Introduction
In the realm of transformative technologies that have revolutionized the manufacturing landscape, vacuum forming emerges as a triumphant conductor orchestrating a symphony of shapes, designs, and innovations. This powerful process holds the baton of versatility, guiding sheets of plastic on a transformative journey from simplistic flatness to a world blossoming with intricate geometries and functional brilliance.
Vacuum forming, a maestro in the realm of thermoforming processes, crafts a stage where heated thermoplastic sheets gracefully embrace the contours of specialized molds, giving birth to a plethora of applications, from packaging marvels to automotive masterpieces and beyond. At the heart of this transformative odyssey reside the unsung heroes—the male or both male and female tooling mold. These pivotal protagonists play crucial roles, each contributing their unique melodies and rhythms to the symphony of shapes brought to life through vacuum forming.
Our journey aims to spotlight these molds, unraveling their mysteries, exploring their distinctive contributions, and illuminating the pathways of decision-making in their application. Join us as we delve deep into the heart of vacuum forming, celebrating the artistry, precision, and technological prowess embodied in the realm of female and male tooling.
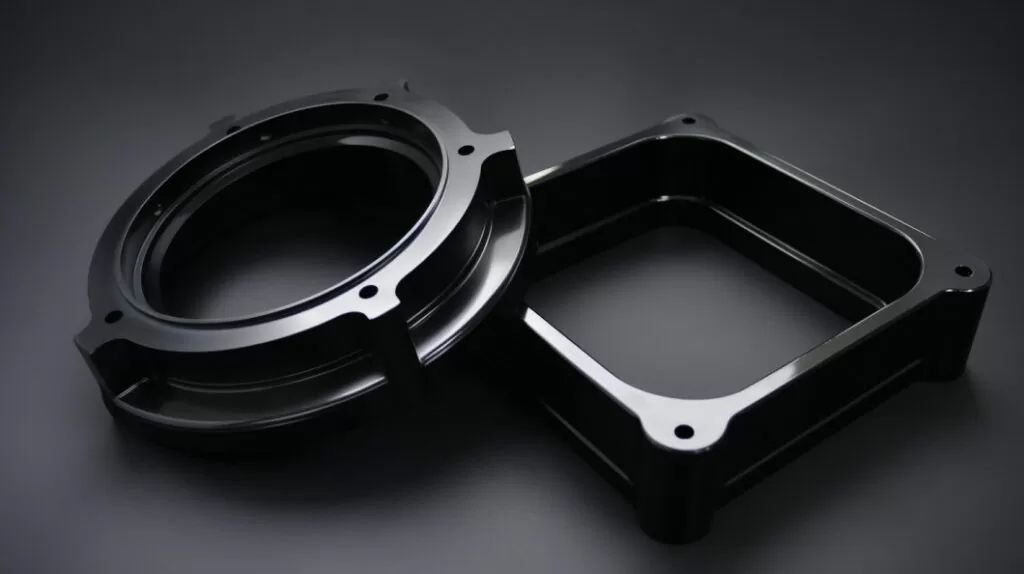
II. Unpacking the Basics
Navigating through the waters of vacuum forming requires us to undertake an investigation that probes its fundamental elements for their roles and significance in orchestrating this transformative process. At its center lies molds – those silent architects which shape vacuum-formed parts’ essences – let’s discover their fundamental definitions and roles; let us bring light on their distinct natures and contributions!
Molds in Vacuum Forming
Vacuum forming molds serve as the essential guides and expert sculptors that steer heated plastic sheets through their journey of transformation. They serve as support structures providing necessary shape, contours and support that softened thermoplastic sheets require in order to transform into beautiful products with functional elegance and aesthetic value.
Molds Provide Direction for Shape and Contour: Molds serve as powerful guides that sculpt plastic into precise forms that mirror an artist’s original designs with exceptional accuracy.
Molds Are Ideal for Detail and Precision: By creating carefully designed surfaces and contours, molds enable the development of details, precision features, and intricate features in vacuum-formed parts.
Differing Between Male and Female Molds
Within vacuum forming’s theater of creation, male and male or female tooling molds emerge as two distinctive characters, each offering distinctive attributes, influences, and potentials to the stage.
Male Molds (Positive Molds): Male molds have an impactful presence that accentuates the exterior appearance of vacuum-formed parts, contributing to defined shapes, sharp angles and precise external features in them. Their prominent protruding surfaces stand out among all their vacuum forming counterparts to dictate outward-facing contours that give products distinct shapes with precise outer features that define shapes for shapes with sharp angles or precise external features – giving these parts their signature looks and characteristics.
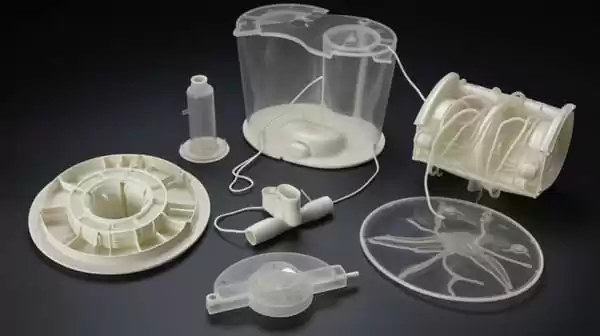
Female Molds (Negative Molds): On the contrary, female molds welcome heated plastic sheets into their recess surfaces for meticulous crafting of internal dimensions of parts and products with features, wall thickness and inner contours that give strength yet detail intricacy. They excel at catering to these features for balance among strength and detail intricacy.
Entaingging in this fundamental inquiry reveals the pivotal roles and unique contributions made by molds to vacuum forming. With these newfound insights we become better prepared to appreciate, analyze, and navigate its complexities as they emerge within this realm of craftsmanship.
III. The Distinctiveness of Male and Female Molds
As we explore vacuum forming, let’s focus on the two main characters—the male and female molds. Each has unique attributes and contributes to crafting vacuum-formed parts. Here, we’ll discuss the qualities of male mold:
External Detailing: Male molds sculpt the exterior surfaces of vacuum-formed parts with precision, defining sharp corners and contours.
Sharp Details: They excel in creating intricate features, making them the preferred choice for external aesthetics.
Material Economy: The elevated design of male molds reduces plastic sheet waste, promoting sustainability in material usage.
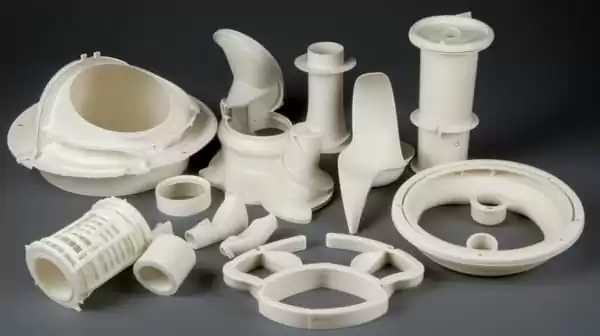
Exposure to Wear: However, due to their exposed nature, male molds can be more prone to wear and tear, affecting durability.
Attributes of Female Molds (Negative Molds):
Internal Precision: Female molds create products with intricate internal detailing. They guide the plastic sheet into recessed surfaces, ensuring precise interior dimensions, wall thickness, and other internal features.
Uniform Wall Thickness: Female molds promote uniform wall thickness, resulting in parts with consistent structural integrity for various applications.
Smooth Exteriors: Female molds produce products with smooth and unblemished exterior surfaces, enhancing the mold surface final product’s appearance.
Enhanced Durability: The recessed design of female molds contributes to enhanced durability, offering a longer lifespan and sustained performance.
In this segment, we’ve explored the attributes of male and female molds, highlighting their distinct contributions to the vacuum forming process. Manufacturers can select the most suitable mold based on project requirements and quality benchmarks for the final vacuum-formed products.
IV. Comparative Analysis: Various Forming Processes
In the realm of plastic manufacturing, a symphony of diverse processes plays, each contributing its unique melodies to the creation of multifarious plastic parts. Each forming process, a soloist in its own right, carries specific attributes and specialties that dictate its role and suitability in various applications. Let us embark on a comparative odyssey, exploring the unique characteristics of pressure forming, injection molding, and twin sheet forming, and unraveling the sophistication and uniqueness they introduce in the world of custom plastic manufacturing.
Pressure Forming and Its Unique Characteristics
Pressure forming, a close relative of vacuum forming, dances to a rhythm of enhanced precision and detail. The process distinguishes itself by utilizing positive pressure in concert with vacuum to ensure the plastic sheet’s intimate conformity to outer surface of the mold, allowing for:
- Enhanced Detailing: The use of pressure facilitates the production of parts marked by sharper detailing, textures, and undercuts.
- Material Distribution: Improved material distribution is achieved, offering a balanced blend of thickness and strength.
- Broad Application: It’s particularly advantageous when manufacturing aesthetic components such as covers, panels, and other visually critical parts.
Insights into Injection Molding
Injection molding, a distinguished performer, directs the orchestra with versatility, speed, and precision. It specializes in the high-volume production of parts by injecting molten plastic into molds, and it harmonizes:
- Efficiency: Known for its fast cycle times, injection molding is a maestro of efficiency and productivity.
- Complex Geometries: It shines when complexity takes the stage, enabling the creation of parts with intricate designs and geometries.
- Consistency: Producing parts with high consistency and repeatability echoes the mastery of this process.
Unveiling the Sophistication of Twin Sheet Forming
Twin sheet forming, a ballet of two sheets harmonizing in a single performance, unveils a landscape of robust, hollow, or double-walled parts. In this sophisticated dance:
- Dual Sheet Fusion: Two plastic sheets are formed and fused together, creating a hollow structure that sings of strength and lightweight harmony.
- Versatility: The process unfolds versatility, allowing for the integration of various design elements such as handles and hinges directly into the parts.
- Application Diversity: It finds its rhythm in diverse applications such as automotive, HVAC, and industrial components where structural integrity is a core requirement.
Through this comparative analysis, the unique rhythms and melodies of pressure forming, injection molding, and twin sheet forming are revealed, allowing us to appreciate the diversity, sophistication, and specific advantages each brings to the concert of plastic manufacturing. Understanding these distinctive characteristics enriches our repertoire, enabling a more nuanced and informed selection of the appropriate injection molding tooling and forming process to resonate with the specific needs and aspirations of each manufacturing project.
V. Decision Criteria: Choosing Between Molds
In the multifaceted world of vacuum forming, decision-making emerges as a critical conductor guiding the symphony of production towards harmony and success. Choosing between male and female molds is a pivotal act, a strategic decision influenced by a spectrum of factors and considerations that resonate with the design aspirations, functional necessities, and the envisioned quality of the final products. Let us navigate through the criteria, exploring the factors and strategies that illuminate the pathway towards making informed and aligned decisions in mold selection.
Factors Influencing the Choice of Molds
A multitude of considerations orchestrate the decision-making process, each playing a significant role in determining the suitability and alignment of the chosen molds with the project’s requirements.
- Design Complexity: The complexity and intricacy of the design often guide the choice. Male molds are often chosen for their ability to impart sharp details and pronounced features on the exterior, while female molds excel in crafting detailed internal geometries and consistent wall thickness.
- Material Usage: Consideration of material economy and sustainability also influence the decision. The structure of male molds often leads to a more efficient use of materials, minimizing waste.
- Durability: The durability and lifespan of the molds come into play, with female molds often showcasing enhanced resilience and longevity due to their recessed design.
- Product Dimensions: The dimensions and depth of the final part also sway the choice. Deeper parts often resonate more harmoniously with the capabilities of female molds.
Strategy and Alignment in Selecting Molds
Strategic alignment in mold selection unfolds as a choreography of analysis, evaluation, and adaptation, ensuring that the chosen molds resonate harmoniously with the project’s objectives and requirements.
- Analysis: Conducting a detailed analysis of the design specifications, functional requirements, and quality benchmarks is essential. It involves evaluating the nuanced aspects such as sharp corners, draft angles, and textured designs that the part must embody.
- Adaptability: Embracing adaptability allows for the exploration of innovative approaches and the optimization of choices, such as the utilization of plug assists or the combination of male and female molds, to achieve the desired outcomes.
- Collaboration: Collaborating with experienced mold designers and technicians opens avenues for insights, guidance, and expert recommendations, fostering informed and strategic decision-making.
Navigating through the decision criteria enriches our strategy, illuminating the pathway with insights and considerations that guide the selection of molds in alignment with the project’s aspirations, design necessities, and quality expectations. In the strategic harmony of these criteria, the choice of molds becomes a well-orchestrated decision that enhances the likelihood of success and satisfaction in the vacuum forming process.
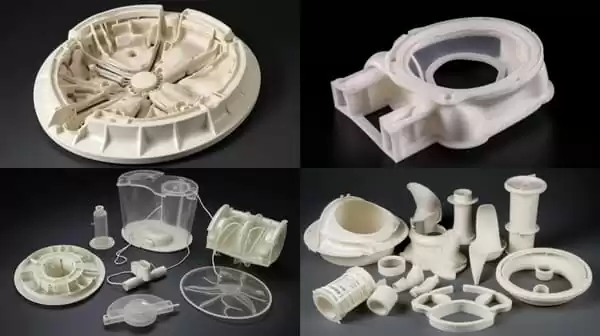
Conclusion
As we conclude our exploratory odyssey through the realms of vacuum forming, we find ourselves enriched with a tapestry of insights, woven with threads of knowledge spanning from the nuanced roles of male and female molds to the pragmatic considerations that govern the art and science of this captivating manufacturing process.
Synthesizing Key Takeaways
- Mold Mastery: The profound understanding of male and female molds, each with its unique attributes and influences on the final parts, illuminates the path of decision-making, allowing for informed and strategic choices that resonate with design aspirations and functional necessities.
- Process Pragmatism: Armed with practical insights into temperature resilience, design precision, and cost considerations, we find ourselves equipped to navigate the terrain of vacuum forming with a balanced perspective that values both quality and economic efficiency.
- Strategic Harmony: The harmonization of various elements, from mold selection to design analysis and cost optimization, unveils a strategic pathway, fostering a symphony of decisions and actions that align with the overarching objectives and quality benchmarks of the vacuum forming process.
Guidance for Navigating the Vacuum Forming Process with Newfound Insights
Embrace the journey of vacuum forming as a continuous learning odyssey, where each step, decision, and adaptation carries the potential to enrich the process, enhance the outcomes, and foster a spirit of innovation and mastery.
- Continuous Learning: Remain open to continuous learning and exploration, allowing the ever-evolving landscapes of technology, materials, and methodologies to enrich your knowledge and practices.
- Collaborative Innovation: Foster a spirit of collaboration and innovation, valuing the insights, experiences, and creativity that each participant brings to the vacuum forming symphony, from designers and technicians to material suppliers.
- Informed Decision-Making: Navigate the pathway of decision-making with a sense of informed confidence, allowing the synthesized insights and understandings to guide your choices towards alignment with your objectives, quality aspirations, and practical considerations.
In the embrace of these synthesized insights and guidance, we find ourselves empowered to navigate the vacuum forming process with a renewed spirit of mastery, strategic harmony, and innovative exploration. May your journey through the realms of vacuum forming resonate with success, satisfaction, and the continuous unfolding of knowledge and mastery.