Introduction
Plastic manufacturing processes play an integral part of many industries, enabling the creation of products we encounter daily. Of all of the techniques available, two notable processes stand out – vacuum forming and injection molding. We will explore both methods here and offer a comparison chart so you can better understand their similarities, differences, and respective advantages – whether you are a designer, engineer, or business owner, understanding these processes will empower you to make informed decisions when it comes to plastic production. So let’s dive in and discover this fascinating world!
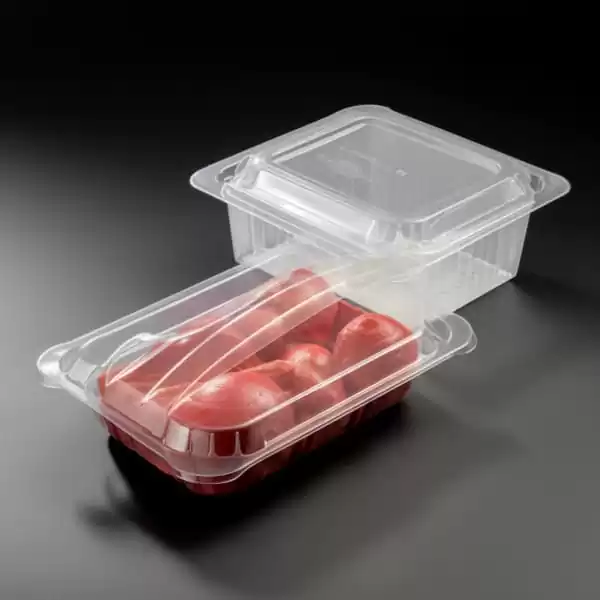
II. Understanding Vacuum Forming
Vacuum forming, also known as thermoforming, is a versatile plastic manufacturing process that involves shaping a mostly thermoplastic material or sheet by heating it and then stretching it over a mold. Let’s delve deeper into the process and its applications.
1.Definition of Vacuum Forming:
Vacuum forming, or thermoforming, is a method of shaping thermoplastic materials by using heat and vacuum pressure.
It allows the transformation of a flat thermoplastic rubber sheet into a three-dimensional shape.
2.The Process of Vacuum Forming:
The first step in the vacuum forming machine is to heat a thermoplastic sheet until it reaches a pliable state. Common thermoplastic materials used include acrylic, polystyrene, and ABS.Once the sheet is heated, it is placed over a mold, which could be made of aluminum, wood, or composite materials.
Vacuum pressure is then applied to the mold, causing the heated sheet to conform to the mold’s shape.
As the vacuum pulls the air between the plastic sheet, and the mold, the plastic material is suctioned tightly onto the mold’s surface, resulting in the desired formed shape.
After cooling and solidification, the formed plastic part is removed from the mold, and any excess material is trimmed.
3.Common Applications of Vacuum Forming:
Vacuum forming finds applications in various industries due to its versatility and cost-effectiveness.
It is commonly used for creating trays, packaging, and disposable containers, especially in the food and retail sectors.
Vacuum-formed parts are also prevalent in te automotive industry, where they are used for interior components, such as door panels and dashboards.
Other common applications include point-of-sale displays, medical equipment housings, and protective covers.
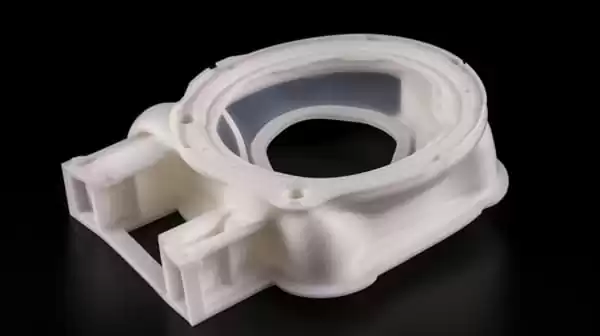
Vacuum forming offers flexibility in terms of design, cost-effectiveness, and suitability for producing large and shallow plastic parts. Its wide range of applications makes it a preferred choice for various industries seeking efficient and economical plastic manufacturing solutions.
III. Exploring Injection Molding
Injection moUlding is a highly precise and widely used plastic manufacturing process. Let’s explore its definition, process, and notable examples of products created through this method.
1.Definition of Injection Molding:
Injection moulding is a manufacturing technique that involves injecting molten plastic material, usually in pellet form, into a mold cavity under high pressure.
The molten plastic material cools and solidifies within the mold, taking the shape of the cavity, and is then ejected as a finished part.
2.The Process of Injection Molding:
The injection molding process begins with the melting of thermoplastic materials in an injection molding machine.
The molten plastic is injected into a mold cavity through a nozzle and a runner system, which channels the material into the mold.
The high pressure applied during the injection phase ensures that the molten plastic fills the mold completely, including intricate details and features.
Once the plastic has cooled and solidified, the mold opens, and the finished part is ejected, ready for further processing or assembly.
3.Precision and Complexity Achievable with Injection Molding:
Injection molding offers exceptional precision and the ability to produce complex parts with tight tolerances.
The high pressure and control provided during the process allow for the creation of intricate designs, fine details, and precise dimensions.
Injection molding enables the production of parts with consistent quality, making it suitable for industries that require high-precision components.
4.Examples of Products Made Through Injection Molding:
Injection molding is widely used across industries to manufacture a diverse range of products.
Toys, such as action figures and building blocks, are commonly produced through injection molding due to its ability to replicate intricate designs and produce large quantities.
Medical devices, including syringes, IV components, and surgical instruments, benefit from the precision and sterile nature of injection molding.
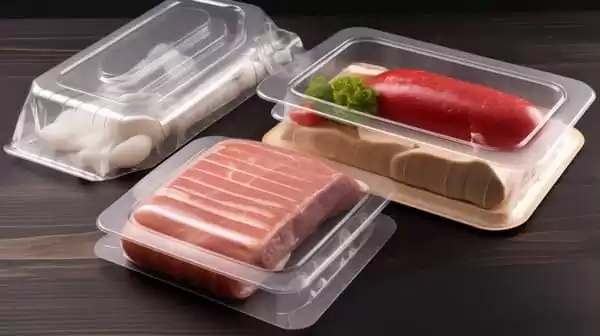
Other examples include consumer electronics, automotive parts, household appliances, and packaging components.
Injection molding’s precision, complexity, and ability to produce high volumes make it a preferred method for manufacturing a wide array of products. Its versatility, combined with advancements in material science and injection molding tooling design, continues to drive innovation across industries.
IV. Comparison: Vacuum Forming vs. Injection Molding
Let’s compare vacuum forming and injection molding to understand their differences and similarities in terms of cost, precision, complexity, material selection, production speed, and lead times.
1.Cost:
Vacuum forming generally has lower tooling costs compared to injection molding.
Vacuum forming molds are simpler and less expensive to produce, making it a more cost-efficient option, especially for smaller production runs or prototypes.
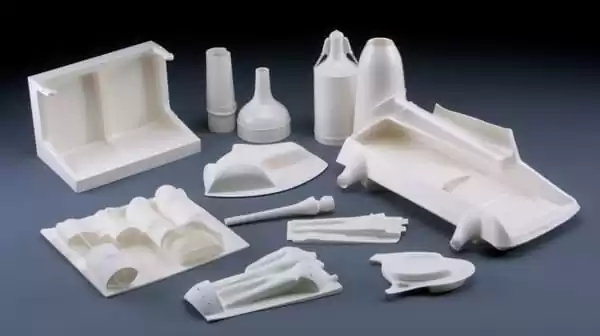
Injection molding requires more complex and expensive molds, but it becomes more economically viable for large-scale production due to its faster cycle times and higher volume capabilities.
2.Precision and Complexity:
Injection molding offers superior precision and accuracy for intricate designs and tight tolerances.
The high-pressure injection process allows for the creation of complex parts with fine det
ails and consistent quality.
Vacuum forming, while capable of producing reasonably detailed parts, may not achieve the same level of precision as injection molding.
3.Material Selection:
Injection molding provides a broader range of material selection.
It can accommodate engineering-grade plastics with enhanced mechanical properties, such as high strength, heat resistance, and chemical resistance.
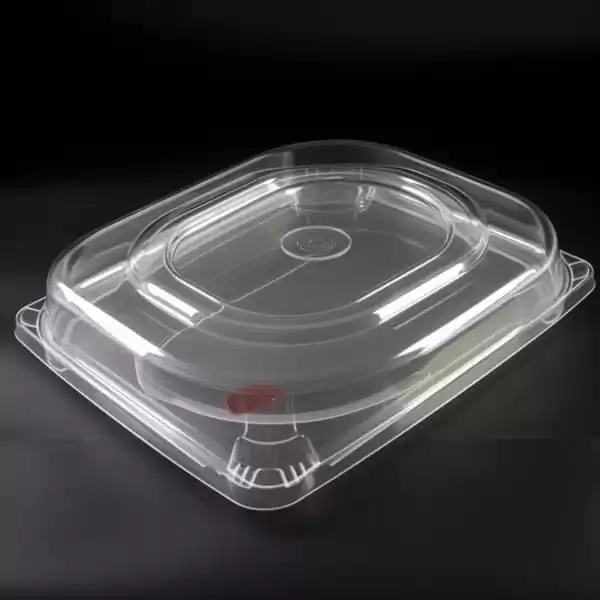
Vacuum forming primarily focuses on standard materials suitable for less demanding applications.
4.Production Speed and Lead Times:
Injection molding is known for its high production speed once the mold is created and set up.
The process allows for rapid and continuous production, making it ideal for large volume manufacturing.
Vacuum forming, while relatively faster than some other plastic forming methods, is generally slower compared to injection molding.
Injection molding typically has longer lead times due to the design, fabrication, and installation of the injection mold, which can take six to eight weeks.
In summary, vacuum forming and injection molding offer distinct advantages and considerations. Vacuum forming is a cost-effective option for smaller production runs or prototypes, suitable for larger parts and simpler designs. Injection molding excels in precision, complexity, and high-volume production, making it ideal for intricate designs and demanding applications. Material selection, production speed, and lead times should also be taken into account when choosing the most suitable manufacturing process for specific project requirements.
V. Advantages and Unique Aspects
Let’s explore the advantages and unique aspects of vacuum forming and injection molding, highlighting their strengths and applications.
1.Advantages of Vacuum Forming over Injection Molding:
Cost Efficiency: Vacuum forming generally has lower tooling costs compared to injection molding, making it a cost-effective option for smaller production runs or prototypes.Large-Scale Designs: Vacuum forming is well-suited for creating larger parts and designs, accommodating a wide range of sizes.
Faster Turnaround: Vacuum forming molds can be produced relatively quickly, resulting in shorter lead times compared to the longer mold fabrication process of injection molding.
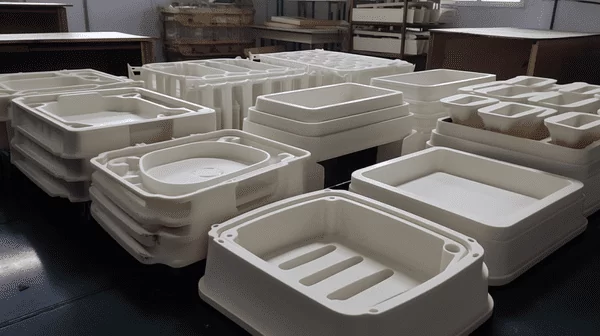
Material Flexibility: Vacuum forming supports a variety of standard materials suitable for less demanding applications, providing versatility and options for different requirements.
2.Benefits of Injection Molding in Precision and Material Selection:
Precision and Complexity: Injection molding offers exceptional precision and the ability to produce complex parts with tight tolerances. It ensures consistent quality and dimensional accuracy throughout high-volume production.
Material Selection: Injection molding provides a broader range of material selection, including engineering-grade plastics with enhanced mechanical properties, such as strength, heat resistance, and chemical resistance. This makes it suitable for demanding applications that require specific material characteristics.
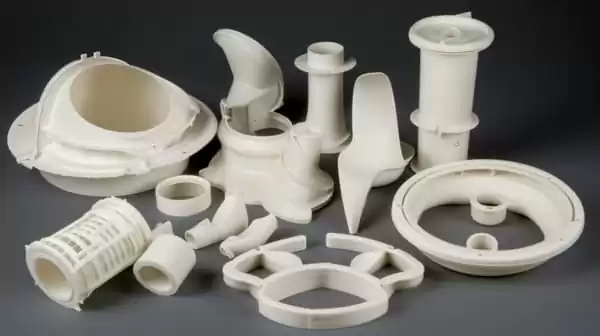
3.Addressing the Advantages of Thermoforming (Vacuum Forming) vs. Injection Molding:
Thermoforming, specifically vacuum forming, excels in cost efficiency, especially for low to medium volume production and prototyping.
It offers the advantage of quicker tooling setup, making it a viable option when faster turnaround times are desired.
Vacuum forming is particularly suited for creating large-scale designs and parts with simpler geometries.
4.Unique Aspects and Applications:
Vacuum Forming: Vacuum forming allows for the creation of large, shallow plastic parts, making it suitable for applications such as trays, packaging, automotive components, and point-of-sale displays.
Injection Molding: Injection molding’s precision, repeatability, and ability to produce intricate designs make it a preferred choice for industries requiring high-quality components, including toys, medical devices, consumer electronics, automotive parts, and packaging.
Both vacuum forming and injection molding have their unique strengths and applications. Understanding these advantages and unique aspects enables manufacturers to select the most suitable process based on factors such as cost, volume, complexity, precision, material requirements, and lead times. By leveraging the benefits of each method, businesses can optimize their plastic manufacturing processes and achieve the desired outcomes for their specific projects.
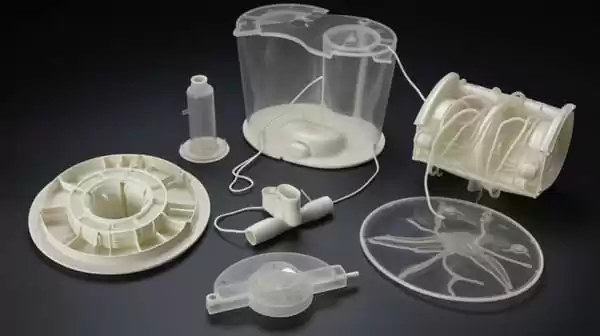
Conclusion:
In conclusion, understanding the differences and advantages of vacuum forming and injection molding enables manufacturers to make informed decisions. By selecting the appropriate manufacturing process, businesses can meet their specific requirements, enhance product quality, control costs, and ultimately thrive in their respective industries.