Introduction
Vacuum forming is a widely used manufacturing process that involves shaping plastic sheets into various products. It is a versatile and cost-effective method utilized in industries ranging from packaging to automotive. Choosing the right plastic material for vacuum forming is crucial to ensure the desired results and product quality. In this article, we will explore the importance of vacuum forming and discuss the key factors to consider when selecting the appropriate plastic for this process.
Vacuum forming, also known as thermoforming, is a manufacturing technique that utilizes a combination of heat and pressure differentials to shape plastic sheets into desired forms. This process involves heating a plastic sheet until it becomes pliable, placing it over a mold, and applying vacuum pressure to form it to the mold’s shape. Once the plastic cools and solidifies, it retains the desired shape, resulting in a finished product.
The importance of vacuum forming lies in its versatility and cost-effectiveness. It allows for the production of a wide range of products, from simple packaging containers to complex parts for various industries. Vacuum forming offers advantages such as high production speed, low tooling costs, design flexibility, and the ability to create prototypes or produce large quantities of items.
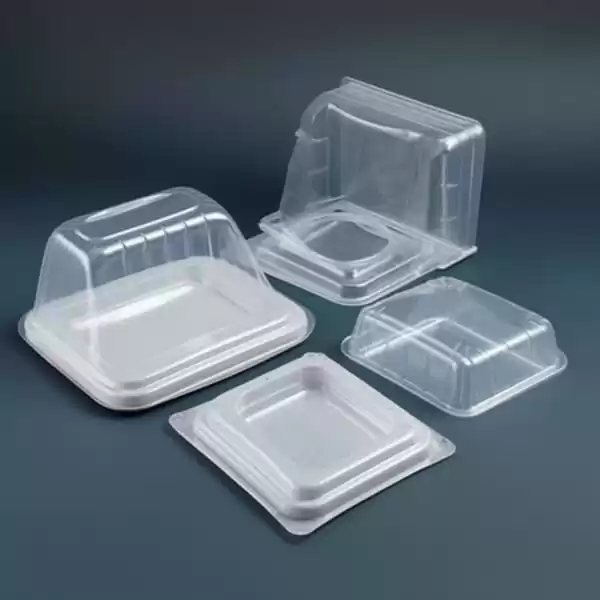
II. Understanding the Vacuum Forming Process
A. Explanation of the vacuum forming process:
Vacuum forming is a manufacturing process used to shape plastic sheets into various products. The process involves several steps:
- Heating: The plastic sheet, typically made of materials like ABS or PETG, is heated until it becomes pliable and softens. This can be done using a heat source such as heating elements or infrared heaters.
- Placement: Once heated, the plastic sheet is positioned over a mold or a positive impression of the desired shape.
- Vacuum Pressure: A vacuum is applied to the mold, creating a pressure differential between the mold and the sheet. This pressure differential causes the softened plastic to be drawn tightly onto the mold’s contours, taking the shape of the mold.
- Cooling and Solidification: The vacuum-formed plastic is allowed to cool, which solidifies it into the desired shape. Cooling can be expedited by using fans or water cooling methods.
- Removal: Once the plastic has completely cooled and solidified, it is removed from the mold, resulting in the finished vacuum-formed product.
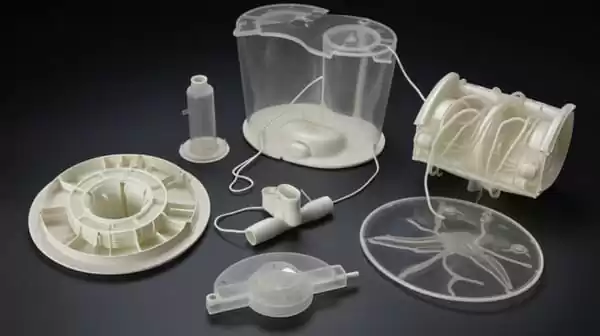
B. Role of Vacuum Forming Machines:
Diy Vacuum forming machines play an essential part in the makes vacuum forming process, automating and streamlining it for increased efficiency and consistency. A typical machine typically comprises of the following components:
Heating Element: This element heats the plastic sheet to an appropriate temperature for softening and shaping purposes.
Frame and Clamping System: The frame serves as structural support while the clamping system holds plastic sheets securely during structural foam forming process.
Mold or Tooling: A mold can be constructed out of various materials like wood or aluminum to produce the desired form for plastic molding.
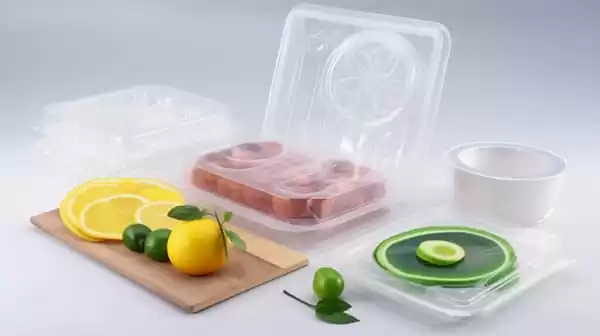
Vacuum System: To effectively pull plastic sheets onto molds, vacuum systems create the required pressure differential.
Cooling System: After the formation process is completed, the cooling system helps the plastic sheet solidify quickly and cool off more rapidly.
C. Key Components Involved in Vacuum Forming:
Along with a vacuum forming machine, other key components play an essential part in vacuum forming. For instance:
Plastic Sheet: Plastic sheets come in various thicknesses and materials for vacuum forming applications, making it the ideal raw material. However, its selection should depend on your application requirements.
Mold Design: To produce the desired shape for the final product, molds or tooling must be designed carefully so as to achieve accurate and consistent results.
Vacuum Pressure Regulation: When forming, vacuum pressure needs to be carefully managed so as to achieve uniform material distribution and adhesion to the mold.
Understanding the vacuum forming process and key components involved are integral parts of its successful implementation. Together they work to shape plastic sheets into high-quality vacuum formed products.
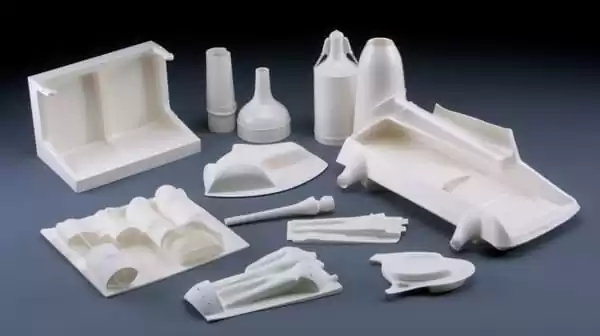
III. Factors to Consider When Choosing the Right Plastic for Vacuum Forming
A. Importance of considering the application and requirements:
When selecting the plastic for vacuum forming, it is crucial to consider the specific application and requirements of your project. Different applications may require different properties from the plastic, such as strength, flexibility, heat resistance, transparency, or chemical resistance. Understanding the application and its specific demands will help you choose the most suitable plastic material.
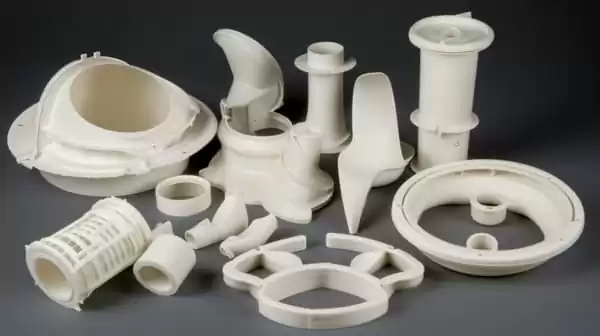
B. Evaluation of material properties:
To choose the right plastic for vacuum forming, it is essential to evaluate the material properties. Here are some commonly used plastics for vacuum forming:
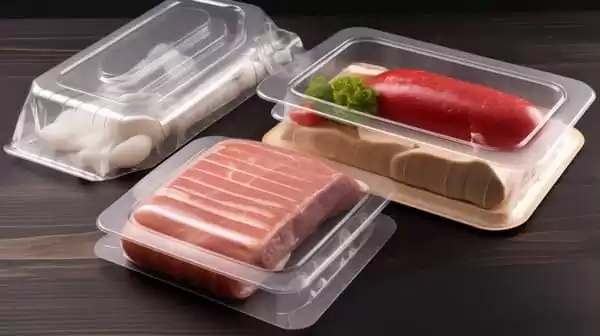
ABS (Acrylonitrile Butadiene Styrene):
Excellent impact resistance and toughness
Affordability
Widely used for prototypes, automotive parts, and consumer products
PETG (Polyethylene Terephthalate Glycol):
Excellent clarity and transparency
Chemical resistance
mpact strength
Used for display cases, medical packaging, and point-of-sale displays
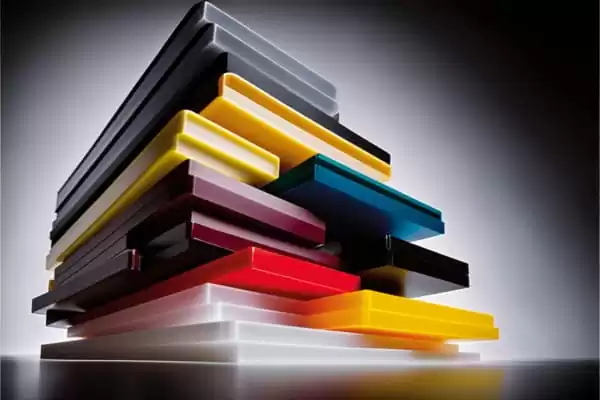
PVC (Polyvinyl Chloride):
Rigid and durable
Good chemical resistance
Electrical insulation properties
Commonly used for pipes, fittings, and signag
C. Ensuring food-grade plastics for food packaging applications:
If your vacuum forming project involves using food containers or packaging, it is essential to ensure that the plastic material is food-grade. Food-grade plastics are specifically designed and manufactured to be safe for contact with food, meeting regulatory requirements. They are free from harmful substances and have undergone proper testing to ensure food safety.
Choosing food-grade plastic is crucial to prevent any potential contamination of the packaged food. Look for plastic materials that are explicitly labeled as food-grade or meet relevant certifications and regulations, such as FDA (Food and Drug Administration) approval in the United States or EU food contact regulations in Europe.
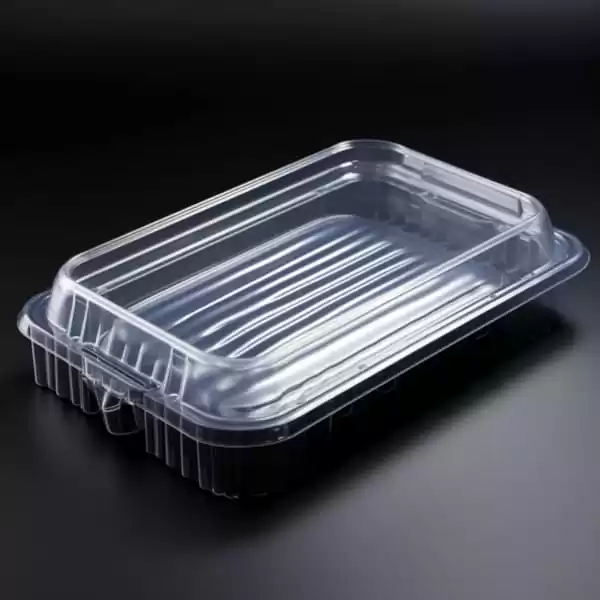
Considering the application and requirements, evaluating material properties, and ensuring food-grade plastics for food packaging applications will help you select the most appropriate plastic material for your vacuum forming project. By choosing the right plastic, you can ensure the desired performance, quality, and safety of the final vacuum-formed products.
IV. Determining the Thickness of the Plastic Sheet
A. Importance of thickness in vacuum forming:
The thickness of the plastic sheet used in vacuum forming plays a crucial role in the success of the process and the quality of the final product. The right thickness ensures proper material distribution, structural integrity, and desired functionality of the vacuum-formed part. It affects factors such as strength, flexibility, and dimensional accuracy.
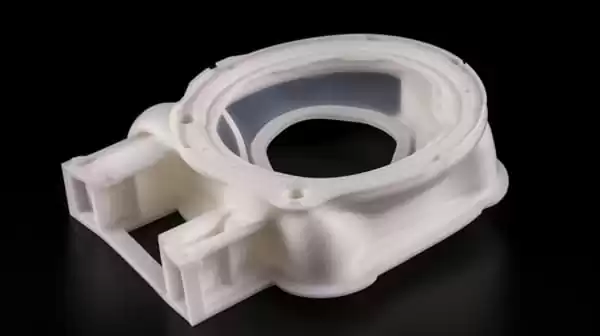
B. Factors influencing the thickness selection:
Several factors influence the selection of the appropriate thickness for the plastic sheet in vacuum forming:
- Size and complexity of the part: Larger and more complex parts often require thicker plastic sheets to maintain structural integrity during the forming process and subsequent use.
- Strength requirements: Consider the strength needed for the final product. Depending on the application, thicker plastic sheets may be necessary to withstand stresses and ensure durability.
- Flexibility requirements: Thinner plastic sheets offer increased flexibility and are suitable for parts that require bending or flexibility.
- Mold intricacy: If the mold has intricate details or sharp corners, thinner plastic sheets may be more suitable as they can better conform to the mold’s contours.
C. Typical range of thickness for vacuum forming:
The thickness of plastic sheets used in vacuum forming typically ranges from 0.5mm to 6mm (0.020″ to 0.236″). However, the optimal thickness depends on the specific requirements of the project.
- Thinner sheets (0.5mm to 2mm): Suitable for smaller, less complex parts, and applications where flexibility is required.
- Medium thickness sheets (2mm to 4mm): Commonly used for general vacuum forming applications, offering a balance between flexibility and structural integrity.
- Thicker sheets (4mm to 6mm): Ideal for larger parts, parts that require additional strength, or applications where rigidity is essential.
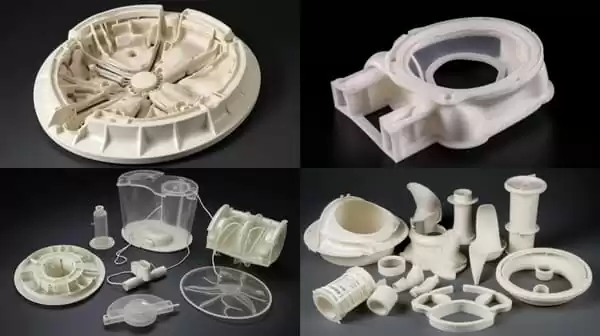
It’s important to note that the appropriate thickness may vary depending on the specific project requirements, so it’s essential to evaluate each project individually and consider factors such as part size, complexity, strength, and flexibility requirements.
By carefully considering these factors, you can determine the optimal thickness of the plastic sheet for vacuum forming, ensuring successful outcomes and high-quality vacuum-formed products.
V. Selecting the Suitable Material for Vacuum Forming Molds
A. Materials Used for Vacuum Forming Molds:
When it comes to selecting materials for vacuum forming molds, there are various options available. Common materials for these molds include:
Wood:
Wood vacuum forming molds are an economical option that’s often chosen for DIY projects and low-cost applications, offering easy shaping, modification and workability. While wooden molds may offer durable performance with limited precision or durability concerns.
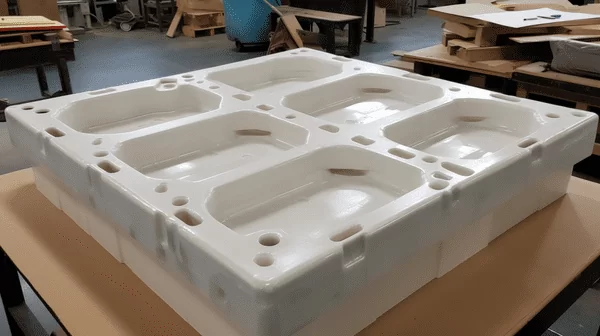
Aluminum:
Aluminum molds are widely utilized for industrial vacuum forming machines. Their excellent durability, thermal conductivity and ability to produce high-quality finishes makes them suitable for high volume production, with repeated usage being no problem at all.
Composite Materials:
Vacuum forming molds often use composite materials like fiberglass reinforced plastic (FRP) or epoxy tooling board as they offer superior durability, dimensional stability and the ability to form complex shapes with ease. Composite molds are commonly utilized for high precision and high temperature applications.
B. Considerations for choosing the mold material:
When selecting the material for a vacuum forming mold, consider the following factors:
Project Requirements:
Assess the specific requirements of your project, including the complexity of the part, expected production volume, and desired finish. Certain materials may be better suited for particular applications.

Durability:
Consider the expected lifespan and durability required for the mold. Industrial vacuum forming applications often require molds that can withstand repetitive use and maintain shape accuracy over time.
Precision and Detail:
If your project involves intricate details or sharp corners, you may require a mold material that can accurately reproduce those features.
Temperature Resistance: Evaluate the temperature requirements of your vacuum forming process. Some materials, like aluminum, offer good thermal conductivity and can withstand higher temperatures.
Cost:
Consider the budget for your project. Wood molds are generally more cost-effective, while aluminum and composite molds may offer greater precision but come at a higher cost.
Machinability:
If you plan to modify or shape the mold, consider the ease of working with the chosen material. Some materials may be easier to machine or modify than others.
By carefully considering these factors, you can select the most suitable material for your vacuum forming mold. The chosen material should meet the specific requirements of your project, ensuring durability, precision, and desired outcomes in the vacuum forming process.
VI. Applications of Vacuum Forming
A. Wide range of industries utilizing vacuum forming:
Vacuum forming is a versatile manufacturing process used in various industries. Its ability to create customized shapes and cost-effective production make it a popular choice. Some of the industries that utilize vacuum forming include:
Packaging:
Vacuum forming is extensively used in the packaging industry, particularly for food packaging and consumer goods. It allows for the creation of custom-shaped trays, blister packs, and clamshells to securely hold and display products.
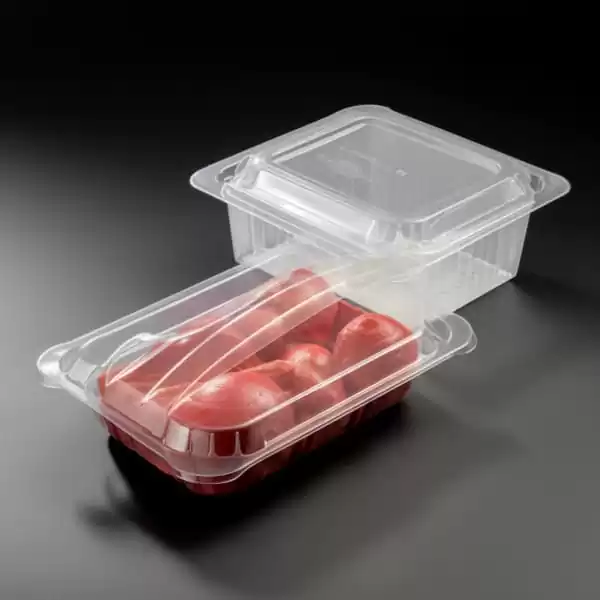
Industrial:
Vacuum forming finds applications in industrial settings for producing machine housings, enclosures, and protective covers. It offers cost-effective solutions for custom parts that require durability and protection.
Medical:
The medical industry relies on vacuum forming for sterile packaging, trays, and protective covers. Vacuum-formed products ensure the safety and cleanliness of medical equipment and devices.
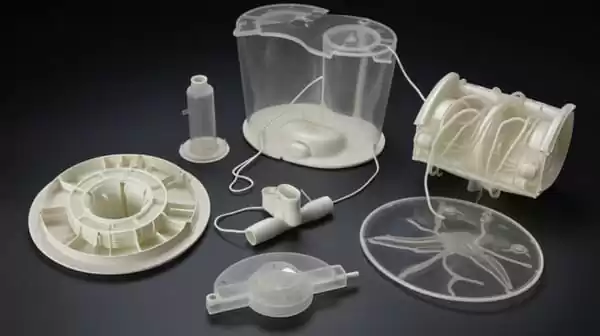
Automotive:
Vacuum forming is utilized in the automotive industry to produce interior components, such as dashboards, door panels, and trim pieces. It enables the creation of complex shapes and customized designs.
Aerospace:
Vacuum forming is employed in the aerospace industry for creating lightweight components, interior panels, and protective covers. Its ability to produce parts with reduced weight is valuable in this sector.
B. Examples of applications:
Food Packaging:
Vacuum forming is commonly used to create various food storage containers, packaging containers, trays, and blister packs. It ensures proper protection, hygiene, and display of food products.
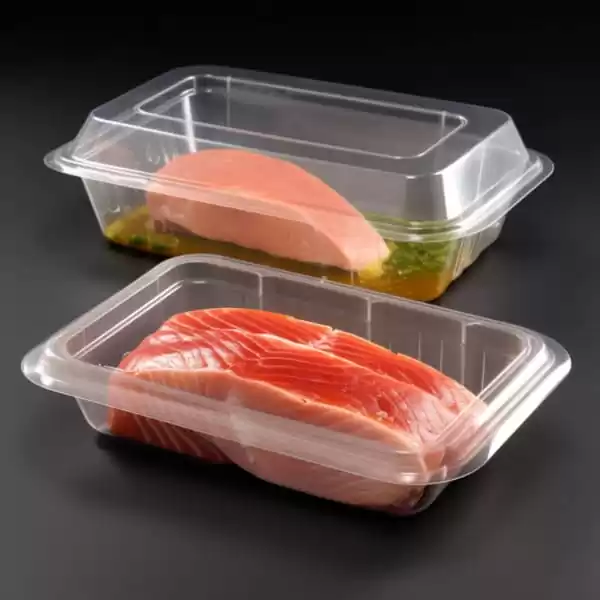
Industrial Machines:
Vacuum forming produces parts for machine housings, enclosures, and guards used in various industrial machines. These parts provide protection, functionality, and customization.
Medical Packaging:
Vacuum-formed trays and packaging are widely used in the medical industry for sterile packaging and protection of medical devices and instruments.
Automotive Components:
Vacuum forming is employed to manufacture interior components such as dashboards, door panels, and trim pieces in the automotive industry.
These examples showcase the versatility of how vacuum forming is used in various industries. Its ability to create custom shapes, cost-effectiveness, and ease of production make it a valuable manufacturing process for a wide range of applications.
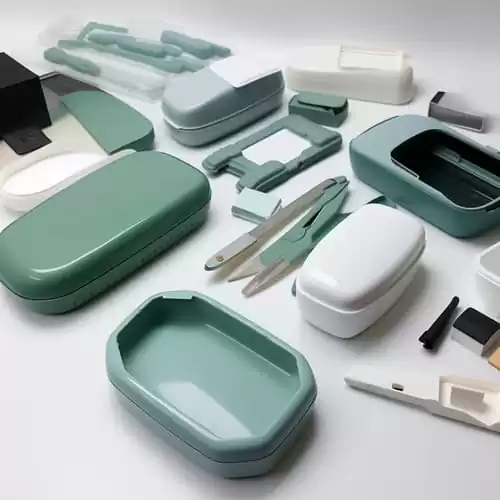
By understanding the applications of vacuum forming, industries can utilize this process to produce high-quality and custom-designed products, reducing costs and improving efficiency.
Conclusion
In conclusion, we have explored the key factors to consider when choosing the right plastic for vacuum forming. By recapitulating the key points discussed, we can emphasize the importance of this process and the significance of selecting the appropriate plastic material.
Firstly, we discussed the vacuum forming process, which involves heating a plastic sheet, placing it over a mold, and shaping it using vacuum pressure. We also highlighted the role of a vacuum forming machine and the key components involved in this manufacturing technique.
Next, we emphasized the importance of considering the application and requirements of your project when selecting the plastic material. Evaluating the material properties is crucial, and we discussed some commonly used plastics for vacuum forming, including ABS, PETG, and PVC. Each of these materials offers unique properties suitable for different applications.
Furthermore, we stressed the significance of ensuring food-grade plastics for food packaging applications to comply with safety regulations and protect consumers.
Determining the appropriate thickness of the plastic sheet is vital, and we explored the factors that influence the thickness selection. Thinner sheets are suitable for smaller and less complex parts, while thicker sheets are ideal for larger and more structurally demanding applications.
Additionally, we addressed the selection of suitable materials for vacuum forming molds. Wood, aluminum, and composite materials were identified as common options, with considerations for factors such as project requirements, durability, precision, and temperature resistance.
Lastly, we concluded by encouraging readers to consider the specific requirements of each project. By carefully evaluating the application, material properties, thickness, and mold material, one can select the most suitable components for successful vacuum forming.
Choosing the right plastic for vacuum forming is crucial to achieve the desired results and ensure the quality of the final products. By considering these factors and tailoring them to the project at hand, manufacturers can optimize their vacuum forming and manufacturing processes and create high-quality, custom-designed products.
In summary, understanding the importance of choosing the right plastic for your vacuum forming work and considering the specific requirements of each project are key to achieving successful outcomes. By following these guidelines, manufacturers can ensure efficiency, cost-effectiveness, and quality in their vacuum forming endeavors.