreover, diligent densification in these sections is crucial to fill potential voids.
Significance of Ingress Point Placement and Intrinsic Stress Management:
In methodologies amalgamating vacuum molding with injection molding, the ingress point’s placement – the juncture where the plastic enters the mold – is critical. This placement significantly influences the flow dynamics and pressure within the mold, impacting bubble formation. Furthermore, managing intrinsic stresses within the plastic, a byproduct of thermal gradients and material flux, is imperative in averting defects such as bubbles.
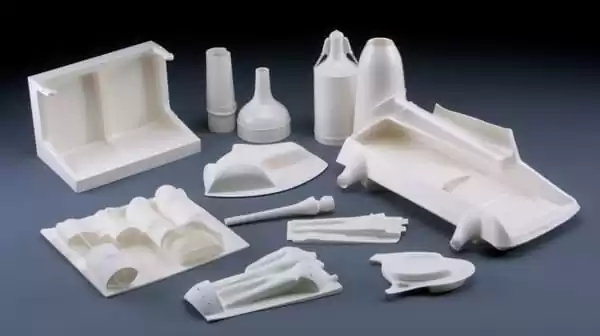
In encapsulation, by meticulously selecting suitable substrates, ensuring uniform thermal exposure with precision-calibrated machinery, and refining the molding process, manufacturers can markedly diminish the incidence of bubbles in vacuum-molded products. These mitigating strategies are indispensable in preserving the integrity and caliber of the end product.
In the realm of plastic fabrication, particularly within the sphere of vacuum forming, the quandary of bubble emergence stands as a paramount challenge necessitating scrupulous focus and a multidimensional strategy. This discourse delves into various facets of this predicament, providing enlightenment on its origins and proposing tactics for its alleviation.
Critical factors instigating bubble occurrence have been pinpointed, encompassing discrepancies in melt temperature and mold thermal states, deficiencies in vacuum apparatus efficiency, and dilemmas pertaining to ensnared air and moisture vapor. Moreover, material and procedural elements, such as the ramifications of plastic flux, the velocity flow pattern of injection, duration of the cycle, and the magnitude of injection pressure, have been underscored as pivotal in determining the caliber of the ultimate product.
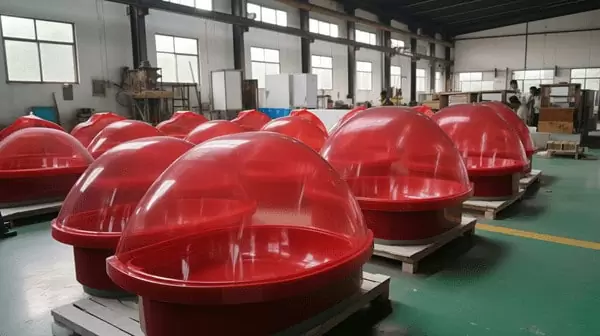
Epilogue
In the realm of plastic fabrication, especially concerning vacuum forming, the quandary of bubble emergence necessitates scrupulous consideration and a composite approach. This discourse has delved into various facets of this quandary, elucidating its origins and proffering tactics for its diminution.
Pivotal elements precipitating bubble emergence, such as disparities in the thermal states of melt and mold, inefficacies in vacuum apparatuses, and dilemmas linked to ensnared air bubbles and aqueous water vapor, have been discerned. The influences of material and procedural variables, encompassing the repercussions of plastic flux, injection velocity, process duration, and injection force, have been accentuated as critical to the integrity of the resultant product.
Preclusive strategies, entailing the selection of materials with congruent characteristics, assuring uniform thermal application and calibration of instruments, optimizing the velocity controlled trajectory of flow, and managing internal tensions, are imperative in fabricating high-caliber, bubble-exempt products. These methodologies not only tackle the immediate issue of bubble formation but also augment the overall excellence and resilience of vacuum-formed items.
The necessity for an exhaustive comprehension and methodology in navigating the complexities of vacuum forming is paramount. Artisans and technicians in this domain must relentlessly pursue an enhanced cognizance of the procedural and material dynamics. In this pursuit, they can instigate and implement efficacious resolutions, culminating in the creation of plastic wares that epitomize the zenith of quality and dependability for diverse sectors.
In summation, addressing the conundrum of bubble formation in plastic manufacturing of vacuum-formed commodities is an intricate task that commands an extensive understanding of both theoretical and applied aspects of plastic fabrication. By amalgamating knowledge, meticulous planning, and precise implementation, fabricators can surmount this challenge, yielding wares that are paragons of quality and steadfastness.