Introduction
Vacuum forming is a versatile manufacturing process widely used in various industries. It involves shaping a heated melted plastic sheet over a mold using vacuum pressure. This technique finds applications in industries such as packaging, automotive, and medical equipment. In this article, we will explore the different types of plastics suitable for vacuum forming. Understanding the characteristics of these plastics is crucial for achieving successful vacuum forming outcomes and meeting specific application requirements. So, let’s dive into the world of vacuum forming and discover the optimal plastics for this innovative manufacturing process.
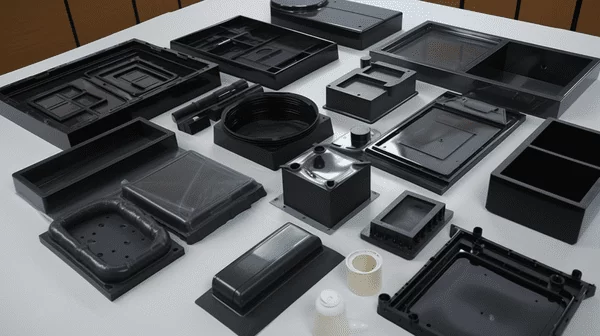
II. Overview of the Vacuum Forming Process
Vacuum forming is a fascinating process that involves transforming a heated plastic sheet into a desired shape by stretching it over a mold using vacuum pressure forming. Let’s explore the steps involved in the vacuum forming process and understand the role of plug assisted vacuum forming machines in this intricate procedure.
A. Explanation of the Vacuum Forming Process
- Heating the Plastic Sheet:Before the vacuum forming begins, a structural foam plastic sheet, typically made of materials like PVC, PET, PS, HDPE, or PP, is heated to a pliable state. This heating process can be accomplished using various methods, including ceramic heaters or digital power controls, which ensure a controlled and uniform heating temperature.
- Stretching the Sheet over a Mold Using Vacuum Pressure:Once the plastic sheet reaches the desired forming temperature, it is carefully positioned above a mold. The mold can have a concave or convex shape, depending on the desired end product. When the mold and the plastic sheet are properly aligned, the vacuum forming process begins. A vacuum pump connected to the vacuum forming machine removes the air from the space between the plastic sheet and the mold. As the air is evacuated, atmospheric pressure pushes the heated sheet against the mold’s surface, conforming it to the desired shape.
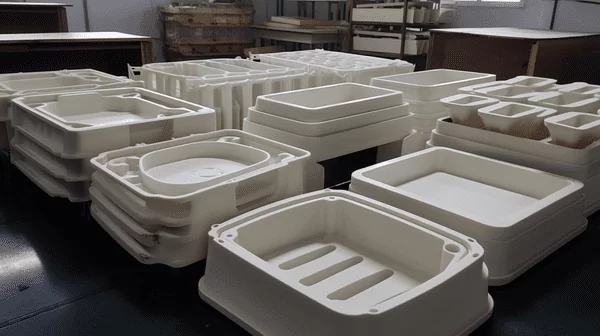
B. Description of Vacuum Forming Machines and Their Operation
- Role of Vacuum Pumps and Vacuum Reservoirs:Vacuum pumps play a crucial role in creating the necessary suction force for the vacuum forming process. These pumps remove air from the forming area, generating the required vacuum pressure to mold the plastic sheet. Vacuum reservoirs are often utilized to maintain a consistent vacuum level during the forming process.
- Types of Machines: Single Heater vs. Double Heater Machines:Vacuum forming machines come in various configurations, but two common types are single heater machines and double heater machines. Single heater machines typically have a single heating element for the plastic sheet, making them suitable for simpler projects. On the other hand, double heater machines feature two heating elements, allowing for more precise control over the heating process and enabling the formation of more complex shapes.
- Temperature Controlling Systems and Cooling Processes:Vacuum forming machines are equipped with temperature controlling systems to ensure the plastic sheet reaches the optimal forming temperature. These systems monitor and regulate the heat throughout the process. After the forming is complete, cooling processes, such as fans or water jets, help solidify the molded plastic sheet and maintain its shape.
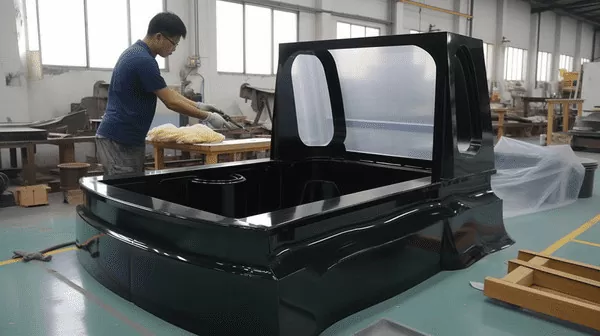
Understanding the vacuum forming process and the components of vacuum forming machines is essential for achieving successful and consistent results. The precise control over temperature, vacuum pressure, and cooling ensures the production of high-quality vacuum formed products.
III. Types of Plastics Used in Vacuum Forming
A. Polystyrene (PS):
The Most Commonly Used Polymer for Vacuum Forming Polystyrene (PS) is one of the most commonly used polymers in vacuum forming. It is a versatile and cost-effective plastic material that is widely available. PS offers good impact resistance and clarity, making it suitable for a variety of applications. It is frequently used in the production of thin-walled food containers, plastic packaging, and even medical trays through the vacuum forming process. The ease of processing and availability of PS make it a popular choice for manufacturers.
B. High-Density Polyethylene (HDPE):
Plastic Materials Suitable for School-Based Vacuum Forming For school-based vacuum forming projects, a suitable plastic choice is High-Density Polyethylene (HDPE). HDPE is a thermoplastic material known for its durability and chemical resistance. It is commonly used in DIY vacuum forming machines and is suitable for creating plastic boxes, food storage containers, and other educational projects. HDPE is a safe and cost-effective option for vacuum forming mold in school settings due to its availability and ease of use.
C. Usability of HDPE in Vacuum Forming
HDPE can be successfully used in vacuum forming processes. Its high density and strength make it suitable for producing sturdy vacuum formed products. HDPE’s excellent chemical resistance also makes it an excellent choice for applications in medical packaging and food containers. With its versatility and affordability, HDPE provides a reliable option for vacuum forming applications where durability and chemical resistance are essential.
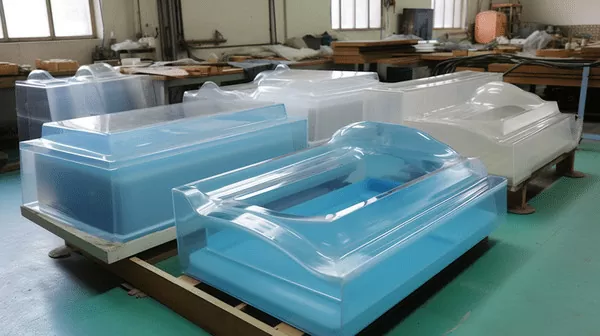
By considering the properties and characteristics of different plastic materials, manufacturers and educators can choose the most suitable plastic for their vacuum forming needs. Polystyrene (PS) is commonly used for its versatility, while High-Density Polyethylene (HDPE) is a popular choice for school-based projects. Understanding the usability of HDPE and its benefits in vacuum forming ensures successful and safe outcomes in various applications.
IV. Plastic Choices for Thermoforming
A. Polypropylene (PP) Is an Excellent Choice for Thermoforming
Polypropylene (PP) is one of the best plastic choices when it comes to thermoforming. As a thermoplastic material, PP offers excellent properties for thermoforming. This material can also be found widely used in industrial and vacuum forming machines operate a machine for producing plastic parts with complex shapes at great quality levels.
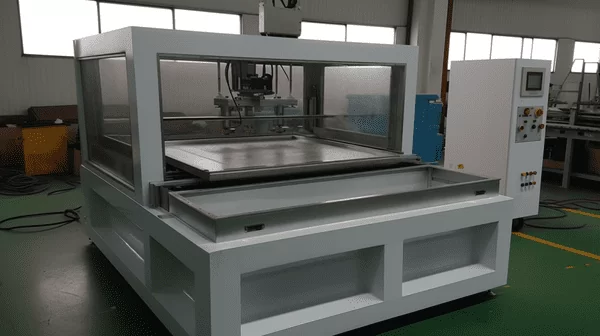
B. Properties of Polypropylene (PP) Conducive to Thermoforming
Polypropylene (PP) offers several features that make it highly suitable for thermoforming applications:
Impact Resistance: Polypropylene has excellent impact resistance, enabling it to withstand external forces while keeping its structure intact.
Dimensional Stability: Polypropylene thermoforming retains its shape and dimensions throughout the thermoforming process, leading to accurate and consistent part production.
Wide Processing Window: Polypropylene has an ideal temperature range for thermoforming techniques, making PP an excellent material to work with.
Chemical Resistance: PP boasts excellent chemical resistance, making it suitable for applications that involve contact with various substances.
Versatility: Due to its versatility and adaptability to various design specifications, polypropylene (PP) can be used to produce an array of products including automotive parts, electronic housings and medical devices.
Polypropylene (PP) thermoforming provides high-quality parts with superior impact resistance, dimensional stability, chemical resistance, and versatility. Additionally, its wide processing window enables efficient production – making PP an attractive plastic choice in numerous industrial applications.
V. Vacuum Forming Common Queries
A. Which Polymer Is Most
Commonly Used for Vacuum Forming? One of the most frequently utilized polymers for vacuum forming plastic is polystyrene (PS). PS is a cost-effective plastic material readily available that features good impact resistance and clarity – characteristics which make it suitable for an array of uses such as thin-walled food containers, plastic packaging and medical tray production through vacuum forming processes.
B. What Type of Plastic Is Commonly Employed for School-Based Vacuum Forming?
HDPE (High-Density Polyethylene) is a popular material choice in school-based vacuum forming projects due to its durability and chemical resistance, making it suitable for DIY vacuum forming machines used for creating plastic boxes, food storage containers, or other educational projects. Furthermore, due to its ease of use in school settings, HDPE provides both safety and cost efficiency makes vacuum forming everywhere.
C. Can HDPE Be Used in Vacuum Forming?
HDPE can certainly be used in vacuum forming. Due to its high density and strength, HDPE makes a good material choice for creating durable vacuum formed products with excellent chemical resistance – ideal for medical packaging applications and food containers. Versatility and affordability make HDPE an economical and dependable option when durability and chemical resistance are crucial features in vacuum formed products.
D. Which Plastic Is Best for Thermoforming?
When it comes to thermoforming, polypropylene (PP) is one of the premier plastic choices. With excellent impact resistance and dimensional stability properties as well as a broad temperature processing range, PP is widely used in industrial vacuum forming machines to produce complex parts with intricate shapes with ease. Due to its versatility and adaptability, PP makes an excellent material choice for automotive components, electronic housings and medical devices among other uses.
By exploring these frequently asked questions about vacuum forming and plastic thermoforming applications, we can gain a better understanding of which polymers are widely used, appropriate choices for school projects, HDPE usability in vacuum forming applications and the optimal plastics to use when thermoforming applications are desired.
Conclusion
In conclusion, vacuum forming is a versatile manufacturing process that utilizes a vacuum to shape a heated plastic sheet over a mold. By exploring the different types of plastics suitable for vacuum forming, we have gained valuable insights into selecting the right materials for successful outcomes.
Polystyrene (PS) is commonly used in vacuum forming due to its versatility and cost-effectiveness. High-Density Polyethylene (HDPE) is a popular choice for school-based projects, offering durability and chemical resistance. HDPE can also be utilized effectively in industrial vacuum forming applications.
For thermoforming, polypropylene (PP) stands out as the best plastic choice. It offers excellent impact resistance, dimensional stability, and a wide processing temperature range, making it ideal for producing high-quality parts with complex shapes.
The importance of selecting the appropriate plastic for vacuum forming applications cannot be overstated. Different plastics possess unique properties, such as impact resistance, chemical resistance, and clarity, which directly affect the performance and functionality of the final vacuum formed products. By understanding the characteristics and suitability of various plastics, manufacturers and designers can ensure the desired outcomes for their specific applications.
In summary, the selection of the right plastic material is crucial for achieving successful vacuum forming results. By considering factors such as impact resistance mold surface, dimensional stability, chemical resistance, and processing temperature range, we can make informed decisions and produce high-quality vacuum formed products that meet the requirements of various industries, from packaging to automotive and beyond.