Introduction:
Vacuum forming is an established manufacturing method used to form plastic sheets into various products. It involves heating a sheet of plastic before molding it under vacuum conditions until reaching its desired shape. Vacuum forming provides versatile, cost-effective ways of creating simple or complex shaped objects. In this article, we’ll explore how vacuum forming heats the plastic sheet during its formation process while answering some frequently asked questions about this form of manufacturing. Let us explore how vacuum forming works, the role heat plays in its process, suitable plastic sheets for vacuum forming and how you can straight vacuum forming to form plastic. Join us and explore its secrets behind heating.
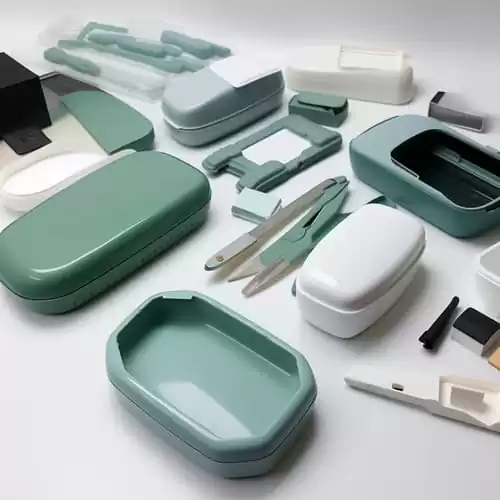
II. How Does Vacuum Forming Plastic Work?
Vacuum forming is a manufacturing process that utilizes the principles of heat and pressure differentials to shape plastic sheets into various forms. Let’s explore the key steps involved in the vacuum-forming work process:
Preparation:
The process begins with the creation of molds, typically made from wood, aluminum, or other materials, depending on the complexity and requirements of the desired shape.
The vacuum forming machine is set up, including the installation of heating heaters and the positioning of the mold.
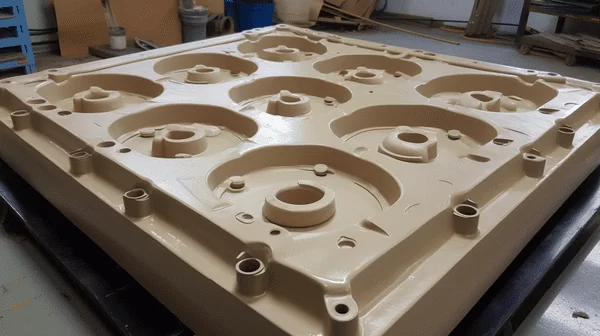
Loading the Plastic Sheet:
A plastic heated sheet, known as a thermoplastic sheet, is selected based on the desired properties of the final product. Common thermoplastic materials used include acrylonitrile butadiene styrene (ABS), polyvinyl chloride (PVC), and polyethylene terephthalate glycol (PETG).
The plastic heated sheet is loaded onto the vacuum-forming machine and secured in place.
Heating the Plastic Sheet:
The loaded plastic sheet is heated using heaters positioned above and below the sheet.
The heaters emit heat, causing the plastic sheet to gradually soften and become pliable.
The heating temperature and duration depend on the type and thickness of the plastic material.
Creating a Vacuum and Forming the Plastic:
Once the plastic sheet reaches the appropriate forming temperature, the vacuum forming machine initiates the vacuuming process.
The machine activates a vacuum pump, which removes the air from the space beneath the plastic sheet.
The atmospheric pressure exerted on the top surface of the plastic sheet causes it to conform to the shape of the mold, creating the desired form.
The vacuum pressure ensures the plastic sheet adheres tightly to the mold, capturing intricate details and contours.
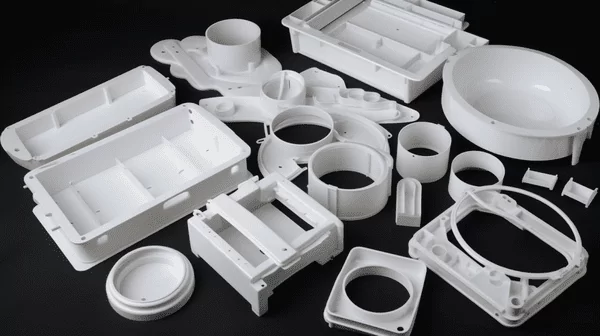
Cooling and Releasing the Formed Plastic Part:
After the plastic sheet has taken the desired shape, a cooling phase begins.
The mold may have cooling elements or be placed in a cooling chamber to expedite the cooling process.
Once the formed plastic part has cooled and solidified, the vacuum and pressure forming part is released, and the mold and formed part are separated.
The excess material or webbing around the formed part is trimmed off using tools such as mechanical trim presses.
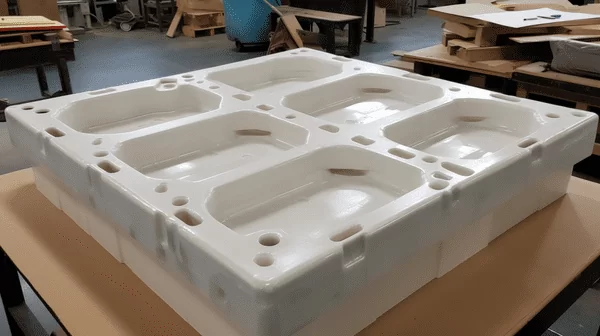
By following these steps, vacuum forming allows for the efficient production of various plastic parts and products, offering versatility in design and cost-effective manufacturing capabilities.
III. Does Vacuum Forming Use Heat?
Heat is a crucial component in the vacuum forming process, playing a vital role in shaping the plastic sheet into the desired form. Let’s explore the significance of heat and how it softens the plastic sheet for molding:
Softening the Plastic Sheet:
The plastic sheet used in vacuum forming is typically a thermoplastic material, which means it can be softened and molded when subjected to heat.
Heating the plastic sheet to an appropriate temperature allows the polymer chains within the material to become more mobile, reducing its viscosity and increasing its flexibility.
As the plastic sheet reaches its forming temperature, it transitions from a rigid state to a pliable state, making it easier to shape.
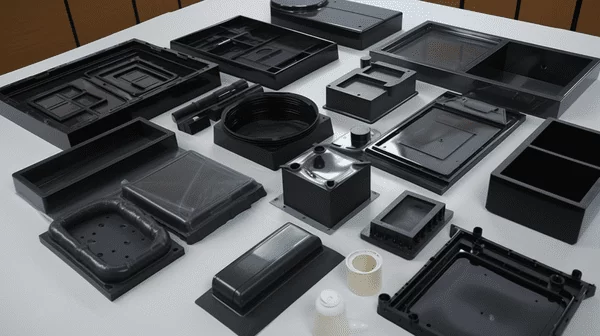
Enhancing Conformity to the Mold:
By applying heat, the plastic sheet becomes more malleable, enabling it to conform closely to the shape of the mold.
The increased temperature makes the plastic more receptive to external forces, allowing it to stretch and take on intricate details of the mold’s surface.
Heat softens the plastic, enabling it to flow and adhere tightly to the contours and features of the mold, resulting in accurate reproduction of the desired form.
Controlling Heating Parameters:
The temperature, air pressure and duration of heating are critical factors in the vacuum forming process.
Different types of thermoplastic materials have specific heating requirements to achieve the optimal forming temperature.
Heating too little or too much can affect the quality and integrity of the final formed part.
Manufacturers carefully regulate the heating parameters to ensure consistent and uniform heating across the entire plastic sheet.
Heating Methods:
Vacuum forming machines employ various heating methods, such as radiant heating elements, infrared heaters, or heating plates, to heat the plastic sheet.
The heaters are strategically positioned above and below the plastic sheet to achieve even heating and uniform softening.
In summary, heat is a fundamental element in vacuum forming as it softens the plastic sheet, making it pliable and capable of conforming to the mold’s shape. By controlling the heating parameters and utilizing appropriate heating methods, manufacturers can achieve precise and consistent results in the vacuum forming process.
IV. What Plastic Sheet is Suitable for Vacuum Forming?
When it comes to vacuum forming, selecting the right plastic sheet is crucial for achieving successful and high-quality results. Let’s explore an overview of the plastic materials commonly used in vacuum forming and the factors to consider when choosing a plastic sheet:
Commonly Used Plastic Materials:
Acrylonitrile Butadiene Styrene (ABS): ABS sheets are popular due to their versatility, impact resistance, and ability to be easily colored or textured.
Polyvinyl Chloride (PVC): PVC sheets are known for their excellent rigidity, chemical resistance, and affordability.

Polyethylene Terephthalate Glycol (PETG): PETG sheets offer clarity, toughness, and resistance to impact and chemicals, making them suitable for transparent applications.
High Impact Polystyrene (HIPS): HIPS sheets are lightweight, rigid, and cost-effective, often used for packaging and display purposes.
Polypropylene (PP): PP sheets are known for their excellent chemical resistance, durability, and flexibility, suitable for a wide range of applications.
Factors to Consider:
Material Properties: Different plastic materials possess varying properties such as rigidity, flexibility, impact resistance, transparency, and chemical resistance. Consider the specific requirements of the final product to determine which material best suits the application.
Forming Temperature: Each plastic material has an optimal forming temperature range. Ensure the selected plastic sheet can be heated to the required temperature without degrading or experiencing undesirable changes in properties.

Wall Thickness: Thicker plastic sheets require longer heating times and higher temperatures to reach the optimal forming state. Consider the desired wall thickness of the final product and ensure the selected plastic sheet can accommodate it.
Compatibility with Mold: Evaluate how well the plastic material can conform to the mold’s shape, including intricate details and undercuts. Certain materials, like ABS or PETG, are more suitable for complex molds due to their flexibility.
Desired Surface Finish: Different plastic materials offer varying surface finishes, ranging from glossy to matte. Consider the aesthetic requirements of the final product and select a plastic sheet that aligns with the desired surface appearance.
Cost Considerations: Plastic materials vary in cost, so it’s essential to consider the budget constraints of the project while maintaining the desired quality and functionality.
By carefully considering the material properties, forming temperature, wall thickness, mold compatibility, surface finish, and cost, you can choose a plastic sheet that is suitable for vacuum forming, ensuring successful outcomes and meeting the specific requirements of your project.
V. How Do You Vacuum Form Plastic Step by Step?
Vacuum forming plastic involves a series of well-defined steps to ensure the successful creation of molded parts. Here is a step-by-step guide on how to vacuum form plastic:
a. Preparation:
- Create Molds: Design and construct molds using suitable materials such as wood, aluminum, or 3D-printed molds. The molds should match the desired shape and dimensions of the final product.
- Set Up Heating Elements: Install and position heating elements, such as radiant heaters or heating plates, above and below the vacuum forming machine’s workspace. Ensure even heat distribution and proper alignment with the plastic sheet.
- Select Plastic Sheet: Choose an appropriate thermoplastic sheet based on the desired properties and requirements of the final product. Common options include ABS, PVC, PETG, HIPS, or PP sheets.
b. Loading the Plastic Sheet:
- Secure the Mold: Place the mold onto the vacuum forming machine’s platform, ensuring it is centered and aligned correctly.
- Position the Plastic Sheet: Carefully lay the selected plastic sheet over the mold, ensuring it covers the entire mold surface with some excess material extending beyond the mold’s outer dimensions.
- Clamp Frame: Secure the plastic sheet in place by lowering a clamp frame over the plastic sheet and mold, creating a seal to prevent air leakage during the vacuuming process.
c. Heating the Plastic Sheet:
- Activate Heating Elements: Power on the heating elements located above and below the plastic sheet.
- Heat the Sheet: Allow the heating elements to raise the temperature of the plastic sheet gradually. The heating duration and temperature depend on the specific type and thickness of the plastic material being used. Refer to material guidelines for appropriate heating parameters.
- Monitor Heating Progress: Observe the plastic sheet’s behavior as it heats up, ensuring it softens uniformly and reaches the ideal forming temperature. Avoid overheating, which can lead to degradation or undesirable changes in the plastic material.

d. Creating a Vacuum and Forming the Plastic:
- Initiate Vacuum Process: Once the plastic sheet has reached the optimal forming temperature, activate the vacuum forming machine’s vacuum system.
- Apply Vacuum Pressure: The vacuum pump generates negative pressure, evacuating the air from beneath the plastic sheet. Atmospheric pressure above the plastic sheet pushes it downward, causing it to conform tightly to the contours of the mold. This creates the desired shape and captures intricate details.
- Mold Adherence: Allow the vacuum to remain active until the plastic sheet has fully conformed to the mold and adhered to its surface. This ensures the creation of accurate and precise formed parts.
e. Cooling and Releasing the Formed Plastic Part:
- Cooling Phase: After forming, cool the plastic part to solidify its shape. This can be done by either cooling the mold directly or using external cooling methods such as fans or a cooling chamber.
- Release Vacuum: Once the formed plastic part has adequately cooled, release the vacuum pressure by deactivating the vacuum pump.
- Separate the Mold and Part: Lift the clamp frame and carefully remove the formed plastic part from the mold. Trim off any excess material or webbing using appropriate vacuum forming tools, such as mechanical trim presses.
By following these step-by-step instructions, you can successfully vacuum form plastic, creating high-quality molded parts with the desired shape and dimensions.
VI. Benefits and Applications of Vacuum Forming process
Vacuum forming is a versatile manufacturing process that offers several advantages, making it widely used across various industries. Let’s explore the benefits of vacuum forming as a manufacturing process and discuss its applications in different fields:
Advantages of Vacuum Forming:
a. Cost-Effective:
Vacuum forming is a cost-effective method for producing plastic parts compared to other manufacturing processes like injection molding. It requires less initial investment in tooling and equipment.
b. Versatility in Design:
Vacuum forming allows for the production of both simple and complex shapes with relative ease. It offers design flexibility and the ability to incorporate intricate details, textures, and undercuts.
c. Rapid Prototyping:
Vacuum forming enables the quick production of prototypes and low-volume production runs, reducing lead times and costs associated with traditional manufacturing processes.
d. Material Selection:
Vacuum forming supports a wide range of plastic materials, including ABS, PVC, PETG, HIPS, and PP, allowing manufacturers to choose materials that meet specific requirements such as durability, transparency, or chemical resistance.
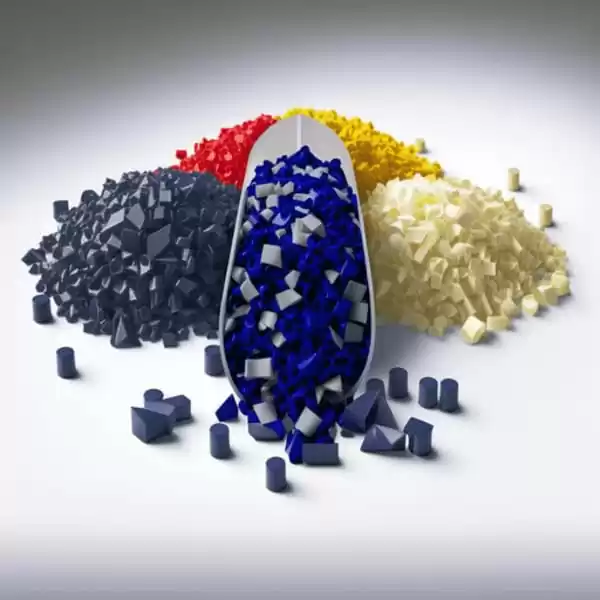
e. Scalability:
Vacuum forming is suitable for both small-scale and large-scale production, making it adaptable to various production volumes and requirements.
f. Customization:
With vacuum forming, it is possible to create custom products tailored to specific customer needs, ensuring personalized solutions.
Applications of Vacuum Forming:
a. Food Packaging:
Vacuum forming offers excellent suitability for food packaging, such as trays, containers, and blister packs. The process allows for precise product placement, protection, and attractive presentation.
b. Medical Equipment:
Vacuum forming is utilized in the production of medical equipment components, such as enclosures, trays, and housings. The process can meet the stringent requirements of the medical industry, including hygiene standards and sterilization compatibility.
c. Automotive Industry:
Vacuum forming is employed to create interior panels, dashboards, and other automotive components. The process offers lightweight alternatives to traditional materials while maintaining durability and aesthetic appeal.
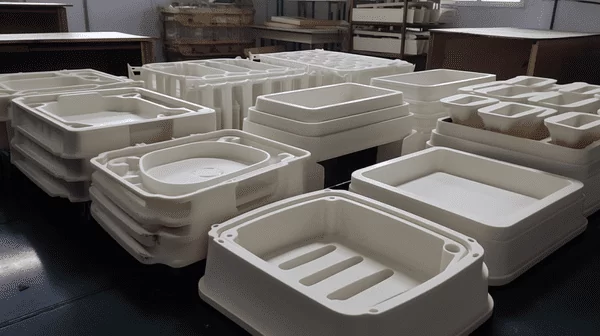
d. Consumer Goods:
Vacuum-formed products find applications in consumer goods such as electronic device enclosures, display stands, point-of-purchase displays, and packaging inserts.
e. Industrial Applications:
Vacuum forming is used to produce parts and components for various industrial applications, including equipment enclosures, protective covers, and machine housings.
f. Building and Construction:
Vacuum-formed plastic sheets are utilized in the production of shower trays, bath panels, interior decor elements, and other building components.
g. Education and Prototyping:
Vacuum forming is often employed in educational settings for teaching manufacturing processes and prototyping various designs, allowing students and designers to bring their ideas to life.
In summary, vacuum forming offers a cost-effective, versatile, and efficient manufacturing process for producing plastic parts. Its applications span across diverse industries, including food packaging, medical equipment, automotive, consumer goods, industrial applications, building and construction, education, and prototyping. By leveraging the benefits of vacuum forming, manufacturers can achieve customized, high-quality products while minimizing production costs and lead times.

Conclusion
Vacuum forming is a manufacturing process that involves shaping plastic sheets by heating and molding them under vacuum conditions.
Heat plays a critical role in vacuum forming as it softens the plastic sheet, making it pliable and allowing it to conform to the shape of the mold.
Proper heating ensures uniform softening of the plastic sheet, enabling it to capture intricate details and contours of the mold’s surface.
Factors such as material selection, forming temperature, wall thickness, and mold compatibility should be considered when choosing a plastic sheet for vacuum forming.
The vacuum forming process consists of preparation, loading the plastic sheet, heating, creating a vacuum, and cooling and releasing the vacuum formed parts and plastic part.
Vacuum forming offers advantages such as cost-effectiveness, design versatility, rapid prototyping, and customization options.
It finds applications in various industries, including food packaging, medical equipment, automotive, consumer goods, and more.
The selection and proper use of vacuum forming tools and equipment, such as tabletop vacuum forming machines, molds, heating elements, vacuum pumps, and trim presses, are crucial for successful vacuum forming.